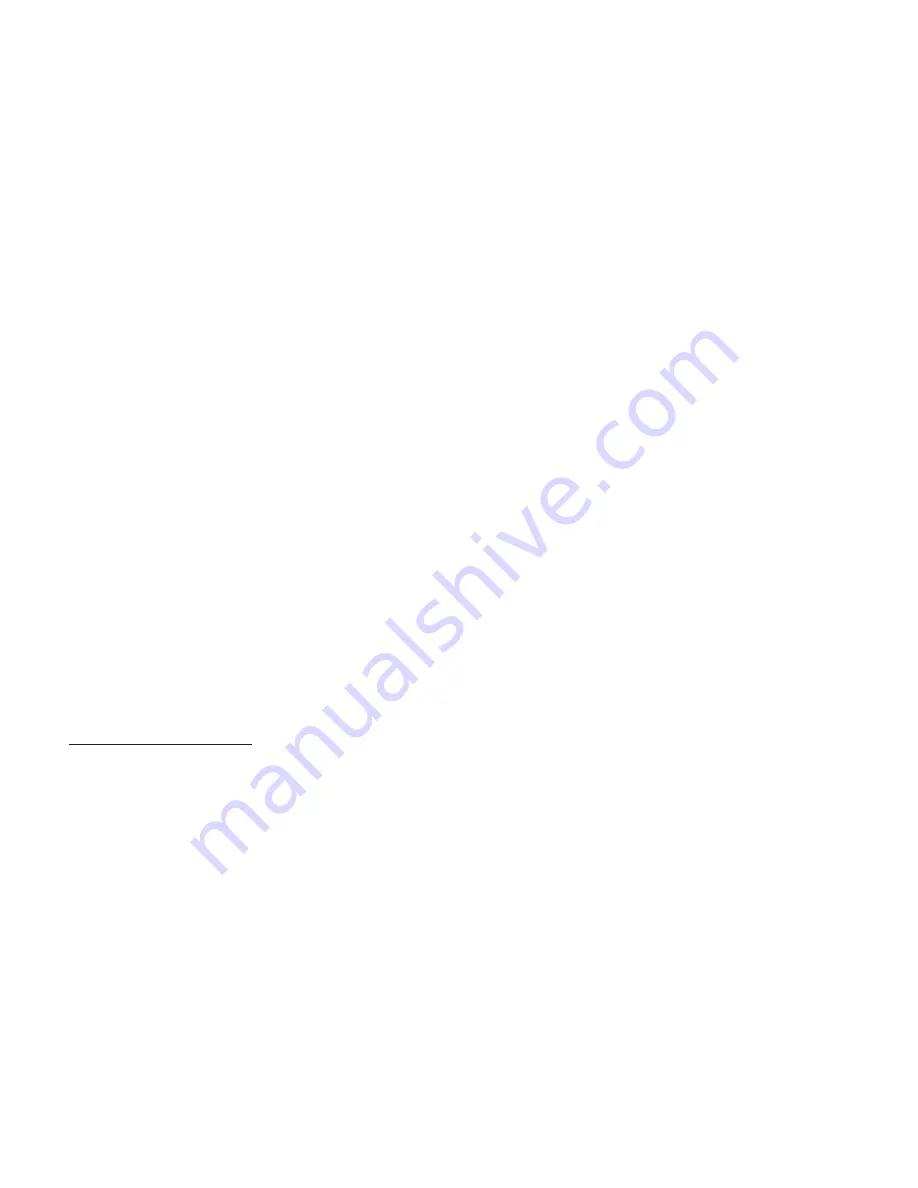
6
The 1-1/4” supply line or riser tapping in the top of the boiler extends approximately 1” below the top
or waterline of the boiler, thus allowing only air-free water to enter the supply to the heating system. The
air trapped in the top of the boiler must be purged through the 3/4" vent tapping by using an Automatic
Float Vent, a Manual Vent or piped into a conventional expansion tank. (See Figure 2 and 4)
The recommended locations of circulators, expansion tanks, etc. are illustrated in Figure 4. Relief valve
discharge and drain valve piping should be piped to a safe place of discharge.
All
plugs and water con-
nections should be checked for leaks upon installation and annually.
VII. TANKLESS WATER HEATER PIPING
The tankless heater may be connected as shown in Figure 4.
A mixing valve (not supplied) may be used to reduce the water temperature at kitchen or bathroom
taps. High temperature water for a dishwasher may be obtained by piping as shown.
The nuts that secure the tankless coil flange should be tightened before the boiler is filled with water, after
initial firing and every year during annual maintenance.
DETERIORATION DUE TO COIL GASKET LEAKS
SHALL VOID WAR RAN TY.
VIII. BURNER AND CONTROLS
The gas burner is factory mounted and wired on all units. The ignition safety shut-off device must be
tested when the unit is in operation. To do this turn gas supply off. Set the thermostat or controller above
room temperature to call for heat. Watch for the igniter to heat up. Determine the length of time the gas valve
stays open. Use a volt meter to verify voltage present at the gas valve. The length of time that power is
applied to the gas valve should not exceed 4.0 seconds. To relight, see lighting and shut-down instructions.
A.
Primary Control - Honeywell S89F
The CWL-GS Series Boiler is equipped with a Honeywell S89F Controller. The Controller is a 24 vac
micro processor based control with electronic ignition and a combustion blower relay. The controller uses
full time flame sensing to continually monitor flame quality with a minimum current of 0.7 microamps. In
addition the controller is set for a 34 second pre purge. In the event of a flame failure, the control shall try
for ignition 3 times before going into lockout. Recovery from lockout requires a manual reset by adjusting
the thermostat. Alternatively, the 24 vac power supply may be disconnected for a period of 5 seconds in
order to reset the control.
CONTROL OPERATION
When a call for heat is received from the thermostat supplying 24 volts to TH/W, the control will check
the pressure switch for normally open contacts. The combustion blower is then energized and once the
pressure switch contacts close, an optional prepurge delay begins and the electronic ignitor is activated.
Following the ignitor heat-up period the gas valve is energized for the trial for ignition period.
When flame is detected during the trial for ignition, the ignitor is de-energized immediately and the gas
valve and combustion blower remains energized. The thermostat, pressure switch, and main burner flame
are constantly monitored to assure the system continues to operate properly. When the thermostat is satis-
fied and the demand for heat ends, the main valve is de-energized immediately, the control senses the loss
of flame signal and initiates an optional post-purge period before de-energizing the combustion blower.
B.
Aquastat Relay L7224 (For CWL Models Only)
This control is installed on the middle of the domestic coil. These immersion type controls are used with
forced hydronic heating systems which include domestic water service. This model provides high limits,
low limits for maintaining minimum boiler water temperature and circulator controls. This control can also
be used for multizone control by using a separate circulator and an R845 relay for each zone. (See Figure
6) The primary control is factory wired to the aquastat relay. These controls working as a system will pre-