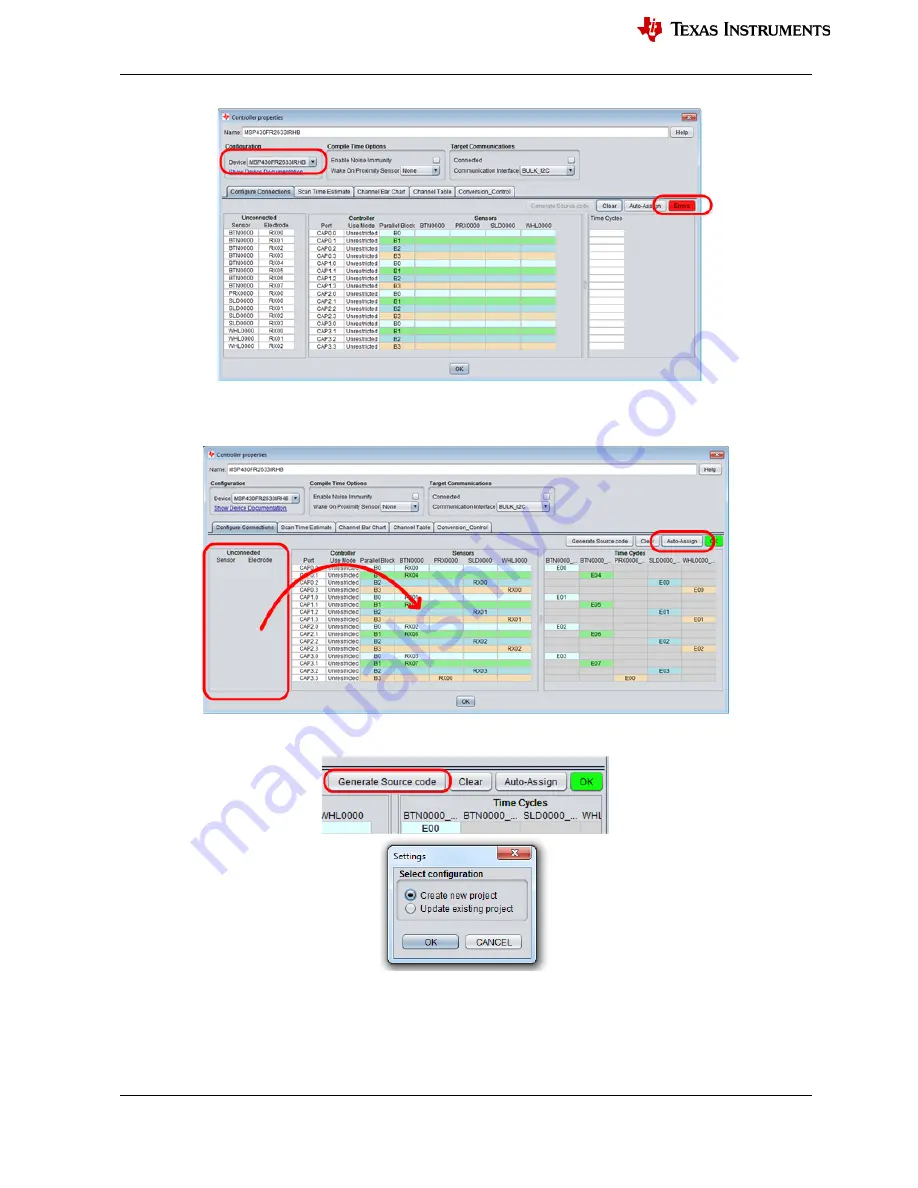
www.ti.com
CapTIvate™ Touch Getting Started Manual
53
Copyright © 2021, Texas Instruments Incorporated
Select the “Auto
-
Assign” button to automatically assign all the sensor ports to appropriate ports on the MSP430.
Note
that the “Errors” LED turns green and “OK”, indicating that all sensor ports have been assigned to controller
ports.
12.
Generate source code
Saving the source code on default location of
CapTIvate™ Design Center
is recommended.