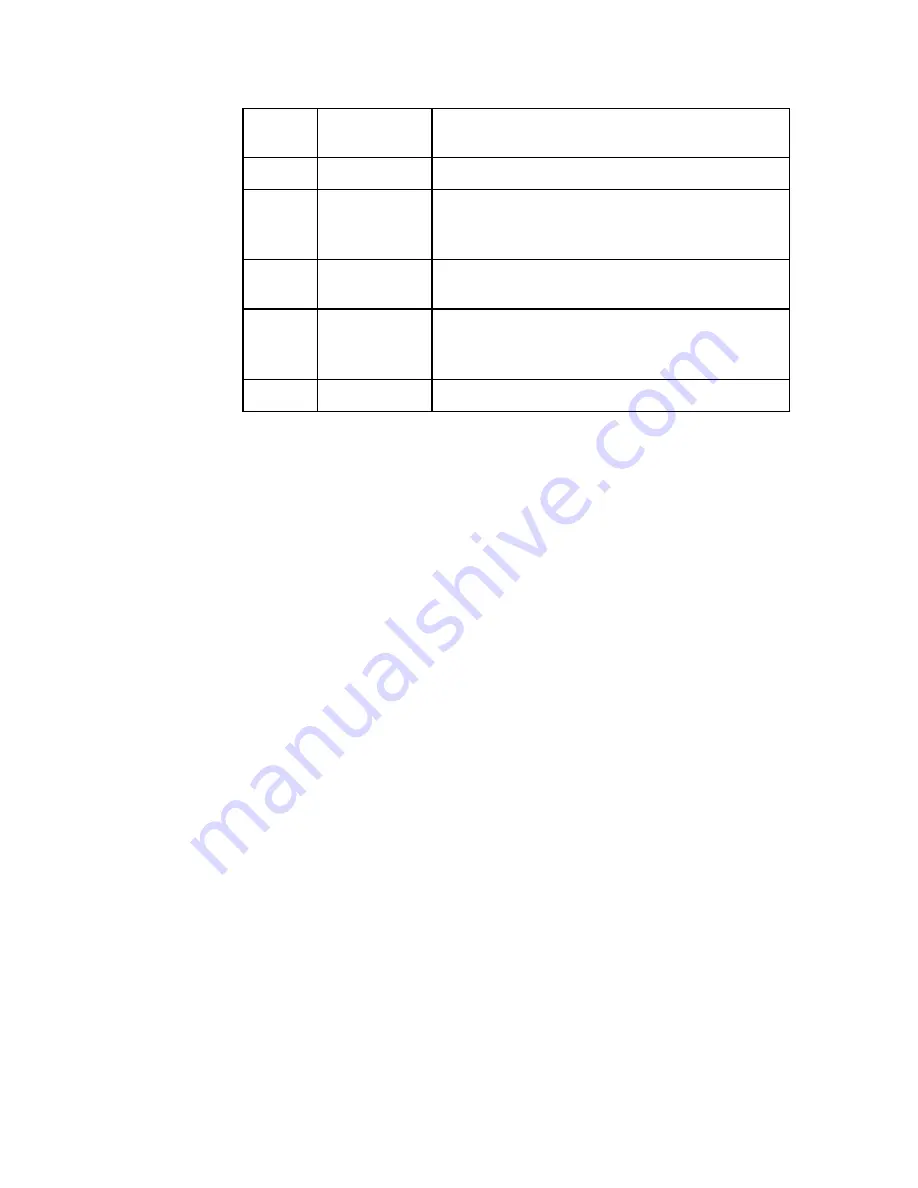
ORET RONIC
™
Tramp Metal Detector
R E C 4 1 0 5
3 - 1 5
due to faulty wiring or actual fault
condition.
F 2
S E L F T E ST
Indicates a microprocessor problem.
F 3
BALANCE
The coil imbalance exceeds the ability
of the detector to electronically “self-
balance.” See 4.4.1
F 4
HIGHPILE
The high pile input was not reset within
4 seconds after tripping.
F 5
OVERLOAD
The input circuitry is saturated. Reduce
gain, mechanically balance coils per 4.4.1
or remove the cause of the overload.
F 6
AUDITCHK
Not yet implemented.
3.3
Setting up the TMD
T h i s s e c t i o n g u i d e s y o u t h r o u g h t h e i n i t i al s e t u p an d ca l i b r a t i o n o f y o u r
O R E T R O NI C I I I T M D . On c e t h e T M D i s s e t u p c o r r e c t l y , f e w o r n o ch an g e s
t o t h e s e t t i n g s a r e r e q u i r ed .
3.3.1 Before You Begin
B e f o r e y o u b eg in s et tin g u p a n d c a l i b r a t in g th e TM D fo r y o u r ap p l i c at io n , b e
s u r e t h at :
•
T h e
T M D
h a s b e en i n st a l l ed b o th me c h a n i c al l y an d e l ec t r i c a l l y
i n a c c o r d an c e w i t h t h e p r o c ed u r e s i n
C h a p t e r 2 : I n s t a l l i n g t h e
T M D
a n d t h e i n s t a l l a t i o n a n d f i e l d w i r i n g d r a w i n g s .
•
Y o u a r e f ami l i a r w i th th e fu n c t io n s o f al l th e k ey s, in d i c a to r s,
a n d d i s p l a y s o n t h e
T M D
f r o n t p a n e l .
•
Y o u h av e t a k e n t h e r eq u i r ed me a s u r e me n t s ( r e f e r t o
S ec t i o n
2 .1 1
:
Det ermi n ing V a l u es to Use fo r In it ia l S e tu p
) .
•
Y o u h av e a t i m i n g m a r k o n y o u r c o n v e y o r b e l t .
•
Y o u h av e a p i e c e o f t r a mp me t a l t h e a v e r ag e s i z e t o b e
d e t e c t ed .
•
Y o u p o we r u p t h e s y ste m 1 5 mi n u t e s b e f o r e b eg in n i n g se t u p .
Summary of Contents for Ramsey ORETRONIC III
Page 2: ...ORETRONIC Tramp Metal Detector ...
Page 10: ...ORETRONIC Tramp Metal Detector REC 4105 vi THIS PAGE LEFT BLANK INTENTIONALLY ...
Page 12: ...ORETRONIC Tramp Metal Detector REC 4105 viii THIS PAGE LEFT BLANK INTENTIONALLY ...
Page 18: ...REC 4105 xiv THIS PAGE LEFT BLANK INTENTIONALLY ...
Page 32: ...ORETRONIC Tramp Metal Detector REC 4105 1 14 THIS PAGE LEFT BLANK INTENTIONALLY ...
Page 48: ......
Page 96: ...ORETRONIC Tramp Metal Detector REC 4105 4 28 THIS PAGE LEFT INTENTIONALLY BLANK ...
Page 110: ...ORETRONIC Tramp Metal Detector REC 4105 A 10 THIS PAGE LEFT BLANK INTENTIONALLY ...
Page 120: ...Oretronic III Tramp Metal Detector REC 4105 B 10 THIS PAGE LEFT BLANK INTENTIONALLY ...
Page 124: ...Oretronic III Tramp Metal Detector REC 4105 C 4 THIS PAGE LEFT INTENTIONALLY BLANK ...
Page 129: ......
Page 130: ......
Page 131: ......
Page 132: ......
Page 133: ......
Page 134: ......
Page 135: ......
Page 136: ......
Page 137: ......
Page 138: ......
Page 139: ......
Page 140: ......
Page 141: ......
Page 142: ......
Page 143: ......