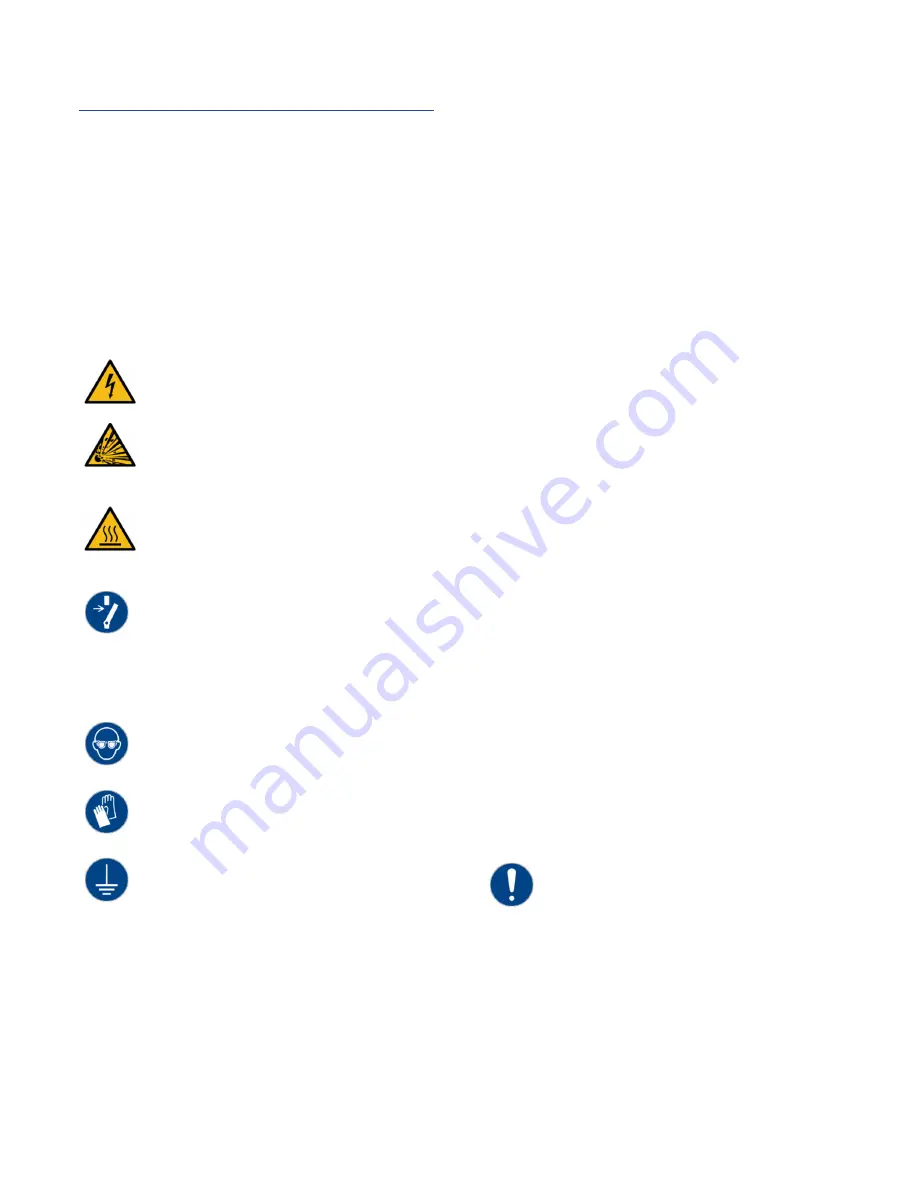
23
Start-Up
Every chiller is factory set to deliver chilled water in
accordance with the standard operating
specifications for that particular chiller. Due to
variables involved with different applications and
different installations, minor adjustments may be
required during the initial start-up to ensure proper
operation. Use a qualified refrigeration technician to
perform the start-up procedure in sequence. The
following serves as a checklist for the initial start-up
and for subsequent start-ups if the chiller is out of
service for a prolonged time.
WARNING: This equipment contains hazardous
voltages that can cause severe injury or death.
WARNING: This equipment contains refrigerant under
pressure. Accidental release of refrigerant under
pressure can cause personal injury and or property
damage.
WARNING: The exposed surfaces of motors, refrigerant
piping, and other fluid circuit components can be very
hot and can cause burns if touched with unprotected
hands.
CAUTION: Disconnect and lock out incoming power
before installing, servicing, or maintaining the
equipment. Connecting power to the main terminal
block energizes the entire electric circuitry of the unit.
Electric power at the main disconnect should be shut
off before opening access panels for repair or
maintenance.
CAUTION: Wear eye protection when installing,
maintaining, or repairing the equipment to protect
against any sparks, debris, or fluid leaks.
CAUTION: Wear protective gloves when installing,
maintaining, or repairing the equipment to protect
against any sparks, debris, or fluid leaks.
CAUTION: Wire the unit ground in compliance with
local and national codes.
Step 1 – Connect Main Power
Connect main power properly ensuring it matches
the voltage shown on the nameplate of the unit.
Check the electrical phase sequence prior to start-
up. Operation of the compressor with incorrect
electrical phase sequencing will cause damage to the
compressors. Check the phasing prior to applying
power. The proper sequence is “ABC.” If the phasing
is incorrect, open the main power disconnect and
switch two line leads on the main power terminal
blocks (or the unit mounted disconnect). All
electrical components are in-phase at the factory. Do
not interchange any load leads that are from the unit
contactors or the motor terminals. After making
proper power connection and grounding, turn the
main power on.
Step 2 – Fill Coolant Circuit
Check to make sure all process chilled-water piping
connections are secure. This chiller is designed for
40% Industrial Grade Ethylene Glycol with a
corrosion inhibitor.
Chillers at their simplest have two main heat
exchangers: one that absorbs the heat from the
process (evaporator) and one that removes the heat
from the chiller (condenser). Our water-cooled
chillers use a shell-and-tube condenser that has
copper refrigerant tubes and a steel shell. These, as
are all heat exchangers, are susceptible to fouling of
heat transfer surfaces due to scale or debris. Fouling
of these surfaces reduces the heat-transfer surface
area while increasing the fluid velocities and
pressure drop through the heat exchanger. All of
these effects reduce the heat transfer and affect the
efficiency of the chiller.
The complex nature of fluid chemistry requires a
specialist to evaluate and implement appropriate
sensing, measurement and treatment needed for
satisfactory performance and life. The
recommendations of the specialist may include
filtration, monitoring, treatment and control devices.
With the ever-changing regulations on fluid usage
and treatment chemicals, the information is usually
up-to-date when a specialist in the industry is
involved.
CAUTION: When your application requires the use of
glycol, use industrial grade glycol specifically designed
for heat transfer systems and equipment. Never use
glycol designed for automotive applications.
Automotive glycols typically have additives engineered
to benefit the materials and conditions found in an
automotive engine; however, these additives can gel
and foul heat exchange surfaces and result in loss of
performance or even failure of the chiller. In addition,
these additives can react with the materials of the
pump shaft seals resulting in leaks or premature pump
failures.