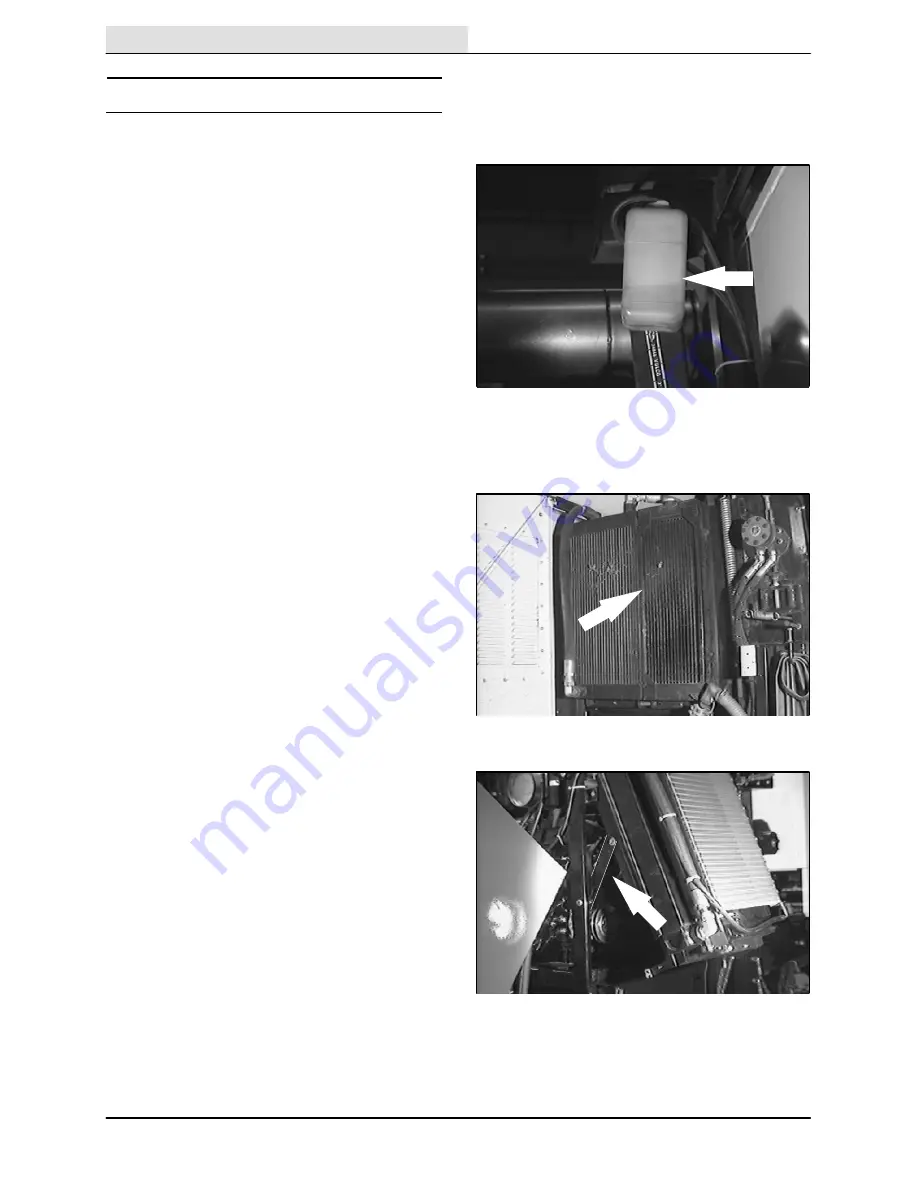
MAINTENANCE
830 MM332 (3--96)
72
ENGINE
COOLING SYSTEM
Check the radiator coolant level daily in the
overflow reservoir. Use clean water mixed with a
permanent-type, ethylene glycol antifreeze to a
--34
_
C (--30
_
F) rating. Add coolant to the
overflow reservoir.
FOR SAFETY: When Servicing Machine,
Avoid Contact With Hot Engine Coolant.
Check the radiator hoses and clamps every
200 hours of operation. Tighten the clamps if they
are loose. Replace the hoses and clamps if the
hoses are cracked, harden, or swollen.
Check the radiator core exterior and hydraulic
cooler fins for debris daily. The hydraulic cooler
blocker (if used) must be removed to clean the
hydraulic cooler fins. Blow or rinse all dust, which
may have collected on the radiator, in through the
grille and radiator fins, opposite the direction of
normal air flow. Be careful not to bend the cooling
fins when cleaning. Clean thoroughly to prevent
the fins becoming encrusted with dust. Clean the
radiator and cooler only after the radiator has
cooled to avoid cracking.
FOR SAFETY: When Servicing Machine,
Wear Eye And Ear Protection When
Using Pressurized Air Or Water.
Flush the radiator and the cooling system every
1600 hours of operation, using a dependable
cleaning compound.
The radiator and hydraulic cooler assembly pivots
forward for cleaning or for accessing the front of
the engine. To pivot forward, unscrew the bottom
two bolts, pull the assembly forward and engage
the locking latch.