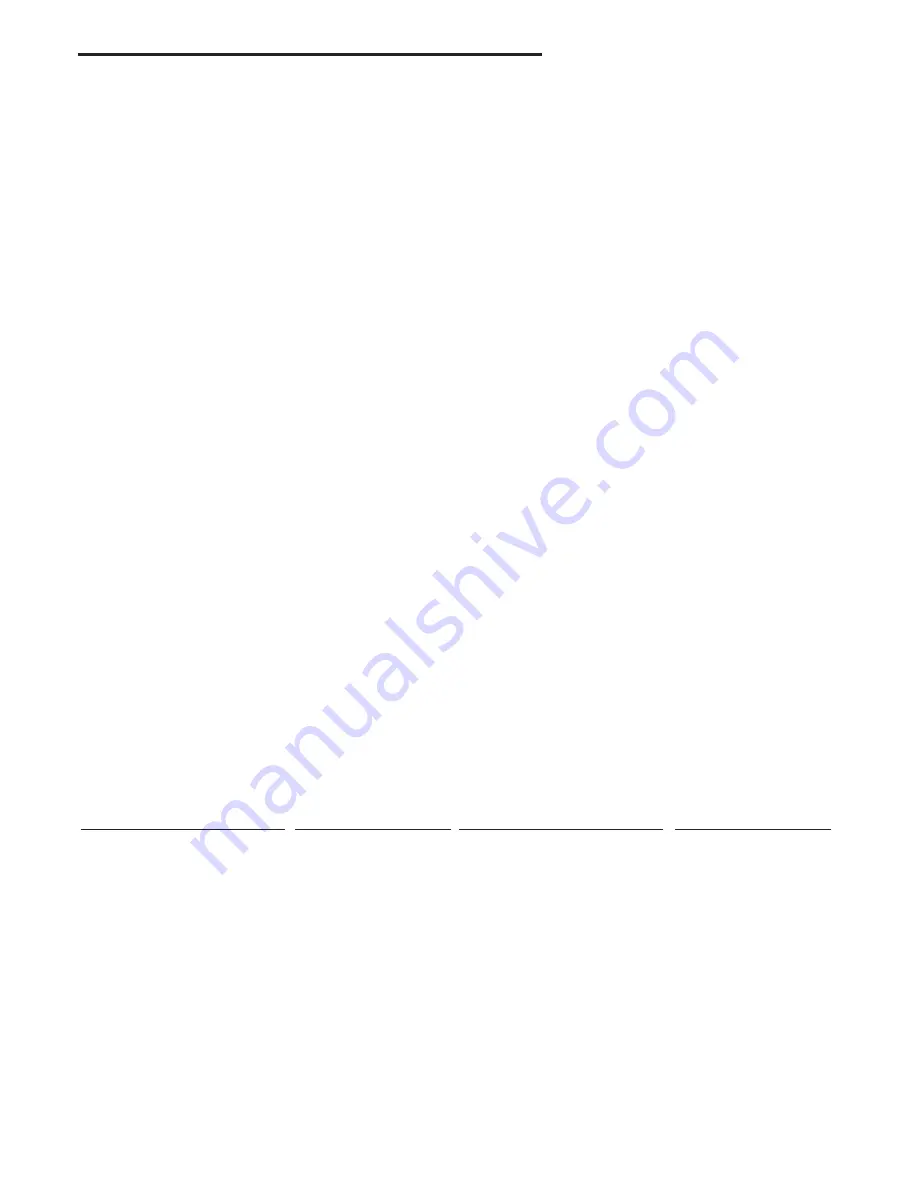
49
41DVN / DVSN Direct Vent Gas Fireplace
20009999
TEMCO FIREPLACE PRODUCTS DIRECT VENT FIREPLACES
INSTALLATION AND STARTUP CHECKLIST
Customer Copy
NOTE: TEMCO Fireplace Products
gas logs and fireplaces require installation by a qualified gas appliance installer.
A copy of this checklist must be submitted, along with proof of purchase, when applying to Technical Services for prior
written approval of warranty repair or replacement.
❑
Read and understand installation instructions before attempting installation.
Verify CORRECT FUEL TYPE
❑
Check carton model number.
❑
Check fireplace label. Models ending in N are for natural gas; those ending in P are for propane (LP gas).
WARNING: Using the incorrect fuel can create a serious fire hazard and will void the warranties. Install in
accordance with local and/or natonal codes and ordinances. Follow the TEMCO installation instruc-
tions.
❑
Supply service shutoff valve upstream of gas fireplace.
❑
Gas line size adequate for input rating (BTU’s per hour) of fireplace, per National Fuel Gas Code (NFPA54)
in the case of USA installations or Installation Code CAN 1-149 in the case of Canadian installations.
Make following checks:
❑
Gas line integrity at supply line connection.
❑
Glass front panel position.
❑
Correct gas pressure. Inlet Pressure __________(inches w.c.) Manifold Pressure __________(inchesw.c.)
❑
Piezo ignitor function (millivolt control models only).
❑
Pilot ignition.
❑
Main burner ignition.
❑
Proper flame pattern and color.
❑
Positioning of logs (in accordance with instructions).
❑
Clearances to combustibles (vent, framing, mantels, etc.).
❑
Vent system in compliance with instructions. All joints and connections sealed.
❑
Wall switch operation. Do not connect millivolt wiring, wall switch or valve to 120v line voltage unless units is
specifically DSI equipped.
❑
Demonstrated proper operating procedure to homeowner.
❑
Explained the need for proper cleaning and maintenance.
❑
Check all fittings and connections for gas leaks, correct if necessary.
Please sign below that checklist has been completed and understood. DATE INSTALLED ____/____/____
Installer Phone Consumer Phone