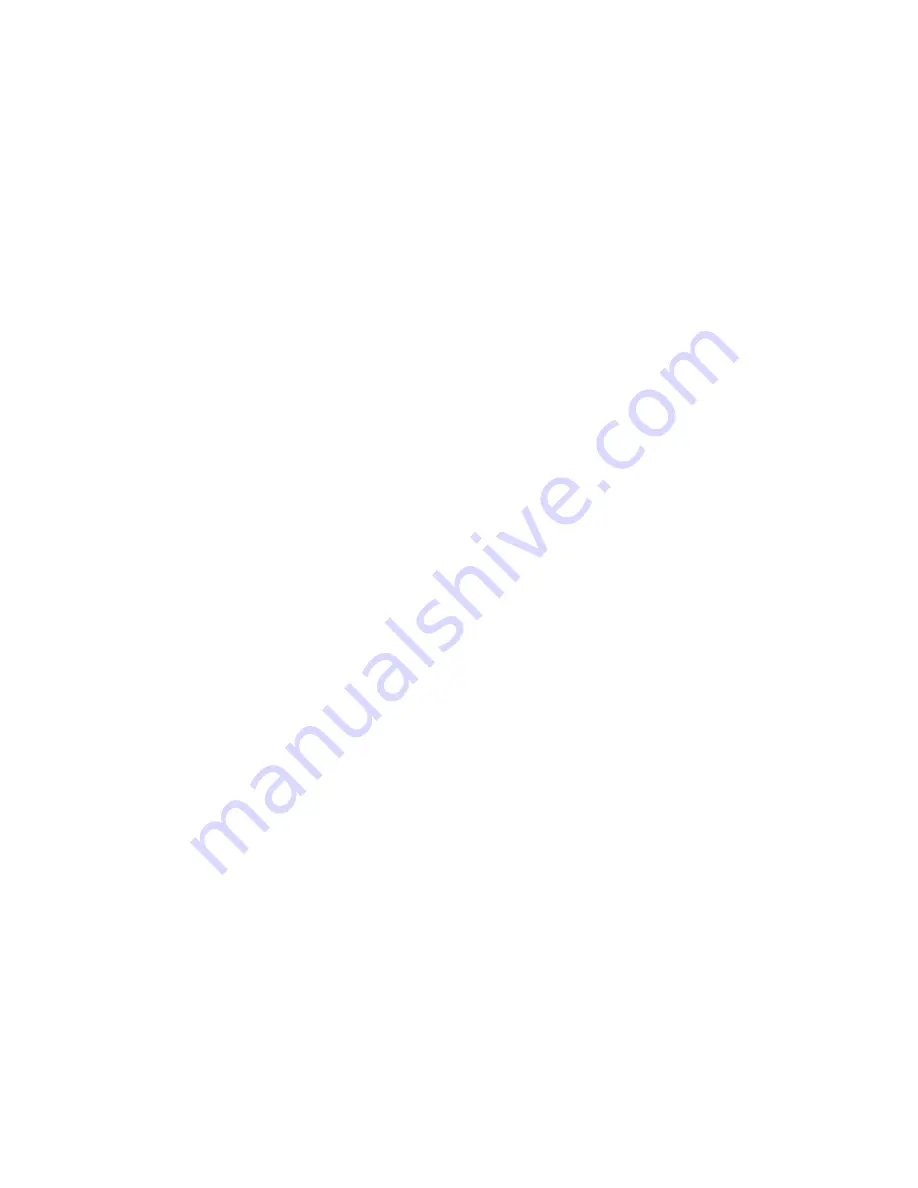
Installation & Wiring
Wiring
Thermo Electron Corporation
Polysonics SX40 User Guide
2-15
2.
Remove the meter access cover.
3.
Locate the POSZERO and RLYCOM wire connections within the
same block used for connecting DC power.
4.
Turn the screws on top of the transducer block counterclockwise to
fully open the connections.
5.
Make the following connections:
a.
First switch wire to RLYCOM
b.
Second switch wire to POSZERO
6.
Turn the screws clockwise to close the connections.
7.
Ensure the wire connections are secure, and replace the meter access
cover.
Summary of Contents for Polysonics SX40
Page 2: ...Polysonics SX40 Dedicated Doppler Flowmeter User Guide P N 1 0563 006 Revision G ...
Page 3: ......
Page 5: ...This page intentionally left blank ...
Page 37: ...This page intentionally left blank ...
Page 53: ...This page intentionally left blank ...
Page 54: ......