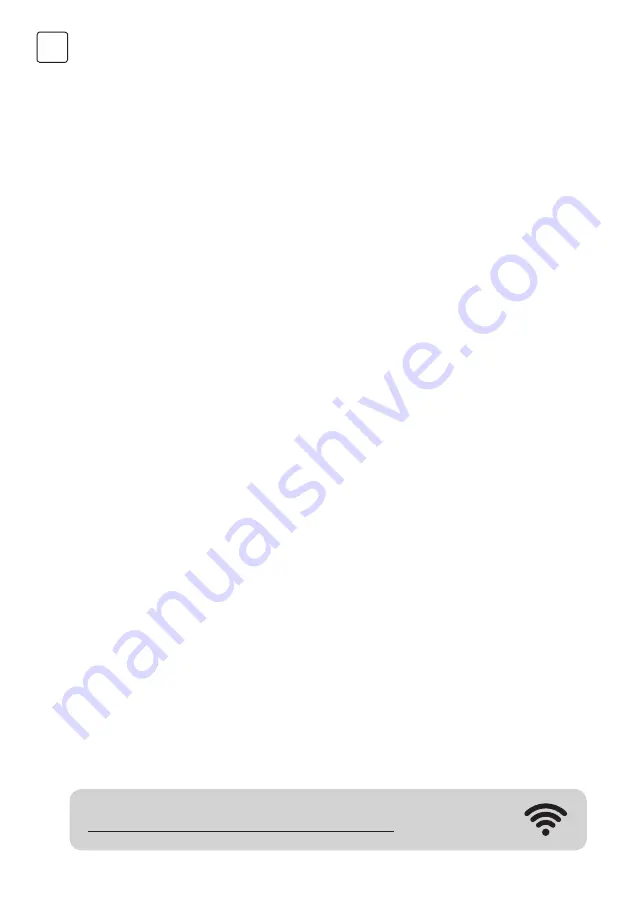
ENG
and all its detail. It is recommended good practice that all refrigerants are recovered safely. Prior to the task
being carried out, an oil and refrigerant sample shall be taken in case analysis is required prior to re-use of
reclaimed refrigerant. It is essential that electrical power is available before the task is commenced.
a. Become familiar with the equipment and its operation.
b. Isolate system electrically.
c. Before attempting the procedure, ensure that:
- mechanical handling equipment is available, if required, for handling refrigerant cylinders;
- all personal protective equipment is available and being used correctly;
- the recovery process is supervised at all times by a competent person;
- recovery equipment and cylinders conform to the appropriate standards.
d. Pump down refrigerant system, if possible.
e. If a vacuum is not possible, make a manifold so that refrigerant can be removed from various parts of the
system.
f. Make sure that cylinder is situated on the scales before recovery takes place.
g. Start the recovery machine and operate in accordance with manufacturer’s instructions.
h. Do not overfill cylinders. (No more than 80 % volume liquid charge).
i. Do not exceed the maximum working pressure of the cylinder, even temporarily.
j. When the cylinders have been filled correctly and the process completed, make sure that the cylinders and
the equipment are removed from site promptly and all isolation valves onthe equipment are closed off.
k. Recovered refrigerant shall not be charged into another refrigeration system unless it has been cleaned and
checked.
24.
Labelling
Equipment shall be labelled stating that it has been de-commissioned and emptied of refrigerant. The label
shall be dated and signed. Ensure that there are labels on the equipment stating the equipment contains
flammable refrigerant.
25.
Recovery
When removing refrigerant from a system, either for servicing or decommissioning, it is recommended good
practice that all refrigerants are removed safely.
When transferring refrigerant into cylinders, ensure that only appropriate refrigerant recovery cylinders are
employed. Ensure that the correct number of cylinders for holding the total system charge are available. All
cylinders to be used are designated for the recovered refrigerant and labelled for that refrigerant (i.e. special
cylinders for the recovery of refrigerant). Cylinders shall be complete with pressure-relief valve and associated
shut-off valves in good working order. Empty recovery cylinders are evacuated and, if possible, cooled before
recovery occurs.
