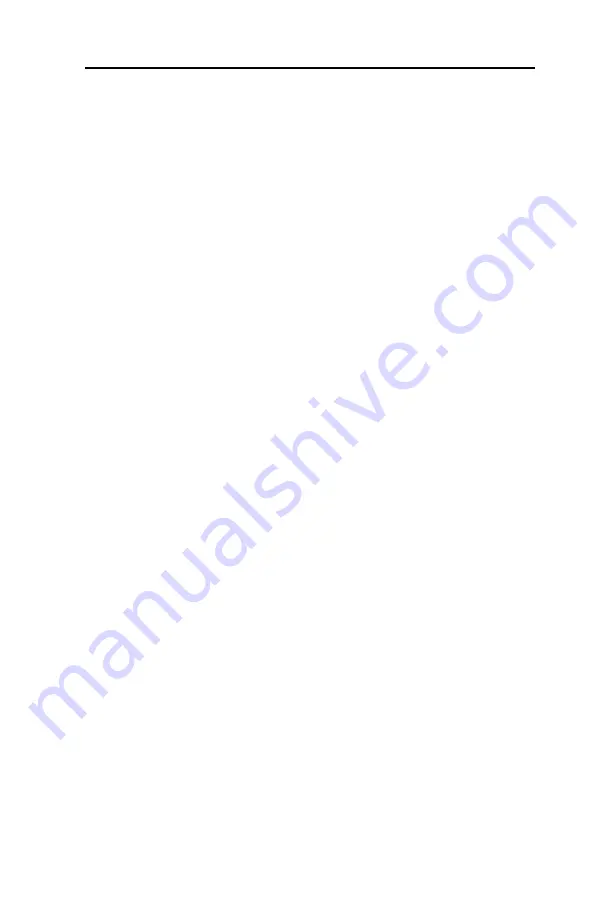
•
Clean the machine prior to beginning work. Clean especially the connections
and screw couplings of oil, fuel and upkeep materials at the beginning of
the maintenance/repair job.
•
Do not use flammable liquids to clean the machine.
•
Perform tasks on the machine that involve welding or grinding only if
approved by the manufacturer. Clean the machine and the work area of dust
and any combustible materials before welding or grinding to avoid fire or
explosion.
•
Before cleaning the machine with water jets (high pressure cleaner) or other
cleaning agents, cover or seal over all openings in which water or cleaning
agents should not penetrate for safety and/or functional reasons. Electrical
motors, switch panels and plug connections are especially subject to
damage. Before cleaning, inspect all fuel, engine oil and hydraulic oil lines
for leaks, loose connections, rubbed spots and damage. Repair or replace
any damaged components immediately.
•
When working with oils, greases and other chemical substances, observe all
safety requirements that apply to the product in question.
•
Ensure that fuels, lubricants and coolants as well as replaced parts are
disposed of in an environmentally proper manner.
•
Proceed carefully when working with hot lubricants, coolants and fuels
(danger of burns and scalding).
Relieve Hydraulic System Pressure
Prior to attempting any hydraulic maintenance or repair, relieve hydraulic
system pressure by performing the following:
1.
Remove any attachment, then shut the machine down as described in
section 5.13 of this manual.
Note:
When lowering the lift arms, lower them to the frame stops (or onto
the lift arm brace if the lift arms are to remain up for service). Fully curl the
quick attach (or you can extend it to the ground if the loader is down), then
activate the float function (section 4.3.1 of this manual) momentarily to
ensure there is no pressure left in the lift arm circuit.
2.
Turn the continuous auxiliary hydraulic switch off and ensure the
intermittent auxiliary switch is in it’s neutral resting position (section 4.7 of
this manual).
3.
Make sure the drive and lift arm controls are in neutral positions (controls
are spring centered, resting position is neutral).
4.
Relieve auxiliary hydraulic residual pressure (step 2 section 4.7 of this
manual).
2 SAFETY
25
RT-60/R160T/R190T ROW O&M
0404-659 2016-05
Summary of Contents for R190T-ROW
Page 7: ...6 RT 60 R160T R190T ROW O M 0404 659 2016 05 This Page Intentionally Left Blank...
Page 29: ...28 RT 60 R160T R190T ROW O M 0404 659 2016 05 This Page Intentionally Left Blank...
Page 31: ...30 RT 60 R160T R190T ROW O M 0404 659 2016 05 This Page Intentionally Left Blank...
Page 37: ...36 RT 60 R160T R190T ROW O M 0404 659 2016 05 This Page Intentionally Left Blank...
Page 47: ...46 RT 60 R160T R190T ROW O M 0404 659 2016 05 This Page Intentionally Left Blank...
Page 57: ...56 RT 60 R160T R190T ROW O M 0404 659 2016 05 This Page Intentionally Left Blank...
Page 61: ...60 RT 60 R160T R190T ROW O M 0404 659 2016 05 This Page Intentionally Left Blank...
Page 63: ...62 RT 60 R160T R190T ROW O M 0404 659 2016 05 This Page Intentionally Left Blank...
Page 85: ......