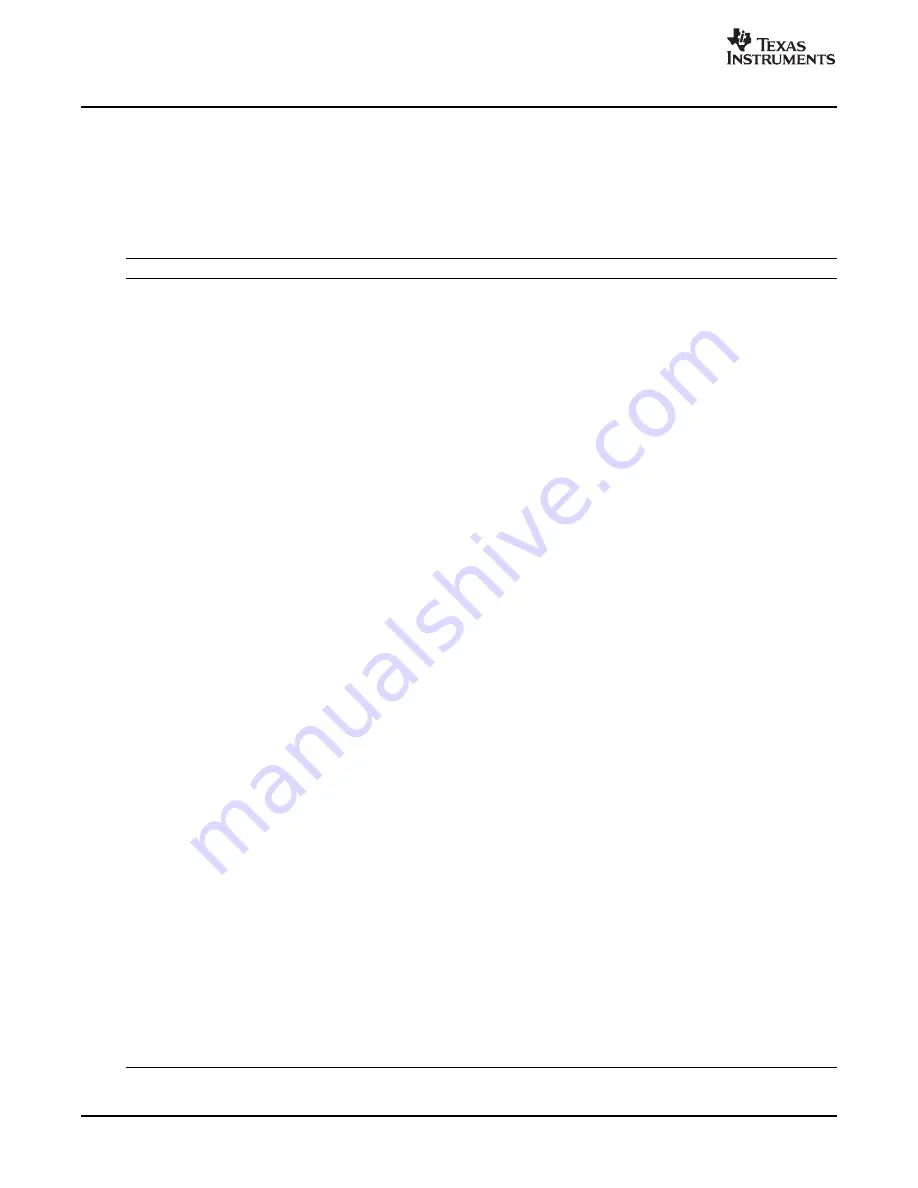
www.ti.com
2.1
Overview
Overview
Table 2-1
lists the seven key submodules together with a list of their main configuration parameters. For
example, if you need to adjust or control the duty cycle of a PWM waveform, then you should see the
counter-compare submodule in
Section 2.3
for relevant details.
Table 2-1. Submodule Configuration Parameters
Submodule
Configuration Parameter or Option
Time-base (TB)
•
Scale the time-base clock (TBCLK) relative to the system clock (SYSCLKOUT).
•
Configure the PWM time-base counter (TBCTR) frequency or period.
•
Set the mode for the time-base counter:
–
count-up mode: used for asymmetric PWM
–
count-down mode: used for asymmetric PWM
–
count-up-and-down mode: used for symmetric PWM
•
Configure the time-base phase relative to another ePWM module.
•
Synchronize the time-base counter between modules through hardware or software.
•
Configure the direction (up or down) of the time-base counter after a synchronization event.
•
Configure how the time-base counter will behave when the device is halted by an emulator.
•
Specify the source for the synchronization output of the ePWM module:
–
Synchronization input signal
–
Time-base counter equal to zero
–
Time-base counter equal to counter-compare B (CMPB)
–
No output synchronization signal generated.
Counter-compare (CC)
•
Specify the PWM duty cycle for output EPWMxA and/or output EPWMxB
•
Specify the time at which switching events occur on the EPWMxA or EPWMxB output
Action-qualifier (AQ)
•
Specify the type of action taken when a time-base or counter-compare submodule event occurs:
–
No action taken
–
Output EPWMxA and/or EPWMxB switched high
–
Output EPWMxA and/or EPWMxB switched low
–
Output EPWMxA and/or EPWMxB toggled
•
Force the PWM output state through software control
•
Configure and control the PWM dead-band through software
Dead-band (DB)
•
Control of traditional complementary dead-band relationship between upper and lower switches
•
Specify the output rising-edge-delay value
•
Specify the output falling-edge delay value
•
Bypass the dead-band module entirely. In this case the PWM waveform is passed through
without modification.
PWM-chopper (PC)
•
Create a chopping (carrier) frequency.
•
Pulse width of the first pulse in the chopped pulse train.
•
Duty cycle of the second and subsequent pulses.
•
Bypass the PWM-chopper module entirely. In this case the PWM waveform is passed through
without modification.
Trip-zone (TZ)
•
Configure the ePWM module to react to one, all, or none of the trip-zone pins.
•
Specify the tripping action taken when a fault occurs:
–
Force EPWMxA and/or EPWMxB high
–
Force EPWMxA and/or EPWMxB low
–
Force EPWMxA and/or EPWMxB to a high-impedance state
–
Configure EPWMxA and/or EPWMxB to ignore any trip condition.
•
Configure how often the ePWM will react to each trip-zone pin:
–
One-shot
–
Cycle-by-cycle
•
Enable the trip-zone to initiate an interrupt.
•
Bypass the trip-zone module entirely.
20
ePWM Submodules
SPRU791D – November 2004 – Revised October 2007
Submit Documentation Feedback
Summary of Contents for 28xxx
Page 2: ...2 SPRU791D November 2004 Revised October 2007 Submit Documentation Feedback...
Page 8: ...List of Tables 8 SPRU791D November 2004 Revised October 2007 Submit Documentation Feedback...
Page 12: ...Read This First 12 SPRU791D November 2004 Revised October 2007 Submit Documentation Feedback...
Page 68: ...ePWM Submodules 68 SPRU791D November 2004 Revised October 2007 Submit Documentation Feedback...
Page 116: ...Registers 116 SPRU791D November 2004 Revised October 2007 Submit Documentation Feedback...