The recovery equipment shall be in good working order with a set of instructions concerning the equipment
that is at hand and shall be suitable for the recovery of all appropriate refrigerants including, when applicable,
flammable refrigerants. In addition, a set of calibrated weighing scales shall be available and in good working
order. Hoses shall be complete with leak-free disconnect couplings and in good condition. Before using the
recovery machine, check that it is in satisfactory working order, has been properly maintained and that any
associated electrical components are sealed to prevent ignition in the event of a refrigerant release. Consult
manufacturer if in doubt.
The recovered refrigerant shall be returned to the refrigerant supplier in the correct recover cylinder, and the
relevant waste transfer note arranged. Do not mix refrigerants in recovery units and especially not in cylinders.
If compressors or compressor oils are to be removed, ensure that they have been evacuated to an acceptable
level to make certain that flammable refrigerant does not remain within the lubricant. The evacuation process
shall be carried out prior to returning the compressor to the suppliers. Only electric heating to the compressor
body shall be employed to accelerate this process. When oil is drained from a system, it shall be carried out
safely.
Smart WiFi app user manual can be found at:
https://tesla.info/wp-content/uploads/pdf/TeslaTTWiFiapp.pdf
Summary of Contents for TT26EX21-0932IA
Page 74: ...74 BG 4A 250V III 50 cm 8...
Page 75: ...75 BG...
Page 76: ...76 BG No 1 2 3 4 LED 5 6 7 8 9 10 11 12 No 13 14 15 16 17...
Page 77: ...77 BG No Led 1 SLEEP SLEEP 2 1 Timer 2 3 TIMER Timer COOL 3 HEAT 5 COOL...
Page 81: ...81 BG 1 2 3 4 1m flashing swing 1 1 2 deactivate 2 2 2 1 2 deactivate flashing 3 2 2 Fan...
Page 88: ...88 BG 10Pa 5g 10g A 5 B 10 C D A B 22 R290 R161 R410A 32 Water drain pipe...
Page 89: ...89 BG mm 250cm...
Page 90: ...90 BG 1 65 2 1 2 3 4 PCB 1 2 32mm 3 4 5...
Page 91: ...91 BG 3 1 3 1 2 3 4 R32 R290 1 2 3 4 1 2...
Page 92: ...92 BG 1 2 3 4 1 25mm 2 1 2 3 4 5 6 1...
Page 94: ...94 BG 1 2 3 4 ON OFF FAN MODE TIMER 6 1 4 7 7 1 2 8 1 8 8 t...
Page 98: ...98 BG 6 N B LCD 1 2 3 45 C 4 5 1 2 40 3 1 2 3...
Page 99: ...99 BG TIMER ON LIGHT...
Page 100: ...100 BG IPM PCB EEPROM 1 2 4m2 3 4 4m2 5 6 7 8 9 10 11 12 13 14 15...
Page 101: ...101 BG 16 1 2 3 4 5 CO2 6 7 8 9 17 1...
Page 102: ...102 BG 2 18 19 20 21 LFL 25 OFN 22 OFN OFN OFN...
Page 105: ...105 24 13 12 TESLA 1 2 2 1 2 2 TESLA 2 3 2 4 2 5 2 6 2 7 2 8 2 9 2 10 2 11...
Page 106: ...106 2 12 3 4 5 6 7 8 112 115 119 112 1 2 1 2 3 113 1 2 3 2 114 4 5 114 1 113 1 2 2 3...
Page 107: ...107 115 4 115 1 2 1 3 1 1 10 02 9700970 02 9700971 9 30 19 00 10 00 16 00...
Page 108: ...108...
Page 109: ...109 GR 4A 250V H 50 cm 8...
Page 110: ...110 GR...
Page 111: ...111 GR 1 2 3 4 LED 5 6 7 8 9 10 11 12 13 14 15 16 17...
Page 112: ...112 GR 1 SLEEP 2 1 2 3 3 5...
Page 114: ...114 GR HEALTH 3 Ap 1 2 3 4 AUTO 5 COOL 6 DRY 7 FAN 8 HEAT 9 ECO ECO...
Page 116: ...116 GR 1 2 3 4 1 m 1 1 2 2 2 2 1 2 2 2...
