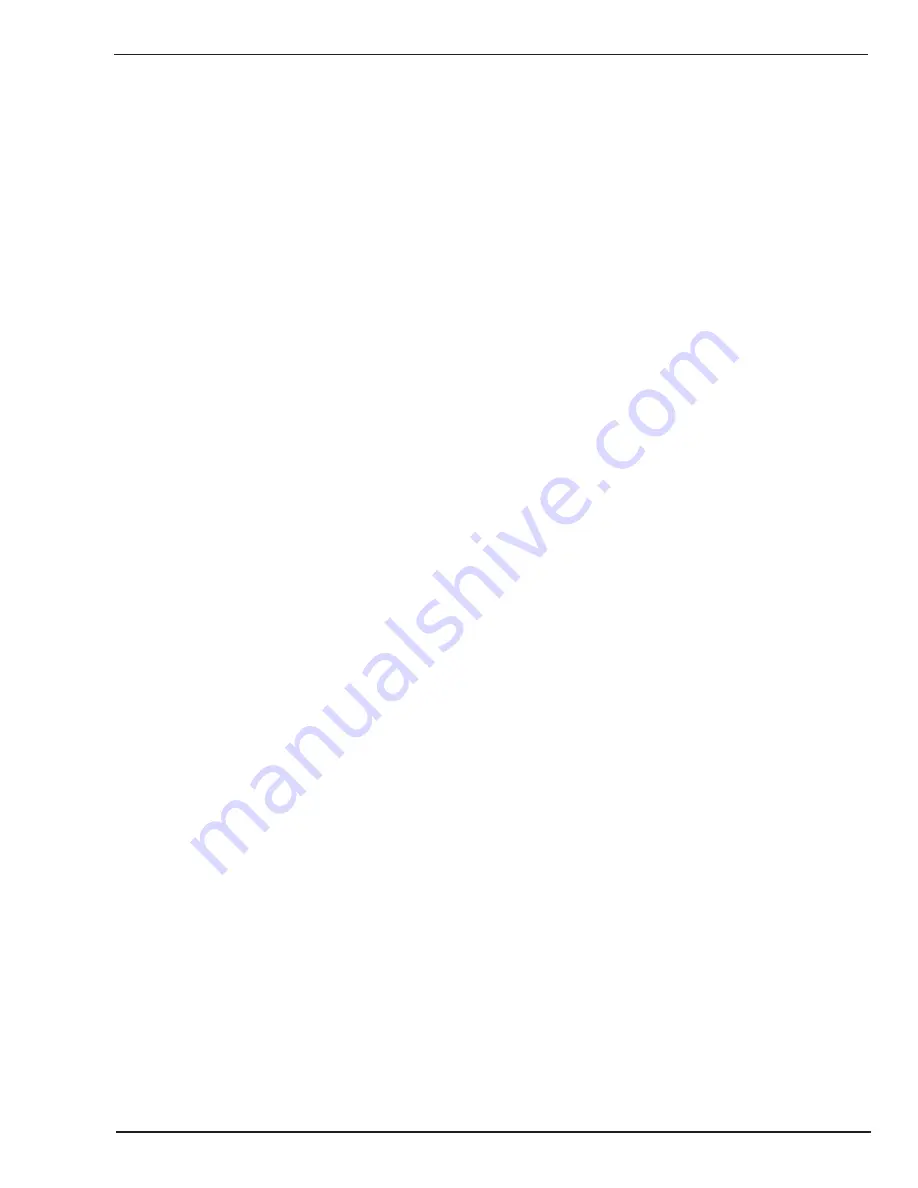
pro-wave 300gtsw
June 21, 2012
5-3
D. Wandering Arc, Poor Control of Arc Direction
1. Wrong size tungsten electrode, typically larger than
recommended
a. Use proper size electrode for amperage
selected (see Operating Manual 0-2514).
2. Improperly prepared tungsten electrode
a. Prepare tungsten properly.
3. Gas Flow rate too high
a. Reduce flow rate to approximately 12 SCFH.
4. Drafts blowing shielding gas away from tungsten
electrode
a. Shield weld zone from drafts and check
condition of tungsten electrode.
5. Loose gas fitting on regulator or gas line drawing
air into weld zone, causing green/blue discoloration
of workpiece
a. Check and tighten all gas fittings.
6. Water in torch
a. Refer to torch parts list for part(s) requiring
replacement and repair torch as necessary.
E. No High Frequency at Torch When PROCESS
SELECTOR Switch is in HF TIG Position
1. PROCESS SELECTOR switch is not in the HF TIG
position
a. Place switch in HF TIG position.
2. Drafts blowing shielding gas away from tungsten
electrode
a. Shield weld zone from drafts and check
condition of tungsten electrode.
3. Loose gas fitting on regulator or gas line drawing
air into weld zone
a. Check and tighten all gas fittings.
4. Water in torch
a. Refer to torch parts list for part(s) requiring
replacement and repair torch as necessary.
5. Tungsten condition is poor
a. Replace electrode.
6. Electrode too high off metal
a. Reduce stand-off.
7. Faulty Main Circuit Board (PCB1)
a. Refer to the Main Circuit Board section 6.11,
page 6-10.
8. Faulty Current Transformer CT1
a. With no welding arc established, measure for
0VDC between CN1 pins 3 and 4 on PCB1.
Replace CT1 if voltage is greater than 0.1VDC.
9. Faulty High Frequency Unit
a. Refer to section 6.39, page 6-46.
10. Faulty TIG Torch
a. Replace TIG torch.
11. Work lead not connected
a. Verify all connections to torch and workpiece.
F. Lack of High Frequency; Difficulty in Establishing
an Arc
1. Dissipation of high frequency from torch cable or
conductive gas hose
a. Be sure that the torch cable is not near any
grounded metal. Do not use conductive gas
hose.
2. Weld cable leakage
a. Check cables and torch for cracked or
deteriorated insulation or bad connections.
Repair or replace necessary parts.
3. Poor ground connection to power supply
a. Verify ground by trying to strike arc within one
inch (2.54cm) of ground clamp.
G. Wall Fuse/Circuit Breaker Trips When Turned ON
1. Input voltage over rated limit
a. Connect to proper line voltage.
2. Shorted primary inverter components
a. Perform the PCA Input Diode Bridge Test,
section 6.24, page 6-24.
3. Faulty PCB1
a. Replace PCB1. Refer to page 6-13.
Summary of Contents for 300GTSW Pro-Wave
Page 26: ...pro wave 300gtsw 2 8 June 21 2012 This page left blank intentially ...
Page 32: ...pro wave 300gtsw 4 4 June 21 2012 This page left blank intentially ...
Page 38: ...pro wave 300gtsw 5 6 June 21 2012 This page left blank intentially ...
Page 67: ...pro wave 300gtsw June 21 2012 6 29 THIS PAGE INTENTIONALLY LEFT BLANK ...
Page 100: ...pro wave 300gtsw 7 8 June 21 2012 6 16 17 Art A 06151 Figure 7 3 Rear Panel ...
Page 105: ...pro wave 300gtsw June 21 2012 7 13 77 26 36 1 36 Art A 06159 Figure 7 11 Output diode bus bar ...
Page 106: ...pro wave 300gtsw 7 14 June 21 2012 76 Art A 06160 Figure 7 12 Main Transformer ...
Page 110: ...pro wave 300gtsw 7 18 June 21 2012 This page left blank intentially ...
Page 121: ...pro wave 300gtsw June 21 2012 A 11 THIS PAGE INTENTIONALLY LEFT BLANK ...
Page 129: ...This page left blank intentially ...