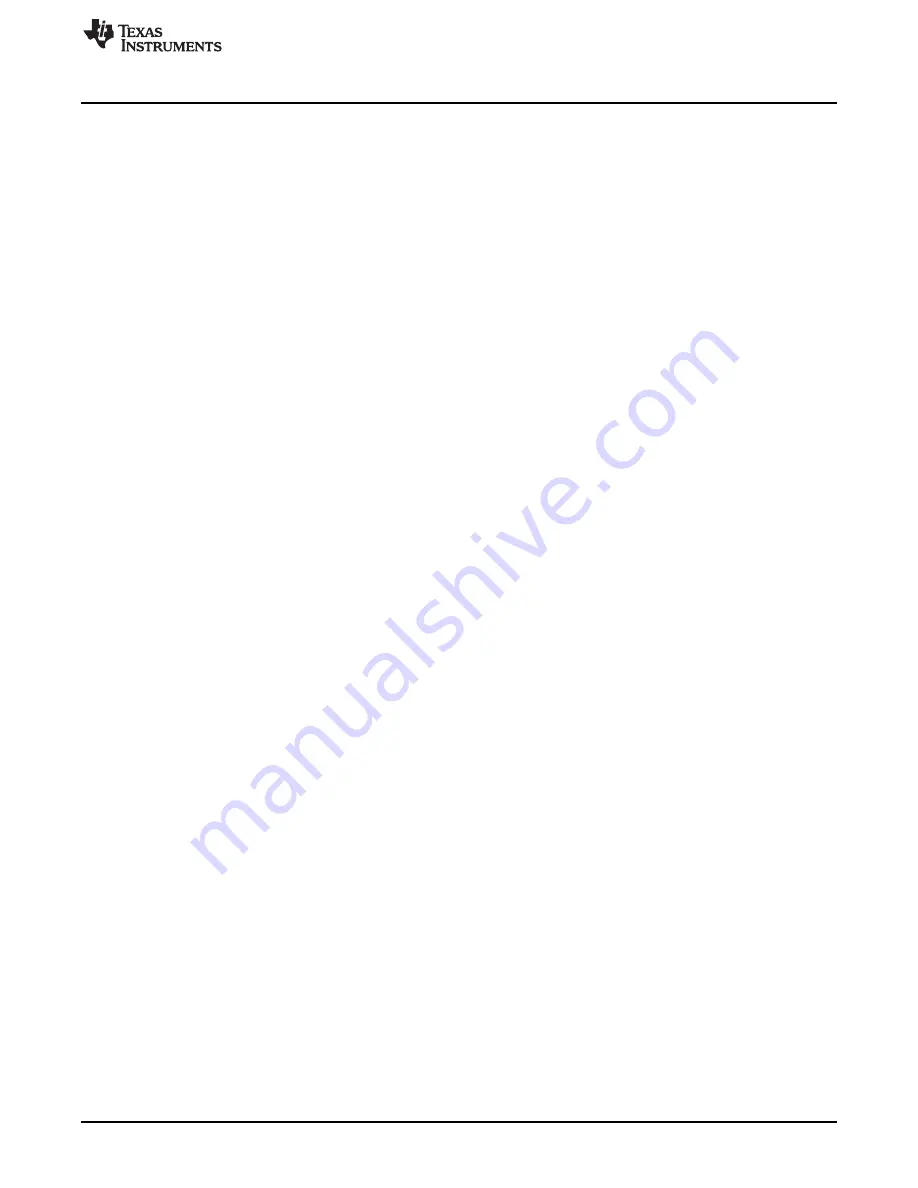
Software Setup and Operation
It is recommended that the user press the 'READ' button at the top of the screen immediately after loading
the software to confirm that the software and cable connections are working properly. The message box at
the top right of the main panel (I
2
C Activity) displays all I
2
C activity. The message box at the bottom (USB
Bridge Connected) displays whether or not the USB-TO-GPIO connection is functional.
The software itself performs no calculations or computations and simply reads and writes to and from the
IC's registers through the I
2
C interface. Each register's bits can either be changed manually by changing
the boxes corresponding to each bit in the panel's top right half, or they can be changed through the drop-
down boxes and buttons in the rest of the panel. Some bits are reserved and not writeable. These will not
allow you to click on them to change their setting. For example, the CHIP_ID register (0x0Ah) is read only
and the TPS650380's main panel does not allow writes to those bits. The I
2
C bus speed is fixed at 100
kbps and this is noted at the bottom of the screen.
Following any change to an individual bit, drop-down box, or button, the user must write the new values to
the registers by either clicking the 'W' button to the left of each affected register or by clicking the 'WRITE'
button at the top of the screen.
In order to reduce the amount of manual reading and writing required, the two drop-downs at the top left of
the screen have been provided to do this automatically. The 'Auto Read' drop down allows the option of
automatically reading all the registers at specific time intervals. The 'Write On Changes' drop-down allows
the option of automatically writing a change to the registers as soon as it is made in the software.
The TPS650380 data sheet is available via the 'Help' menu (Internet access is required). The data sheet
discusses the functionality of the various register bits, which is also briefly repeated here.
The left side of the software main panel is divided into three parts--one for each output voltage. In each of
these sections, the output voltage, ramp rate, and sequencing timer time can be changed. In addition,
there are settings for enabling each output, enabling each output voltage's active output capacitor
discharge circuit on shutdown, changing the mode status of each output voltage (Forced PWM mode or
Power Save Mode), as well as an option to disable the nPG_x bit for each output voltage individually.
These settings correspond to all of registers 0x00h through 0x04h and 0x07h through 0x09h, as well as
portions of registers 0x05h and 0x06h.
In the bottom left corner of the software main panel are various common controls, including enabling the
over-current protection, forcing PWM mode on a ramp down of the output voltage, and resetting bits in the
exceptions register that correspond to various faults. These functions correspond to the remaining bits in
registers 0x05h and 0x06h.
The bottom right corner of the software main panel contains a status output screen. Displayed are the
status of the TPS650380's INT pin (high or low), the status of the exceptions register (0x06h), and the
contents of the CHIP_ID register (0x0Ah) which identifies the IC installed.
Finally, in the upper left corner of the software's main panel is a RESET button which writes a 1 to the
RESET bit of register 0x0Bh.
Circuit Use and Modifications
Besides the required circuitry to operate the TPS650380 (outlined in a white silk screen border on the
PCB), there are additional circuits present on the TPS650380EVM-054 that assist in evaluating the
TPS650380 as a processor power supply solution. Additionally, there are modifications that can be made
to adapt the circuit's performance to the needs of a particular application.
3.1
Load Step Circuit
The TPS650380EVM-054 contains a simple circuit that produces fast load current steps at the output of
the TPS650380. This evaluates the response of the TPS650380 to various load transients that might
occur in the system. An identical circuit is included for each output voltage. To operate the circuit on the
output of DCDC_A, connect a function generator to TP3. The output of the function generator should be a
square wave with a small duty cycle. The output high level controls the gate to source voltage of the
power transistor, Q1, and should be adjusted to generate the desired step current high level. The output
low level sets the step current low level. Good settings to start with are a square wave signal running at
100 Hz and 5% duty cycle going from 0V to 3V. These settings can be adjusted in order to generate the
desired load step.
9
SLVU720A – June 2012 – Revised November 2012
TPS650380EVM-054
Copyright © 2012, Texas Instruments Incorporated