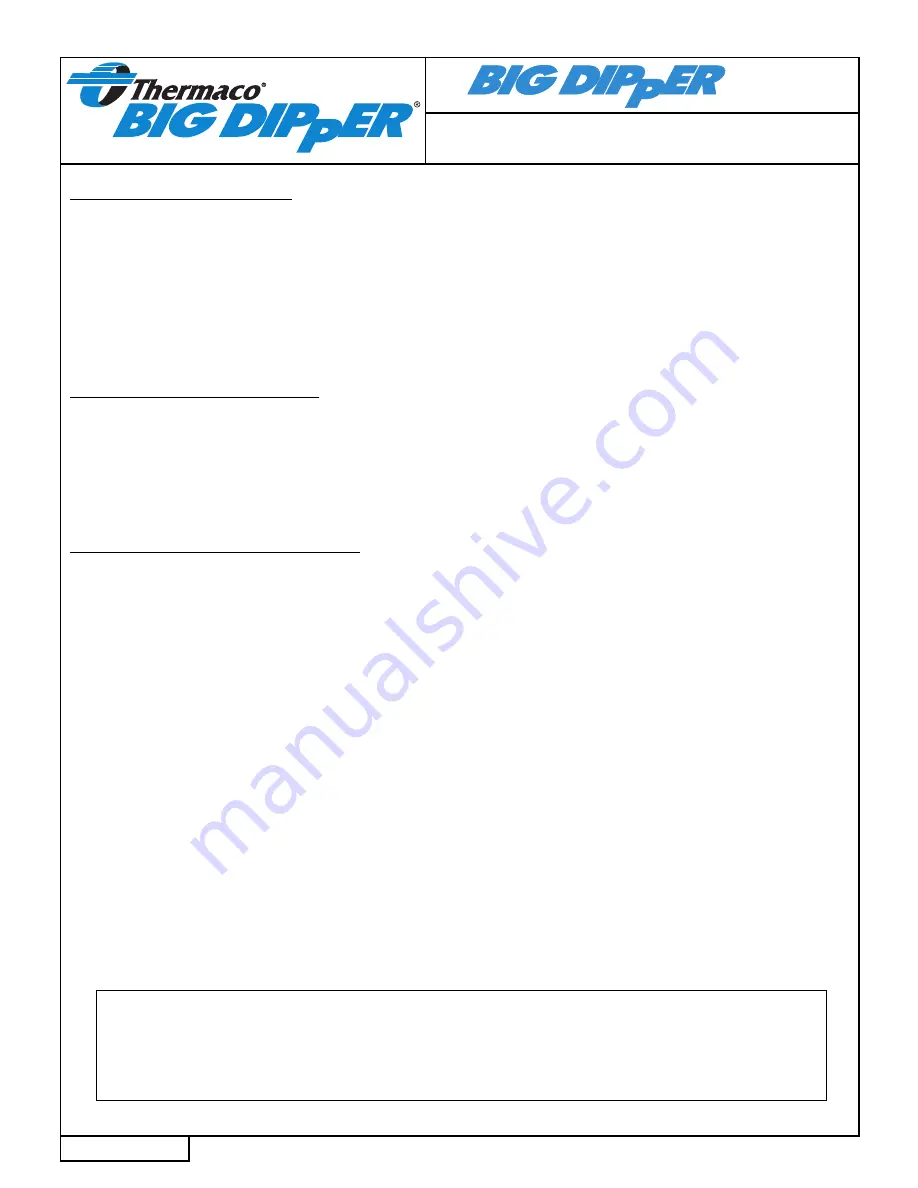
©2001 Thermaco, Inc. All rights reserved • Patented/Patents Pending • Specifications subject to change without notice
Thermaco, Inc. • 646 Greensboro St. • Asheboro, N. C. 27204-2548 • Phone (336) 629-4651
MNL-AST 5
®
AST
Maintenance Procedures
DAILY MAINTENANCE
(A)
Empty the grease/oils collection container, which is located beside the Big Dipper AST, once
each day (or more frequently, if necessary). This grease can typically be put in a rendering
recepticle for pick-up by a local rendering company. The collection container should be
washed periodically.
(B)
Check inside of the solids removal chamber for solids build-up. If excessive solids buildup
is found on the filter baskets, remove the baskets and wash them out with hot water.
WEEKLY MAINTENANCE
(A)
Remove the lid and check the collection trough, the wiper blades and the black rubber sump
outlet hose for any solids build-up. Wipe off any accumulated deposits and assure that the
wiper blades are clipped in place properly.
(B)
Check Timer for proper setting.
QUARTERLY MAINTENANCE
(A)
Check for sludge build-up on the bottom of the Grease/Oils Retention area of the Big
Dipper tank. When accumulation exceeds 25 mm use a long handled spatula to stir up the
sediment while water is flowing through the tank. It may be necessary to drain the tank
and clean the unit thoroughly. A wet vac works well for this purpose. Use hot water to
clean the walls of the tank.
Only perform this process after the system has gone through
its self-cleaning cycle.
(B)
Check the wheel drive sprockets (Part # WDS-1) and skimming wheels (Part # PDA-1) for
wear. If wheel drive sprockets slip on their axle, tighten the set screws or replace if neces
sary
(C)
Check the motor drive coupling (Part #NSC-1) for slippage. If the NSC-1 slips on the shaft,
tighten the set screws or replace if necessary.
(D)
Check the wheel wiper blade assemblies (Part # WWA-1). The wiper blades should rest
against the skimmer wheel and provide an even wiping action on both wheel surfaces.
Replace if they are cracked, excessively worn, or if they fail to skim oils/fats off the skim
mer wheel.
*CAUTION! DISCONNECT POWER TO UNIT BEFORE CLEANING to prevent damage
to the unit and personal injury
*NOTE: Before turning on circuit after cleaning, make sure to fill tank with water
to protect wipers and heater from damage