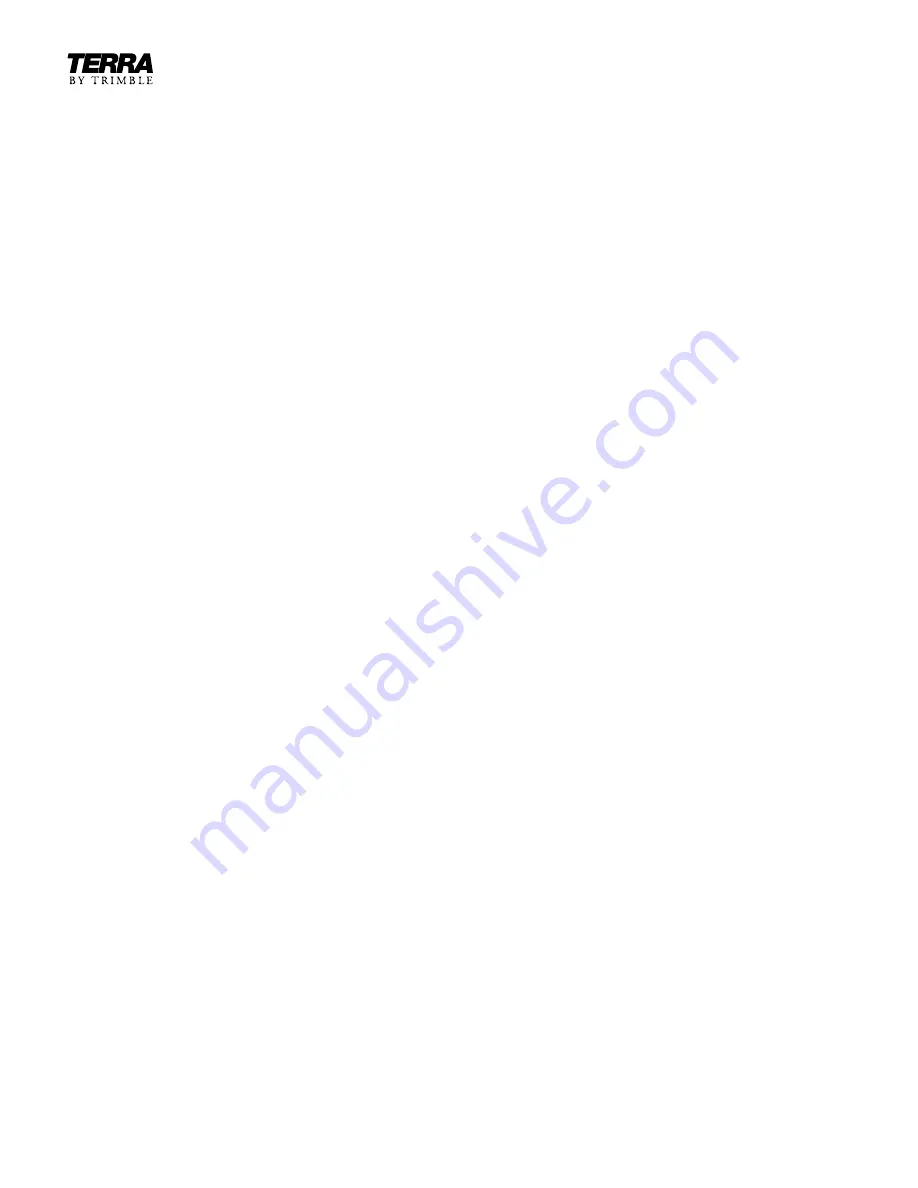
10
Revision G
October 14, 1996
3.3.2
ANTENNAS
The three cardinal points for antenna installation are location, mounting and
electrical characteristics.
Antenna Location:
Provide an area where shadowing of the antenna will not occur (eg. blocking of the
signal by other parts of the aircraft). Remember that at VHF frequencies and above,
direct line of sight signals are required from ground stations to the antenna and vice-
versa for maximum effective range. Consider that close proximity of an antenna to
other antennas or noise sources may create interference problems. Read carefully
and follow closely the recommendations of the antenna manufacturer about antenna
location.
Antenna Mounting:
Proper attachment of any antenna to the aircraft surface is of primary importance.
Carefully clean all paint and corrosion off the mounting surface and apply an anti-
corrosion treatment. Do the same to the inside surface if a backing or nut plate is to
be used. Mount the antenna securely per the antenna manufacturer’s
recommendations and check carefully to insure good electrical bonding. Do not
mount any antenna to doors, hatches, inspection plates or other moveable surfaces
because proper bonding to the aircraft surface cannot be accomplished. After proper
mounting and bonding is achieved, a bead of high quality RTV around the junction
of the antenna base and the aircraft surface will prevent water seepage and corrosion
from forming between the antenna base and aircraft surface.
Antenna Electrical Characteristics:
Use the antenna supplied with the avionics equipment, or if not supplied, the
antenna(s) recommended by the avionics manufacturer. If no specific antenna is
recommended, choose an antenna which provides good service for the frequency
range and the service conditions of the aircraft (eg. speed, altitude, etc.). If a signal
splitter is to be used, compare the specifications carefully to the application. Many
installation problems are encountered with improper application of signal splitters!
If in doubt, test the power and frequency characteristics of the splitter on the bench to
be sure.
Simple antenna problems such as shorting or open circuit problems can be
determined by use of an ohmmeter, although certain types of antennas may require
use of ramp test equipment to check radiation. But, by far, the most common antenna
problems are diagnosed to be coax or connectors, antenna bonding, or signal splitters.
Never allow an aircraft antenna to be painted.
3.3.3
WIRING AND HARNESSING
Construct the installation wiring harness carefully from the avionics manufacturer’s
wiring diagram. Be extremely careful to note recommended wire sizes, the need for
shielded wiring (if any), and decide upon any optional wiring to be included.
Measure carefully and plan the harness layout to avoid interference of the cable
harness with existing avionics, instruments or controls.
Summary of Contents for TRI NAV
Page 9: ...6 Revision G October 14 1996 THIS PAGE INTENTIONALLY LEFT BLANK ...
Page 10: ...Revision G October 14 1996 7 Figure 2 1 TRI NAV Display ...
Page 11: ...8 Revision G October 14 1996 THIS PAGE INTENTIONALLY LEFT BLANK ...
Page 17: ...14 Revision G October 14 1996 THIS PAGE INTENTIONALLY LEFT BLANK ...
Page 18: ...Revision G October 14 1996 15 Figure 3 1 TRI NAV TRI NAV C Jumper Wire Location ...
Page 19: ...16 Revision G October 14 1996 THIS PAGE INTENTIONALLY LEFT BLANK ...
Page 20: ...Revision G October 14 1996 17 18 Figure 3 2 Tri Nav Interconnect Diagram ...
Page 22: ...20 Revision G October 14 1996 THIS PAGE INTENTIONALLY LEFT BLANK ...
Page 23: ...Revision G October 14 1996 21 Figure 3 3 TRI NAV ADJUSTMENT ...
Page 24: ...22 Revision G October 14 1996 THIS PAGE INTENTIONALLY LEFT BLANK ...
Page 26: ...24 Revision G October 14 1996 THIS PAGE INTENTIONALLY LEFT BLANK ...