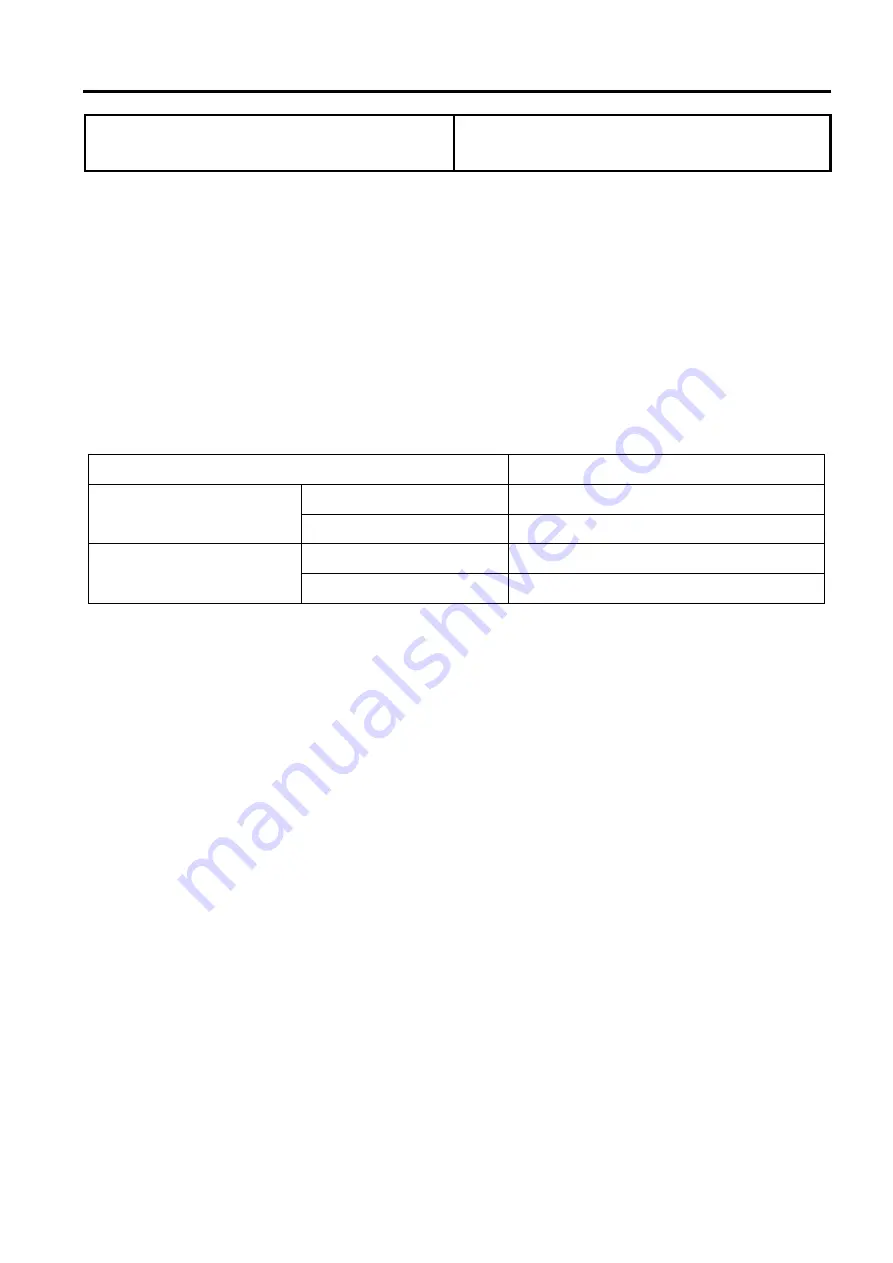
TGB 5. ENGINE REMOVAL
5-1
OPERATIONAL PRECAUTIONS ......... 5-1
ENGINE REMOVAL ............................. 5-2
INSTALLATION OF ENGINE ............... 5-4
OPERATIONAL PRECAUTIONS
General Information
y
Engine must be supported by a bracket or adjustable tool in height.
y
The following parts can be serviced with the engine installed on the frame.
1. Carburetor
2. Driving disk, driving belt, clutch, and transporting disk
3. Final reduction gear mechanism
Specification
Item Specification
Replacement 750
c.c.
Engine Oil Capacity
Disassemble 850
c.c.
Replacement 110
c.c.
Gear Oil Capacity
Disassemble 120
c.c.
Torque Values
Engine suspension bolt
4.5~5.5kgf-m
Engine suspension nut
4.5~5.5kgf-m
Bolt of rear shock absorber upper connection
3.5~4.5kgf-m
Bolt of rear shock absorber lower connection
2.4~3.0kgf-m