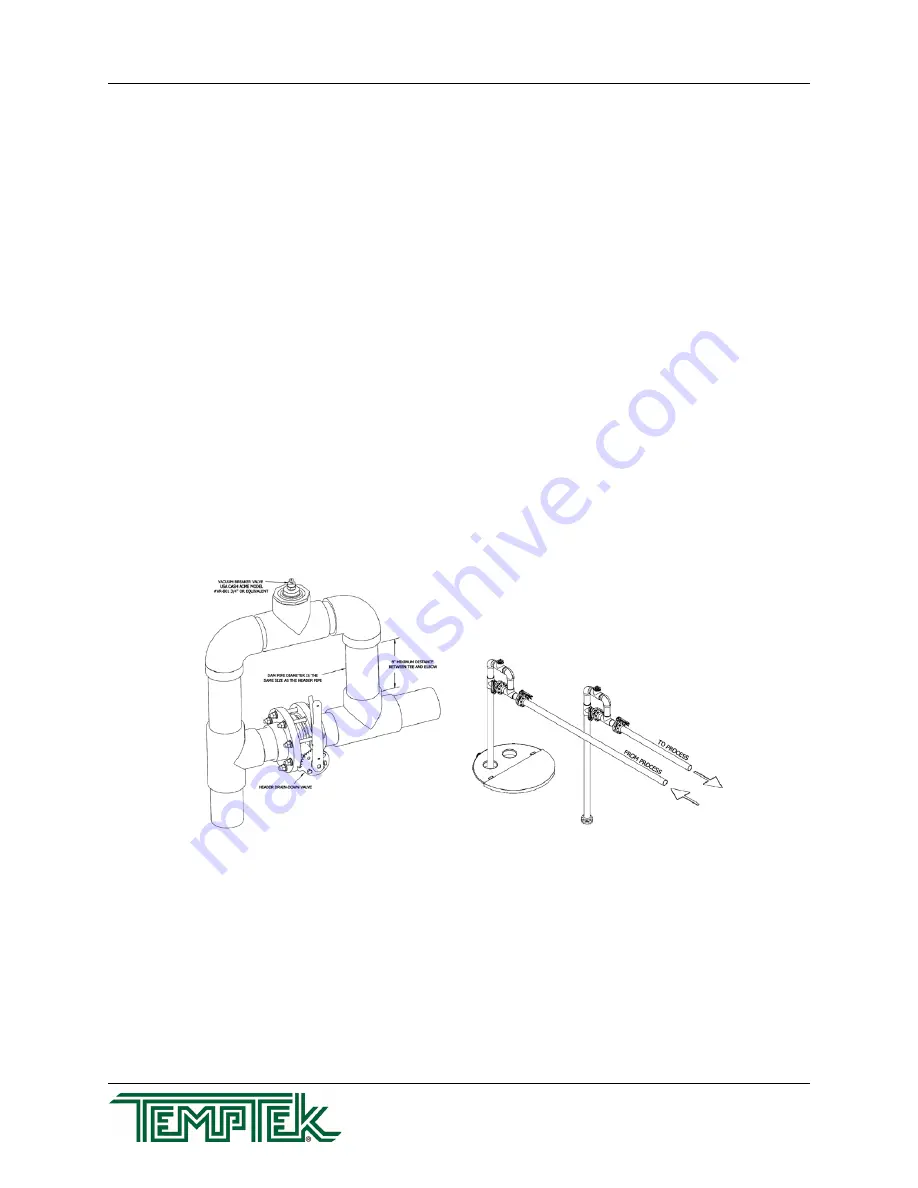
Page: 9
TEMPTEK, INC.
525 East Stop 18 Road Greenwood, Indiana 46142
317-887-6352 Fax: 317-881-1277
Email: [email protected]
PTK Series Polyethylene Pump Tank Station with Checkmate Control System
efficiently. Fouling can lead to a loss of plant performance.
C.
The Manufacturer assumes no responsibility for equipment failures or other results from
untreated or improperly treated water.
D. Legionella. Cooling towers must be treated for and protected from Legionella. Follow
ASHRAE Standard 188P and/or CTI Guidelines WTB-14B, and /or OSHA Guidelines
Section III Chapter 7 and/or the recommendation of your professional water treatment
expert to prevent Legionella in your tower. Failure to prevent Legionella may result in
sickness or death.
2.5
VACUUM BREAKERS
A.
Vacuum breakers are required in all systems where overhead piping is used. Vacuum
breakers keep the main header system full of fluid and prevent tank overflow during shut
down periods.
B.
The purpose of the vacuum breaker/anti-siphon (also called a drain-back dam) is to retain
water in the header system during shut-down periods and to allow for air purge which
eliminates shock to plumbing during start-up.
C.
It is necessary to install vacuum breakers in the ‘supply’ and ‘return’ lines. The vacuum
breaker must be installed at the highest point in the system, nearest to the tanks to
be most effective. A nipple length of 8 inches minimum is required to create sufficient
vacuum to open the Cash Acme model VR-801.
2.6
PROCESS CONNECTIONS
A.
Connect equipment process pump discharge port to main header supply line.
B.
Connect equipment chiller or tower pump discharge port to chiller to tower cell inlet.
C.
Install return line from the chiller or tower cell into the back 1/3 section of the cold tank
through the provide opening. Return line from tower is gravity induced flow and sloping of
this pipe is critical to proper flow rates (minimum 10% slope).
Typical Vacuum Breaker System