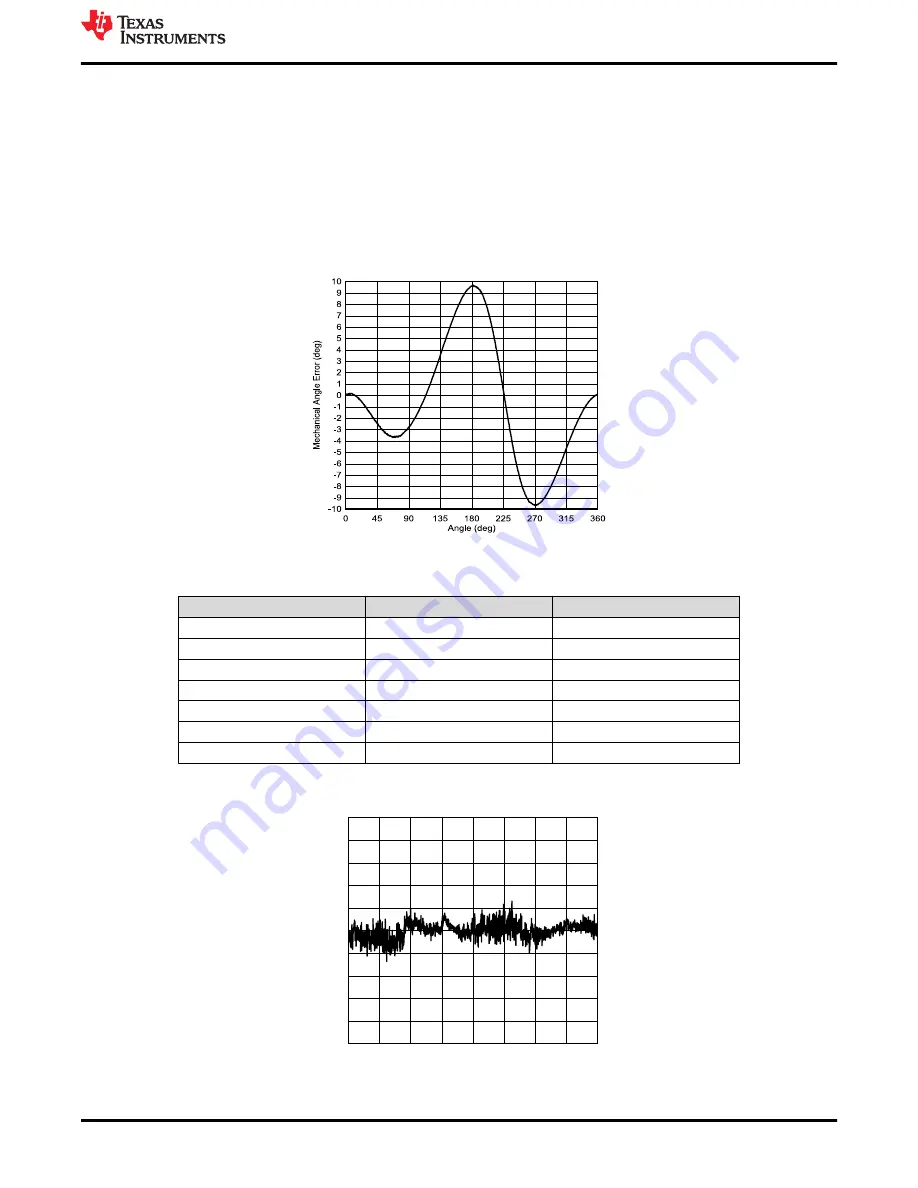
3.3.5 TMAG5170 45° Alignment
, the 45° alignment option dramatically reduces the need to adjust
sensitivity gain by inherently matching the input magnitude observed for each axis. Some sensitivity mismatch
may still be present, which might require minor adjustment.
This alignment was tested in the in-plane alignment at an identical range to the previous results. This
alignment cannot use the CORDIC outputs from
, given that it requires adjustment to the arctangent
calculations to produce a useful result.
The resulting pre-calibrated error after performing phase correction is captured for this alignment and shown in
45° Angle Alignment Mechanical Angle Error
Figure 3-19. 45° Angle Alignment Mechanical Angle Error
Table 3-5. 45° Angle Alignment Harmonic Correction Factors
HARMONIC
α
i
β
i
1
–2.64
4.34
2
0.18
–5.59
3
0.82
0.51
4
–0.43
–0.05
5
0.06
–0.1
6
0
0.05
7
–0.025
–0.005
shows the resulting error after applying the harmonic data.
Angle (deg)
Calibr
at
ed An
gle E
rror (d
eg)
0
45
90
135
180
225
270
315
360
-0.5
-0.4
-0.3
-0.2
-0.1
0
0.1
0.2
0.3
0.4
0.5
Figure 3-20. 45° Calibrated Angle Error
Hardware, Software, Testing Requirements, and Test Results
Absolute Angle Encoder Reference Design With Hall-Effect Sensors for
Precise Motor Position Control
29
Copyright © 2022 Texas Instruments Incorporated