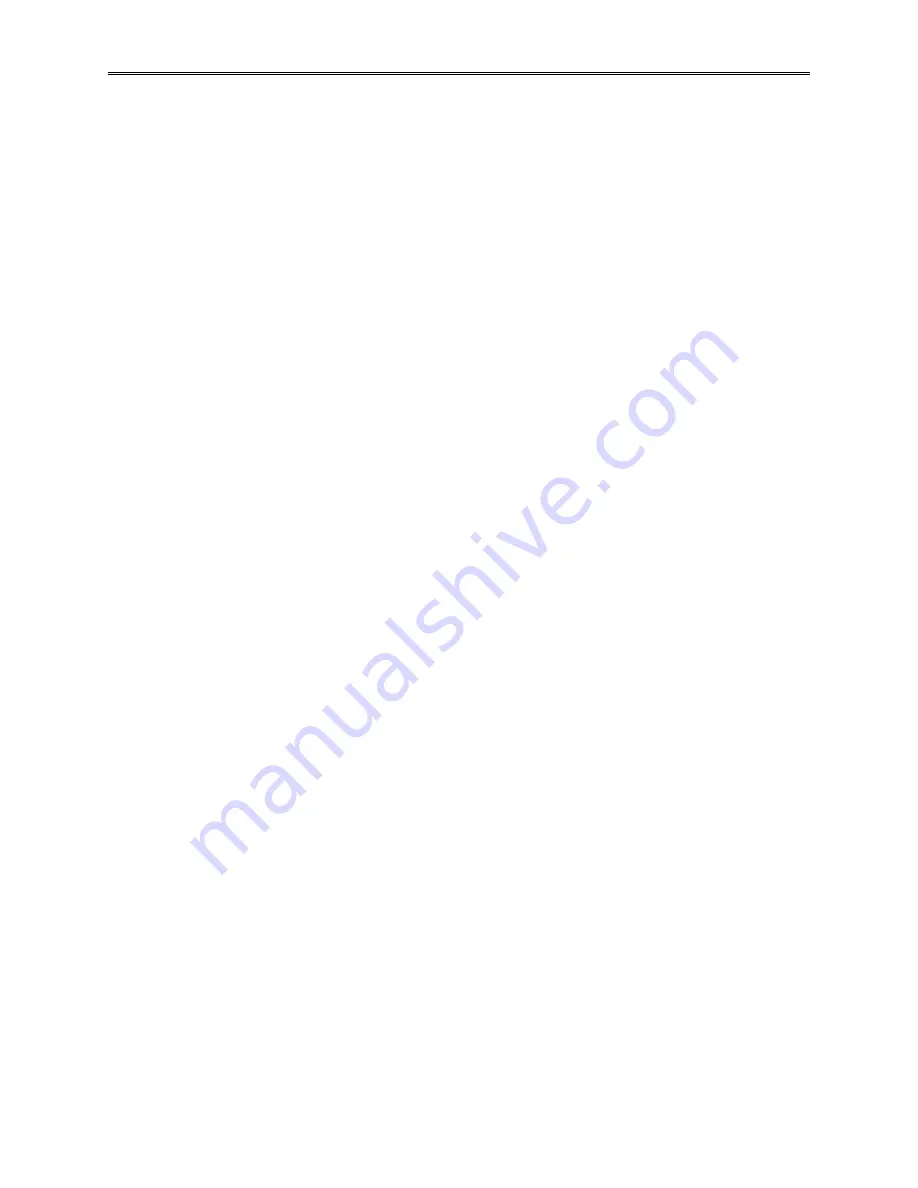
Chapter 2 – Installation
TestEquity 3007C Temperature Chamber
Page 2-5
The recommended connection method from your source of liquid nitrogen is either a length of
3/8-inch OD, ASTM A269, 0.049-inch Wall, Seamless 316 series stainless steel tube terminated
on one end with a 37-degree JIC flare fitting and insulated with closed cell, vapor sealed foam;
or alternately a commercially manufactured vacuum jacketed liquid nitrogen connecting tube
designed for this service. For urethane and polyisocyanurate (Dow Trymer) foam, typical long-
term operation liquid nitrogen insulation wall thickness is approximately 2-inches per side (4-
inches OD).
If a 3/8-inch OD tube stainless steel tube is selected, the insulation should be installed flush
against the non-metallic thermal breaker around the LN2 Inlet fitting on the chamber. If a
vacuum jacketed tube is selected, a short adapter may be required to make the final connection to
the chamber’s LN2 Inlet fitting. For a vacuum jacketed connection, a short ring of closed cell,
vapor sealed foam should be applied flush against the thermal breaker on one side and
overlapping the vacuum jacket by approximately six inches on the other side.
Support all liquid nitrogen carrying lines with ridged hangers to prevent excessive flexing when
cold.
Chamber Relief Vent Considerations with Liquid Nitrogen
For installation in enclosed areas of any size or when ventilation in the room is limited:
•
The workspace vent at the top of the chamber must be piped outside of the building to
atmosphere with a backpressure-free, vapor-tight, insulated tube.
•
The enclosed room must be adequately ventilated to prevent the buildup of nitrogen gas due
to leakage, pressure relief valve operation, or chamber door opening.
•
An automatic, Low Level Oxygen Alarm must be installed to alert operators of potentially
dangerous conditions within the enclosed room. These devices are available from a number
of sources. An example is the Chemgard Gas Monitor from MSA (Mine Safety Appliances
Company) in Pittsburgh, PA (800-672-2222, www.msanorthamerica.com).
For installation in large factory areas, with open doors and adequate ventilation certified by a
qualified Mechanical Engineer:
•
The vent at the top of the chamber can discharge directly into the factory. If desired, the vent
can be extended upward approximately two feet with a length of insulated tubing to prevent
frost buildup on the top of the chamber.