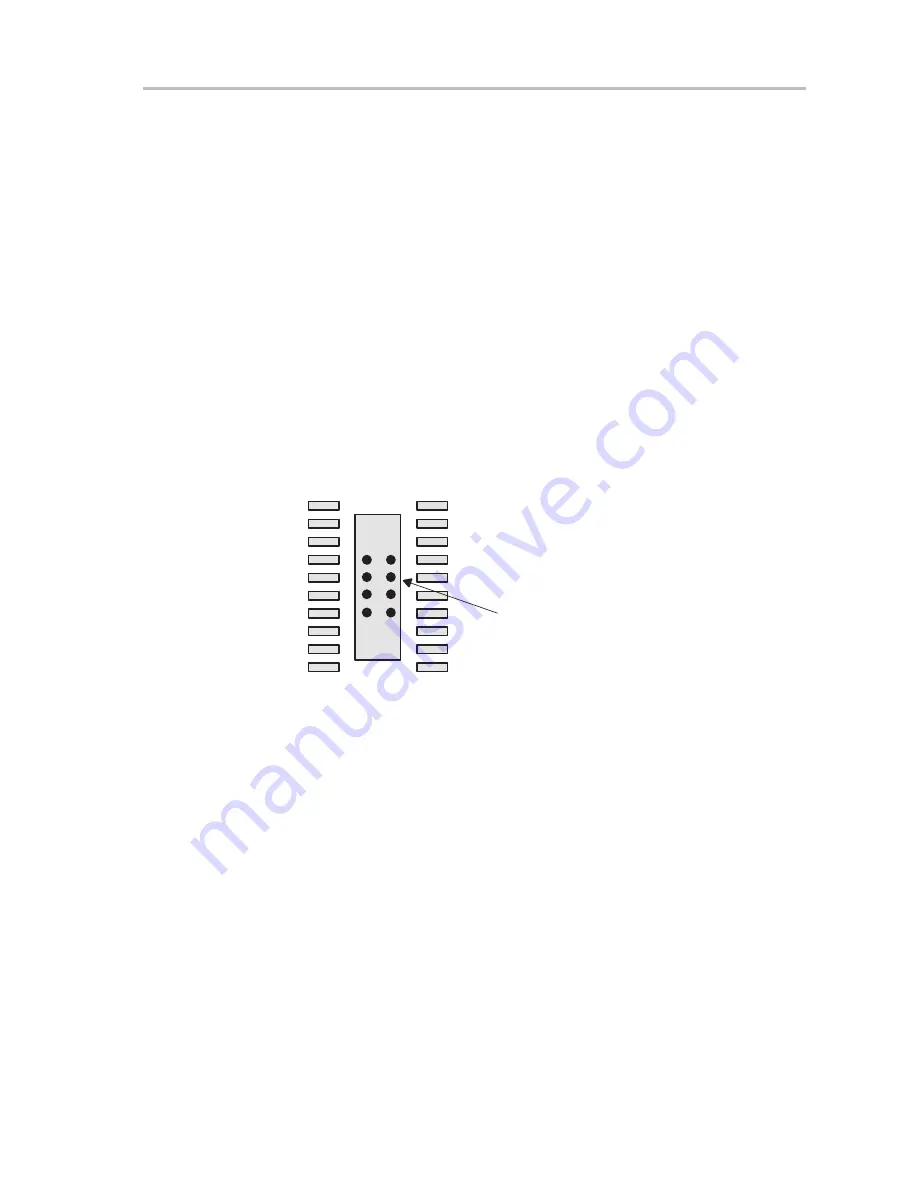
General PowerPAD
t
Design Considerations
1-15
General Information
1.9
General PowerPAD
t
Design Considerations
The THS7001 IC is mounted in a special package incorporating a thermal pad
that transfers heat from the IC die directly to the PCB. The PowerPAD package
is constructed using a downset leadframe. The die is mounted on the
leadframe but is electrically isolated from it. The bottom surface of the lead
frame is exposed as a metal thermal pad on the underside of the package and
makes physical contact with the PCB. Because this thermal pad is in direct
physical contact with both the die and the PCB, excellent thermal performance
can be achieved by providing a good thermal path away from the thermal pad
mounting point on the PCB.
Although there are many ways to properly heatsink this device, the following
steps illustrate the recommended approach as used on the THS7001 EVM,
which is built on a multilayer PCB with an internal ground plane.
1) Prepare the PCB with a top side etch pattern as shown in Figure 1–11.
There should be etch for the leads as well as etch for the thermal pad.
Figure 1–11. PowerPAD PCB Etch and Via Pattern
Thermal pad area (0.12 x 0.17) with 8 vias
(Via diameter = 13 mils)
2) Place 8 holes in the area of the thermal pad. These holes should be 13 mils
in diameter. They are kept small so that solder wicking through the holes
is not a problem during reflow.
3) Additional vias under the package, but outside the thermal pad area, will
improve heat transfer but are not required. These holes should be 25 mils
in diameter. They may be larger because they are not in the area to be
soldered so that wicking is not a problem.
4) Connect all holes, the 8 within the thermal pad area and any others outside
the pad area, to the internal ground plane.
5) When connecting these holes to the ground plane, do not use the typical
web or spoke via connection methodology. Web connections have a high
thermal resistance connection that is useful for slowing the heat transfer
during soldering operations. This makes the soldering of vias that have
plane connections easier. However, in this application, low thermal
resistance is desired for the most efficient heat transfer. Therefore, the
holes under the THS7001 package should make their connection to the
internal ground plane with a complete connection around the entire
circumference of the plated through hole.