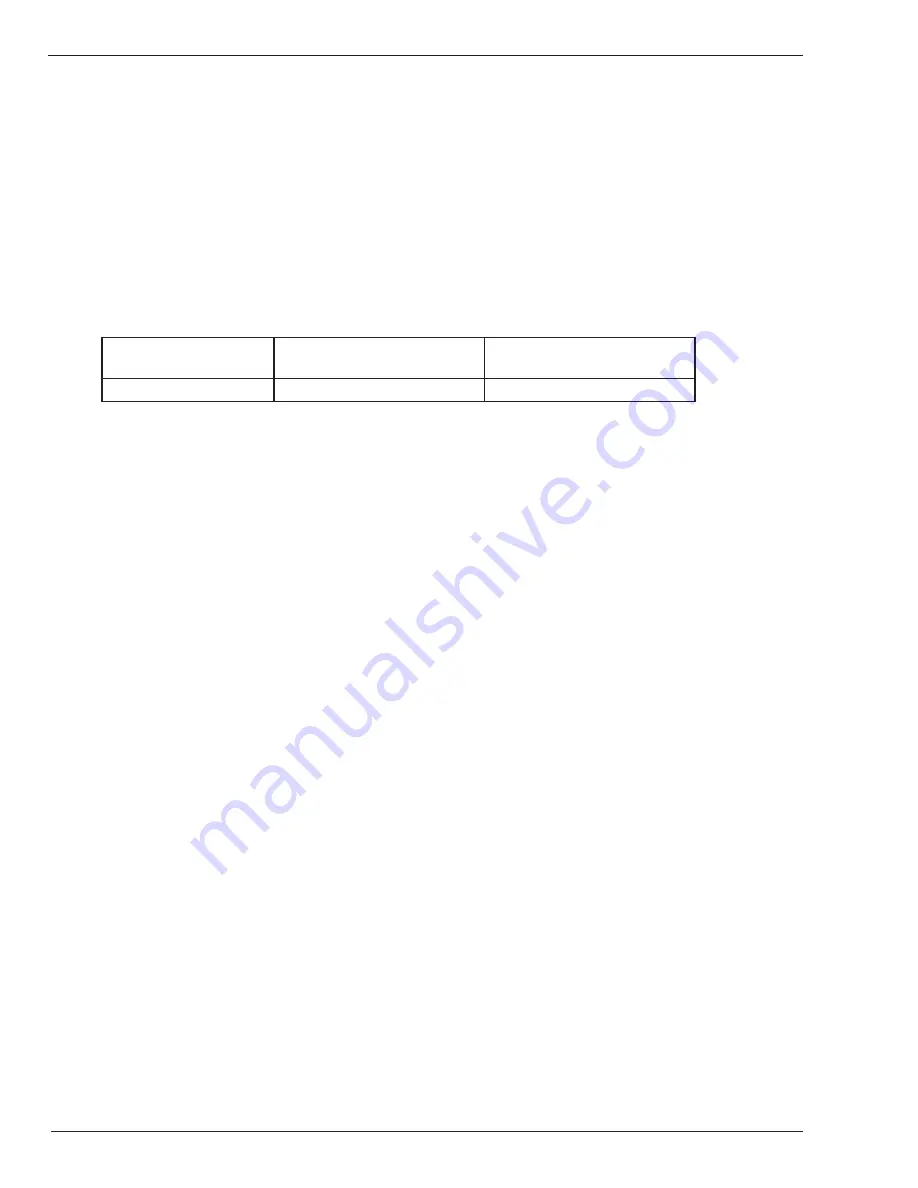
CUTMASTER 42
GENERAL INFORMATION 1-8 Manual 0-5141
1.08 Statement of Warranty
LIMITED WARRANTY:
Subject to the terms and conditions established below, Thermadyne Company warrants to the original retail purchaser that new
Thermal Dynamics CUTMASTER® plasma cutting systems sold after the effective date of this warranty are free of defects in material and workmanship.
Should any failure to conform to this warranty appear within the applicable period stated below, Thermadyne Company shall, upon notification thereof and
substantiation that the product has been stored operated and maintained in accordance with Thermadyne’s specifications, instructions, recommendations
and recognized industry practice, correct such defects by suitable repair or replacement.
This warranty is exclusive and in lieu of any warranty of merchantability or fitness for a particular purpose.
Thermadyne will repair or replace, at its discretion, any warranted parts or components that fail due to defects in material or workmanship within the
time periods set out below. Thermadyne Company must be notified within 30 days of any failure, at which time Thermadyne Company will provide
instructions on the warranty procedures to be implemented.
Thermadyne Company will honor warranty claims submitted within the warranty periods listed below. All warranty periods begin on the date of sale
of the product to the original retail customer or 1 year after sale to an authorized Thermadyne Distributor.
LIMITED WARRANTY PERIOD
Product
Power Supply Components
(Parts and Labor)
Torch and Leads
(Parts and Labor)
CUTMASTER 42
4 Year
1 Year
This warranty does not apply to:
1. Consumable Parts, such as tips, electrodes, shield cups, o - rings, starter cartridges, gas distributors, fuses, filters.
2. Equipment that has been modified by an unauthorized party, improperly installed, improperly operated or misused based upon industry standards.
In the event of a claim under this warranty, the remedies shall be, at the discretion of Thermadyne Company:
1. Repair of the defective product.
2. Replacement of the defective product.
3. Reimbursement of reasonable costs of repair when authorized in advance by Thermadyne.
4. Payment of credit up to the purchase price less reasonable depreciation based on actual use.
These remedies may be authorized by Thermadyne and are FOB West Lebanon, NH or an authorized Thermadyne service station. Product returned
for service is at the owner’s expense and no reimbursement of travel or transportation is authorized.
LIMITATION OF LIABILITY:
Thermadyne Company shall not under any circumstances be liable for special or consequential damages such as, but not
limited to, damage or loss of purchased or replacement goods or claims of customer of distributors (hereinafter “Purchaser”) for service interruption.
The remedies of the Purchaser set forth herein are exclusive and the liability of Thermadyne with respect to any contract, or anything done in
connection therewith such as the performance or breach thereof, or from the manufacture, sale, delivery, resale, or use of the goods covered by or
furnished by Thermadyne whether arising out of contract, negligence, strict tort, or under any warranty, or otherwise, shall not, except as expressly
provided herein, exceed the price of the goods upon which liability is based.
This warranty becomes invalid if replacement parts or accessories are used which may impair the safety or performance of any Thermadyne
product.
This warranty is invalid if the Thermal Dynamics product is sold by non - authorized persons.
Effective October 15, 2010
Summary of Contents for 42 CUTMASTER
Page 4: ...TABLE OF CONTENTS...
Page 24: ...This page left blank intentionally...
Page 38: ...This page left blank intentionally...
Page 44: ...Notes...
Page 45: ...This Page Intentionally Blank...