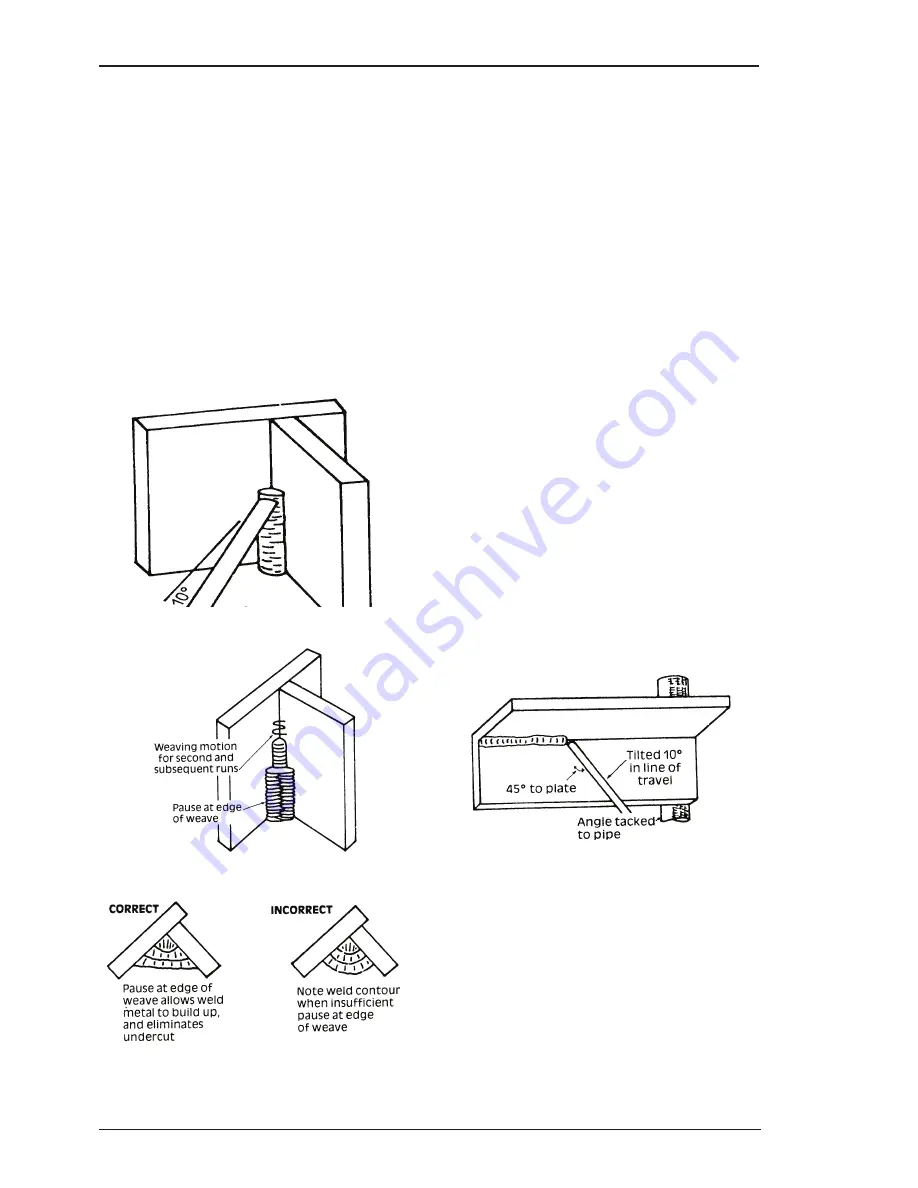
ARC MASTER 175 SE OpERATION
Manual # 0-5054 4-8 March 20, 2008
of the fillet. The electrode needs to be about 10°
from the horizontal to enable a good bead to
be deposited. Refer Figure 4-16. Use a short
arc, and do not attempt to weave on the first
run. When the first run has been completed
de-slag the weld deposit and begin the second
run at the bottom. This time a slight weaving
motion is necessary to cover the first run
and obtain good fusion at the edges. At the
completion of each side motion, pause for a
moment to allow weld metal to build up at
the edges, otherwise undercut will form and
too much metal will accumulate in the centre
of the weld. Figure 4-17 illustrates multi-run
technique and Figure 4-18 shows the effects of
pausing at the edge of weave and of weaving
too rapidly.
Art # A-07701
Figure 4-16: Single run vertical fillet weld
Art # A-07702
Figure 4-17: Multi run vertical fillet weld
Art # A-07703
Figure 4-18: Examples of vertical fillet welds
2. Vertical Down
The E7014 electrode makes welding in this
position particularly easy. Use a 1/8" (3.2mm)
electrode at 120 amps. The tip of the electrode
is held in light contact with the work and the
speed of downward travel is regulated so that
the tip of the electrode just keeps ahead of the
slag. The electrode should point upwards at
an angle of about 45°.
3. Overhead Welds
Apart from the rather awkward position
necessary, overhead welding is not much
more difficult that down hand welding. Set
up a specimen for overhead welding by first
tacking a length of angle iron at right angles to
another piece of angle iron or a length of waste
pipe. Then tack this to the work bench or hold
in a vice so that the specimen is positioned in
the overhead position as shown in the sketch.
The electrode is held at 45° to the horizontal
and tilted 10° in the line of travel (Figure 4-
19). The tip of the electrode may be touched
lightly on the metal, which helps to give a
steady run. A weave technique is not advisable
for overhead fillet welds. Use a 1/8" (3.2mm)
E6012 electrode at 120 amps, and deposit the
first run by simply drawing the electrode along
at a steady rate. You will notice that the weld
deposit is rather convex, due to the effect of
gravity before the metal freezes.
Art # A-07704
Figure 4-19: Overhead fillet weld
4.19 Distortion
Distortion in some degree is present in all forms of
welding. In many cases it is so small that it is barely
perceptible, but in other cases allowance has to be
made before welding commences for the distortion
that will subsequently occur. The study of distortion is
so complex that only a brief outline can be attempted
hear.
Summary of Contents for 175 SE ARC MASTER
Page 6: ......
Page 18: ...Manual 0 5054 1 12 March 20 2008 ARC MASTER 175 SE SAFETY INSTRUCTIONS...
Page 41: ......