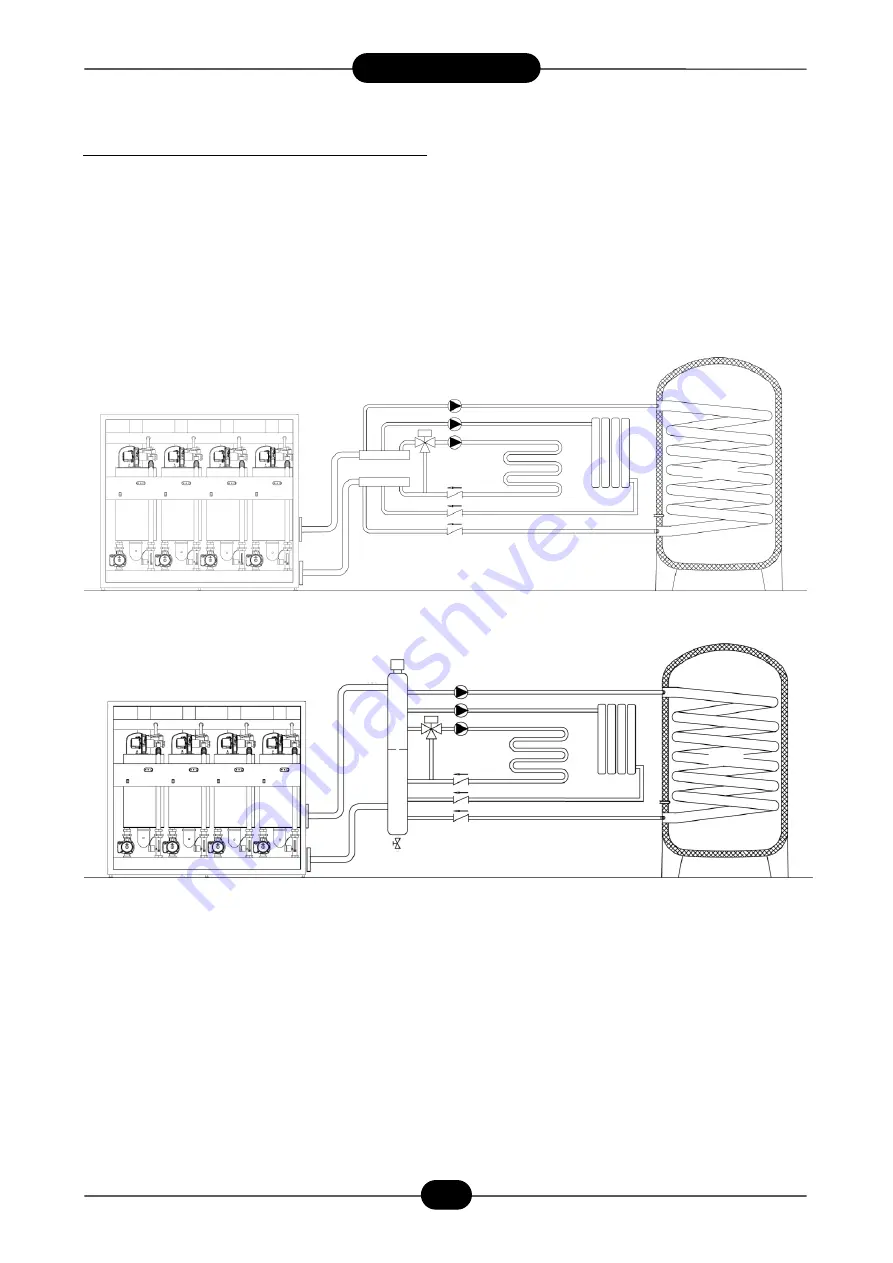
16
Installation schemes
5
Installation schemes
A plant scheme must be fit for the technical
boiler features: so it’s possible to utilize in the
better way boiler’s efficiency and to keep the
plant in good conditions for a long time
In Figure 8 is shown an installation without a
mixing element, in Figure 9 is shown a installa-
tion with a mixing element.
Figure 8
Figure 9
Summary of Contents for COROLLA PACK 1000 Series
Page 1: ...COROLLA PACK SERIE1000 ...
Page 2: ......
Page 35: ...35 Electrical wiring diagram ...
Page 38: ...NOTES ...
Page 39: ......
Page 40: ...20135201 Rev 0 05 17 ...