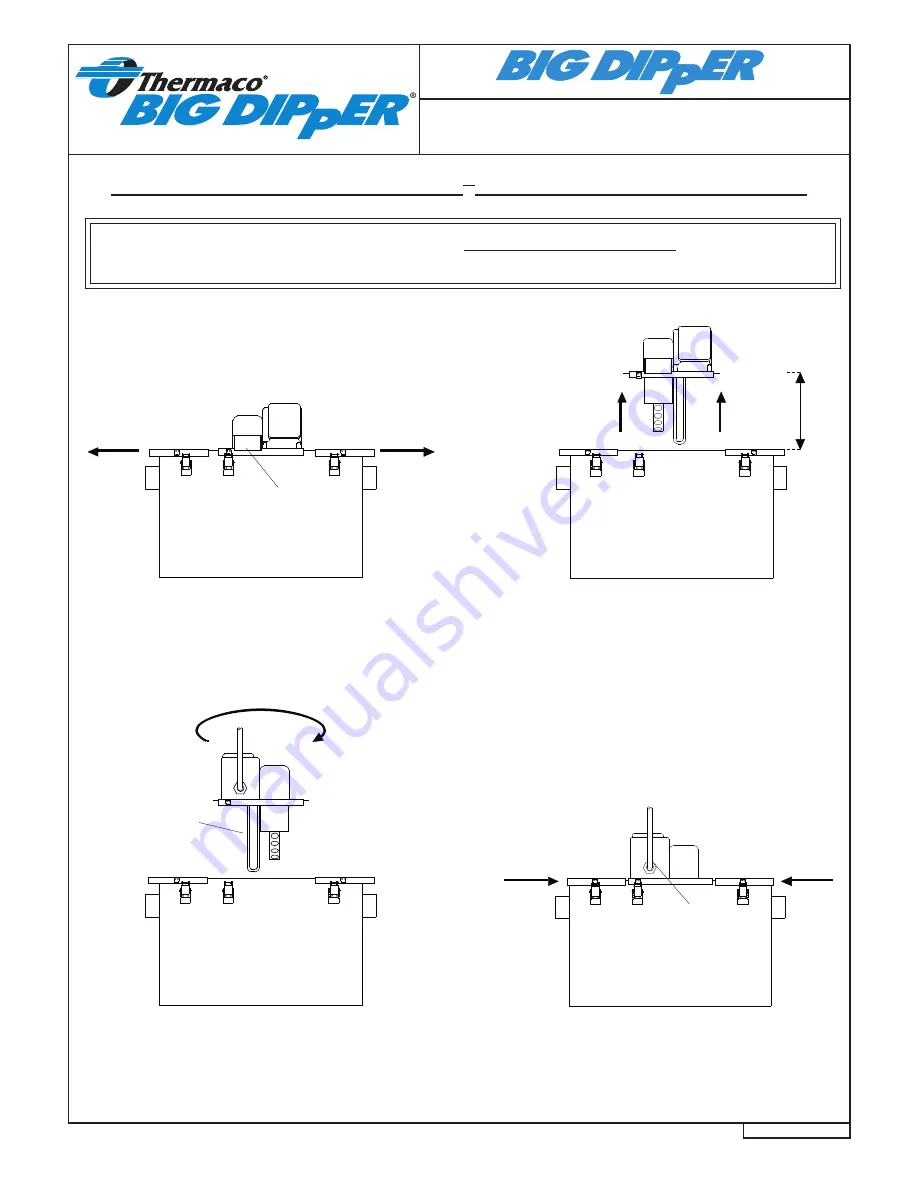
©2005 Thermaco, Inc. All rights reserved • Patented/Patents Pending • Specifications subject to change without notice
Thermaco, Inc. • 646 Greensboro St. • Asheboro, N. C. 27204-2548 • Phone (336) 629-4651
MNL-IS6000 9
®
How To Reverse Big Dipper
®
IS System Unit Operation
1) Unlatch the Unit lid. Pull the
side wings outward.
2) Lift the center module up off of
the unit, ensuring clearance for the
heater.
3) Rotate the center module
180º.
4) Lower the center module back
down on top of the unit. Move the
two side wings back into place & fas-
ten all six latches.
1)
2)
4)
3)
Grease
Outlet
Heater
Power
Cord
How To Reverse Big Dipper
®
IS System Unit Operation
Clearance Required
To Remove Lid
*ALWAYS UNPLUG UNIT BEFORE REMOVING LID
*SYSTEM WILL NOT OPERATE UNLESS CENTER LID LATCHES ARE FASTENED
14.000”