Page 117: ...117 GR FAN MODE COOL 1 2 3 MODE HEAT 1 2 3 MODE DRY MODE FAN MODE AUTO 2 10...
Page 123: ...123 GR 10 Pa 5 g 10 g A 5 B o 10 A B R22 R290 R161 R410A R32...
Page 124: ...124 GR mm 250 cm...
Page 125: ...125 GR 1 65 2 1 2 3 4 1 2 32 mm 3 4 5...
Page 126: ...126 GR 3 1 3 1 2 3 4 R32 R290 1 2 3 4 1 2 NAI OXI NAI OXI OXI...
Page 127: ...127 GR 1 2 3 4 1 25 mm 2 1 2 3 4 5 6 1 1...
Page 129: ...129 GR 1 2 3 4 MODE 3 2 3 6 1 4 7 7 1 2 8 1 8 8...
Page 133: ...133 GR 6 LCD 1 2 3 45 oC 4 5 1 2 40 C 3 1 2 3...
Page 134: ...134 GR...
Page 135: ...135 GR IPM EEPROM 1 2 4 m2 3 4 4 m2 5 6 7 8 9 10 11 12 13 14 15...
Page 136: ...136 GR 16 1 2 3 4 5 CO2 6 7 8 9...
Page 137: ...137 GR 17 1 2 18 19 20 21 LFL 25 OFN 22 OFN...
Page 138: ...OFN OFN 23 80 24 25...
Page 139: ...139 GR SmartWiFi https tesla info wp content uploads pdf TeslaTTWiFiapp pdf...
Page 141: ...141 7 service TESLA TESLA 8 9 TESLA 10 email warranty gr comtrade com...
Page 142: ...142 1 Service 2 Service 3 Service 4 Service 5 Service 6 Service 7 Service 8 Service 9 Service...
Page 208: ...208 MK 4A 250V III 50 cm 8...
Page 209: ...209 MK...
Page 210: ...210 MK 1 2 3 4 LED 5 6 7 8 9 10 11 12 13 14 15 16 17...
Page 211: ...211 MK Led 1 SLEEP 2 1 2 3 COOL 3 HEAT 5 COOL...
Page 215: ...215 MK 2 LRO 3 AAA 1 5 V ECO EKO 1 2 3 4 1 m...
Page 216: ...216 MK Swing 1 FLAP 1 2 swing 2 2 2 1 2 swing 2 2 COOL MODE COOL 1 2 3...
Page 223: ...223 MK 10 Pa 5 g 10 g 5 10 22 R290 R161 R410A 32...
Page 224: ...224 MK mm 250...
Page 225: ...225 MK 1 65 2 1 2 3 4 1 2 32 mm 3 4 5...
Page 226: ...226 MK 3 1 3 1 2 3 4 R32 R290 1 2 3 4 1 2...
Page 227: ...227 MK 1 2 3 4 1 25 mm 2 1 2 3 4 5 6 1...
Page 229: ...229 MK 1 2 3 4 ON OFF FAN MODE TIMER 6 1 4 7 7 1 2 8 1 8 8...
Page 233: ...233 MK 6 LCD 1 2 3 45 C 4 5 1 2 40 C 3 1 2 3...
Page 234: ...234 MK TIMER ON COOLING DEHUMIDIFYING DRY LIGHT...
Page 235: ...235 MK IPM PCB EEPROM 1 2 4 m2 3 4 4m2 5 6 7 8 9 10 11 12 13 14 15...
Page 236: ...236 MK 16 i 1 2 3 4 5 CO2 6 7 8 a a 9 17...
Page 237: ...237 MK 1 2 18 19 20 21 LFL 25 oxygen free nitrogen OFN 22...
Page 238: ...23 a 80 24 25...
Page 239: ...239 MK WiFi https tesla info wp content uploads pdf TeslaTTWiFiapp pdf...
Page 241: ...241 1 30 2 3 3 12 12 12...
Page 242: ...242...
Page 243: ...243 Customer signature m C C V 15 1 2 3 C C V C C V...
Page 352: ...www tesla info...