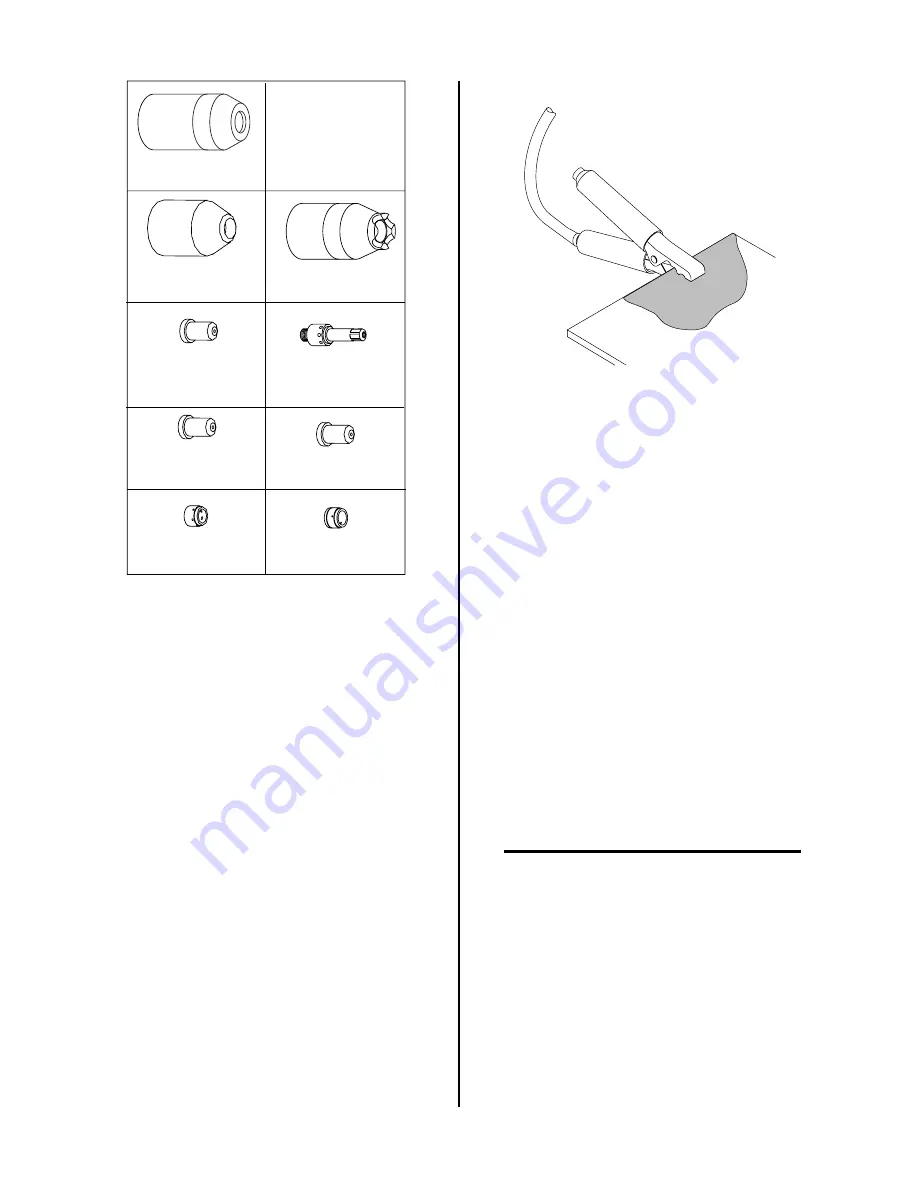
Manual 0-2746
23
SECTION 4: OPERATION
Standard Shield Cup
Catalog No. 8-7500
Standoff Cutting Tip
Air/N2, 60 Amp
Catalog No. 9-7726
Gouging Gas Distributor
Catalog No. 8-7508
A-02473
Crown Shield Cup
Catalog No. 8-7507
Drag Cutting Tip
Air/N2, 35 Amp
Catalog No. 8-7503
Gouging Tip, Air
Catalog No. 8-7506
Gas Distributor
Catalog No. 8-7501
Electrode
Catalog No. 8-7502
Copper Shield Cup
Catalog No. 8-7496
Figure 4-7 Parts Selection (PCH-60)
B. Check primary power source as follows:
1. Check the power source for proper input voltage. Make
sure the input power source meets the power require-
ments for the unit per Section 2.03-A-4, Specifications/
Design Features.
2. Connect the input power cable (or close the main dis-
connect switch) to supply power to the system.
C. Gas Selection
Select desired gas (air or nitrogen). Make sure gas source
meets pressure and flow requirements (refer to Section
3.08, Gas Connections). Check connection and turn gas
supply on.
D. Work Cable Connection
Check for a solid and clean work cable connection to the
workpiece. The area must be free from paint and rust.
Make a solid work cable
connection to the work-
piece or cutting table
A-00925
Figure 4-8 Work Cable Connection To Workpiece
E. Torch Connection
Check that the torch is properly connected.
F. Power Supply On
Move the ON/OFF switch to ON position.
G. Select Output Current
Select the desired current output level for the operation:
• 15 to 60 amps for standoff cutting and gouging
• 15 to 35 amps for drag cutting
H. Set Operating Pressure
Move the RUN/SET/LATCH switch to SET position. Ad-
just the gas pressure to 60 psi (4.1 bar).
I. RUN/SET Switch
Set the RUN/SET/LATCH switch to RUN position.
The system is now ready for operation.
NOTE
For general cutting, use the RUN position which
provides normal touch operation where the torch
switch must be held throughout the main arc trans-
fer.
For specific applications, use the LATCH position
where the torch switch can be released after the main
arc transfer. The torch remains activated until the
main arc breaks from the workpiece.
Summary of Contents for CE PAK Master 75XL
Page 1: ...Manual No 0 2746 August 23 1999 Operating Manual A 02464 Air Plasma Cutting Power Supply...
Page 3: ...Purchase Date Power Supply Torch Record Serial Numbers For Warranty Purposes...
Page 4: ......
Page 41: ...Manual 0 2746 35 APPENDIX This Page Left Blank...
Page 43: ...Manual 0 2746 37 APPENDIX A 02503 OK OK TO MOVE 8 11 99...
Page 44: ...APPENDIX 38 Manual 0 2746...