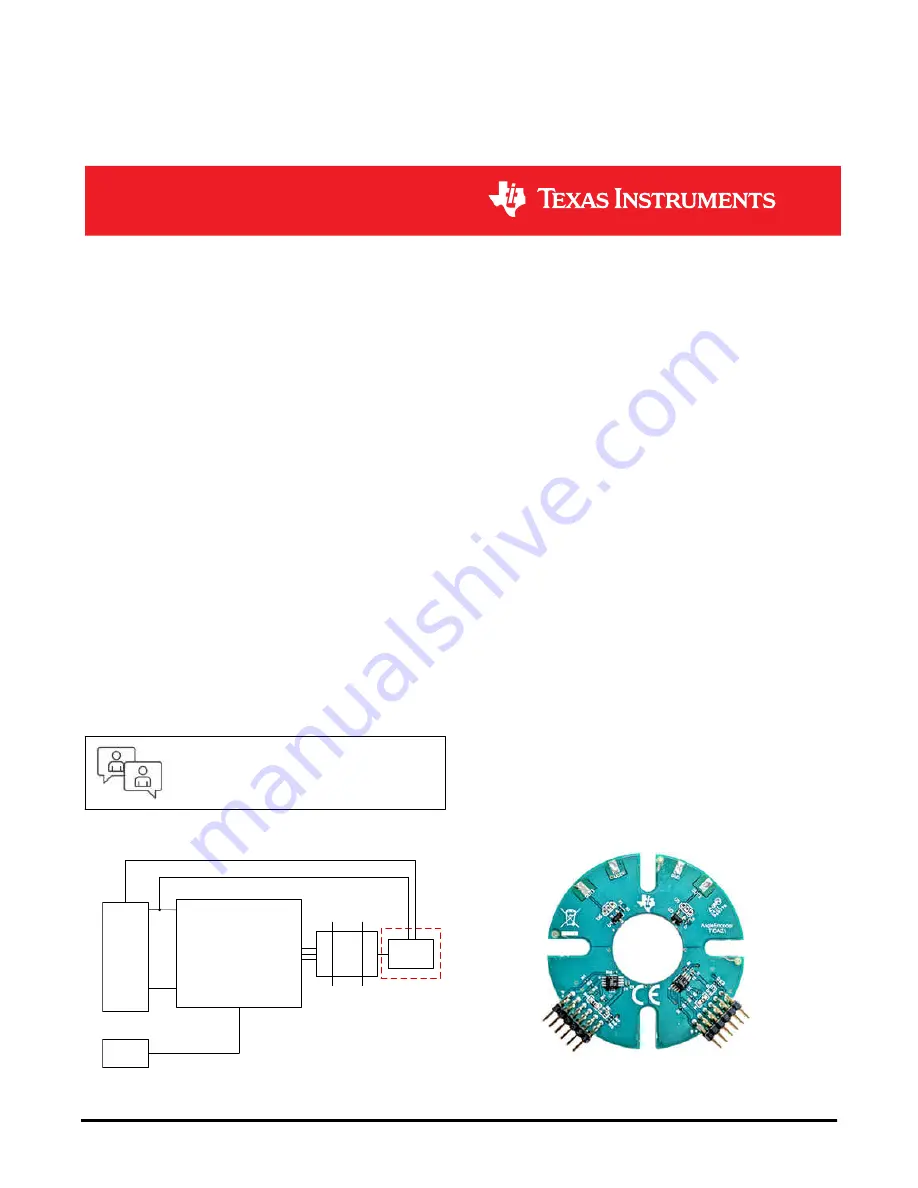
Design Guide: TIDA-060040
Absolute Angle Encoder Reference Design With Hall
Effect Sensors for Precise Motor Position Control
Description
This reference design demonstrates a method for
absolute angle encoding typical in precision motor
control applications such as robotic arm control.
Angle encoding can be achieved using various
magnetic sensing technologies. This is done by
detecting two magnetic flux density, B-field, vector
components which are naturally 90° out of phase. As
the magnet spins, the sensor inputs are sinusoidal
which allows for calculations using trigonometric
properties. However, due to electrical and mechanical
characteristics of the system, it is often necessary
to correct the final result to achieve the greatest
accuracy. Typically in most precision motor control
applications, the final target error is less than
0.1°. This design explores the process for selecting
a magnet, determining placement, and correcting
for system-level imperfections to achieve a highly-
accurate angle measurement.
Resources
Design Folder
Product Folder
Product Folder
Features
• Measure angle in on-axis, in-plane, and off-axis
alignments for flexible alignment and sensor
placement
• Calibration process for accuracy of 0.1°
• Selectable digital SPI communication or analog
output
• Design files with sensor placement guidance
Applications
•
•
•
•
•
•
•
Self-balancing personal transporter
Motor Supply
Voltage
C2000
LaunchPad™
Interface
Motor Driver
Hall-Effect
Sensor
TIDA-060040
BLDC
Motor
3.3 V
SPI Bus
Description
Absolute Angle Encoder Reference Design With Hall-Effect Sensors for
Precise Motor Position Control
1
Copyright © 2022 Texas Instruments Incorporated