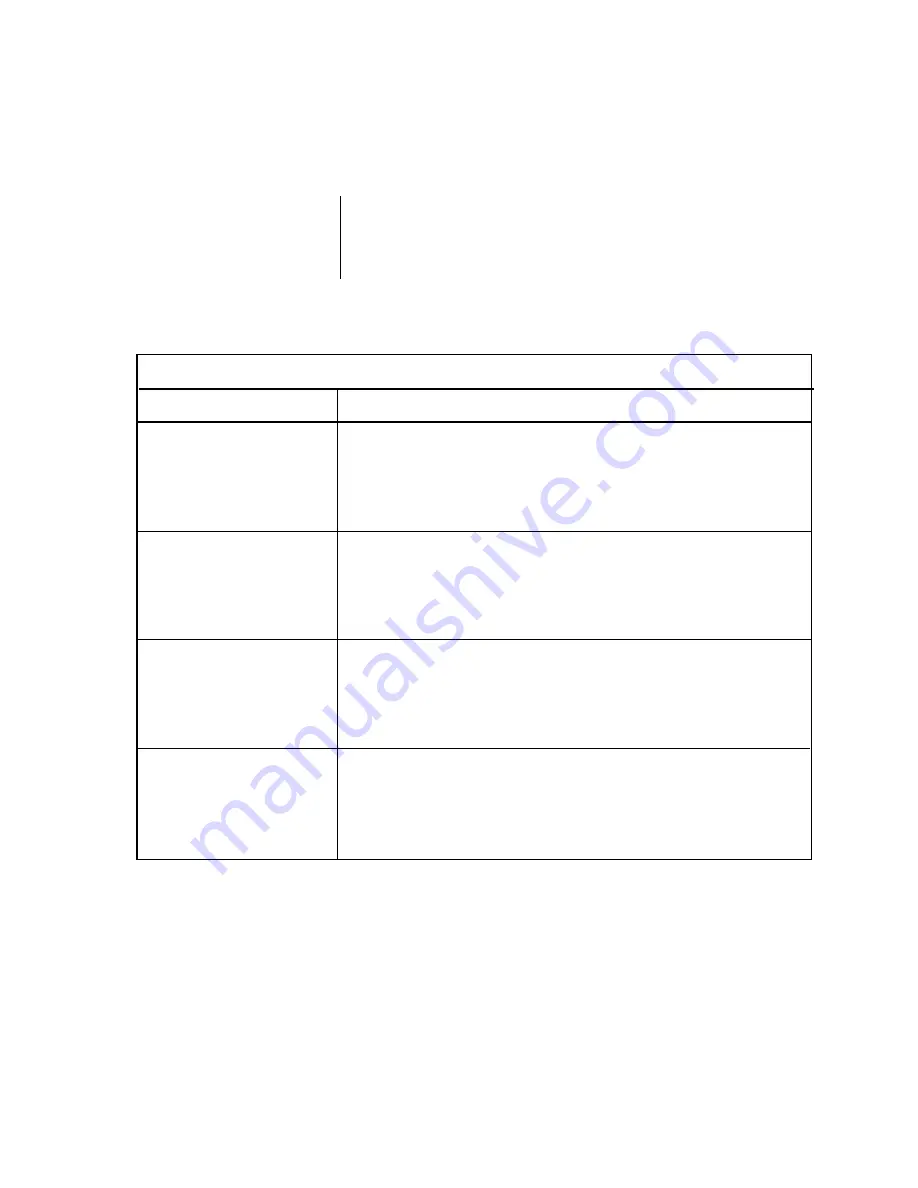
Manual 0-2470
35
OPERATION
4.06 OPERATING THE SYSTEM (continued)
Dross
(continued)
High speed dross usually forms a narrow bead along the bottom
of the cut edge and is very difficult to remove. When cutting a
troublesome steel, it is sometimes useful to reduce the cutting
speed to produce slow speed dross. Any resultant cleanup can be
accomplished by scraping, not grinding.
Table 4-C Common Causes of Operating Problems
Problem
Insufficient
Penetration
Main Arc
Extinguishes
Excessive
Dross Formation
Short Torch
Parts Life
Possible Cause
1. Cutting speed too fast
2. Torch tilted too much
3. Metal too thick
4. Worn torch parts
5. Cutting current too low
1. Cutting speed too slow
2. Torch standoff too high from workpiece
3. AC line too low - reduce output current
4. Work cable disconnected
5. Worn torch parts
1. Cutting speed too slow (bottom dross) Easily removed
2. Cutting speed too fast (bottom dross) Tight bead, Difficult to remove
3. Torch standoff too high from workpiece (top dross) Easily removed
4. Worn torch parts
5. Improper cutting current
1. Oil or moisture in air source
2. Exceeding system capability (material too thick)
3. Excessive pilot arc time
4. Air flow too low (incorrect pressure)
5. Improperly assembled torch
Common Cutting Faults
Summary of Contents for CE CutMaster 50
Page 12: ...GENERAL INFORMATION 8 ...
Page 79: ...Manual 0 2470 75 PARTS LIST 1 2 3 5 6 8 15 13 14 7 10 11 12 9 16 A 00775 ...
Page 85: ...Manual 0 2470 81 PARTS LIST 6 7 5 4 3 1 2 8 9 11 10 12 13 ...
Page 87: ...Manual 0 2470 83 APPENDIX This Page Left Blank ...
Page 88: ...APPENDIX 84 Manual 0 2470 APPENDIX I SYSTEM SCHEMATIC A 00804 ...
Page 89: ...Manual 0 2470 85 APPENDIX A 00804 ...
Page 90: ...APPENDIX 86 Manual 0 2470 ...