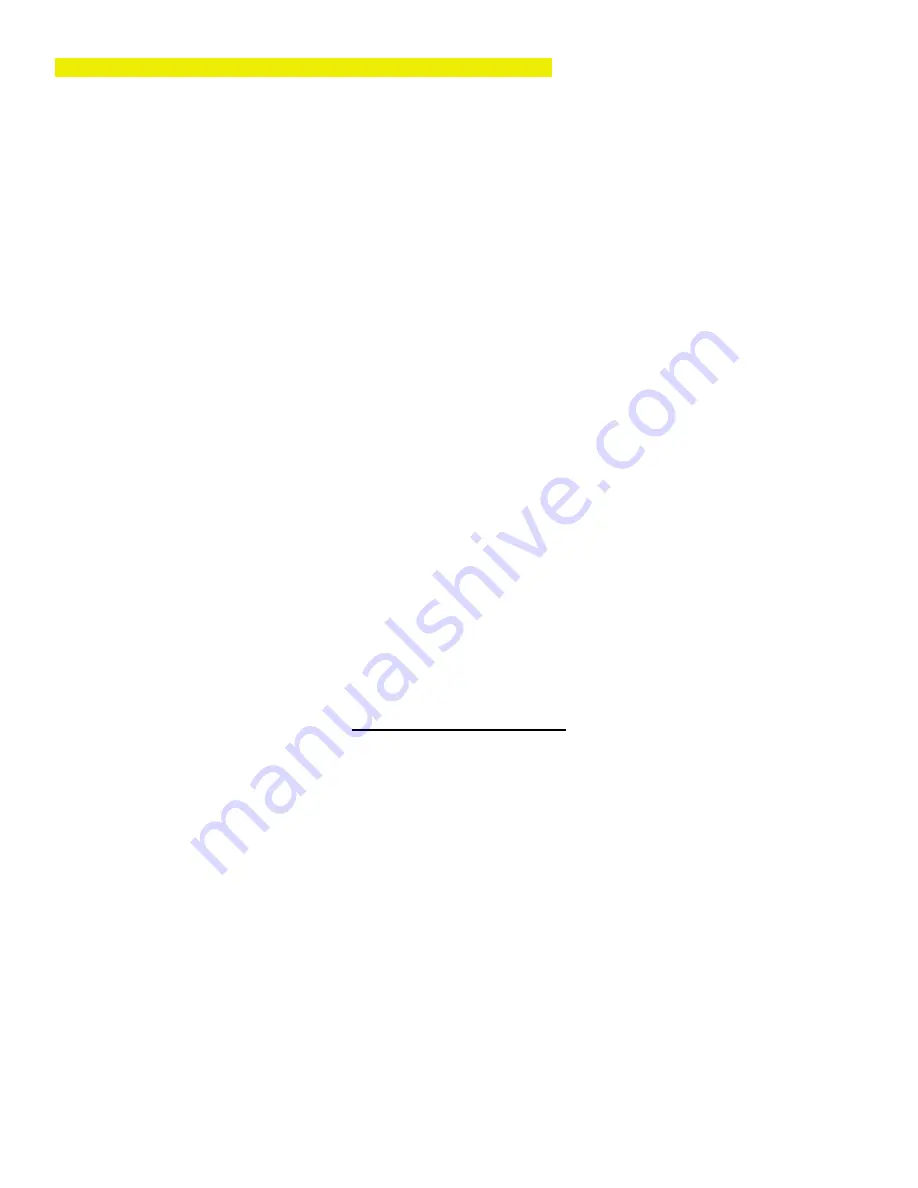
Tennsmith Inc. / 6926 Smithville Hwy. / McMinnville, TN 37110 / 931-934-2211 / Fax 931-934-2220
www.tennsmith.com
6
HEMMING:
Note: Forming hems is a secondary operation for a hand brake.
If you adjust the brake to close a hem in
the center of the work piece, the brake most likely will not bend straight. A hem is formed by making an acute
(reverse) bend in the work piece and then clamping the bent flange in the hold down (1) to press the flange
closed (to 180 degrees). Often the hem will not fully close in the center of a long work piece due to fact that the
outer ends of the brake are more rigid than the center. Here it is especially important that the brake is
sufficiently crowned and that there is proper clamping pressure at the center of the brake. Also the situation
can be improved by inserting a strip of material (of the same thickness as the work piece) between the work
piece and the clamp block slightly longer than the open portion of the hem. Re-clamp the hold down to close
the hem. A tinner’s mallet or hammer is also useful for closing hems. Be cautious not to use excessive force on
the clamp handles to close the hem.
OVERBENDING
:
The hold down assembly should be moved back on the end where the over bending occurs
by slightly unclamping the clamp handles, loosening the set screw and turning the eccentric pin. When the
correction is made retighten the set screw.
U48-22 BOX AND PAN BENDING:
The fingers can be removed and repositioned on the hold down
assembly by moving the clamp handle fully to the rear and loosening the finger clamp screws. Reposition the
fingers to assemble the desired width and secure the fingers to the hold down by tightening the finger clamp
screws. Be certain that the tops of the fingers are flush and parallel with the milled edge on the hold down and
the finger clamps are parallel with the bottom edge of the hold down. As a general rule, use the wider finger
first and fill in with the narrower fingers. Small gaps between the fingers may be left with no adverse effect to
the work piece. The maximum depth of box or pan which can be bent is 3-Inches.
ADJUSTING THE BRAKE
Your brake when assembled at the factory was adjusted for proper operation. Due to handling and
repositioning, the brake my require adjustment and alignment. Read the adjustment and operating instructions
completely before making any adjustments. Operate the brake and bend some material first before attempting
any major adjustments.
BASIC ALIGNMENT:
The clamp block on the base of the brake should be straight. This is the reference
point for all of the other alignment operations in adjusting the brake. Raise or lower the center of the brake by
adjusting the center of the brake by adjusting the center truss rod.
NOTE:
The U48 has four truss rods that
serve as the adjustments of the primary components. The S48 is equipped with three truss rods which facilitate
adjustment of the brake’s three primary weldments. Adjustments are accomplished through rotation of the nut
located on the studs mounted perpendicular to the weldments. The U48 comes with an additional brace which
serves to correct the alignment of the center fingers of the brake with respect to the ends. This adjustment is
made by turning the nut located on the right hand side of the hold down assembly.
ShopRPMachinne