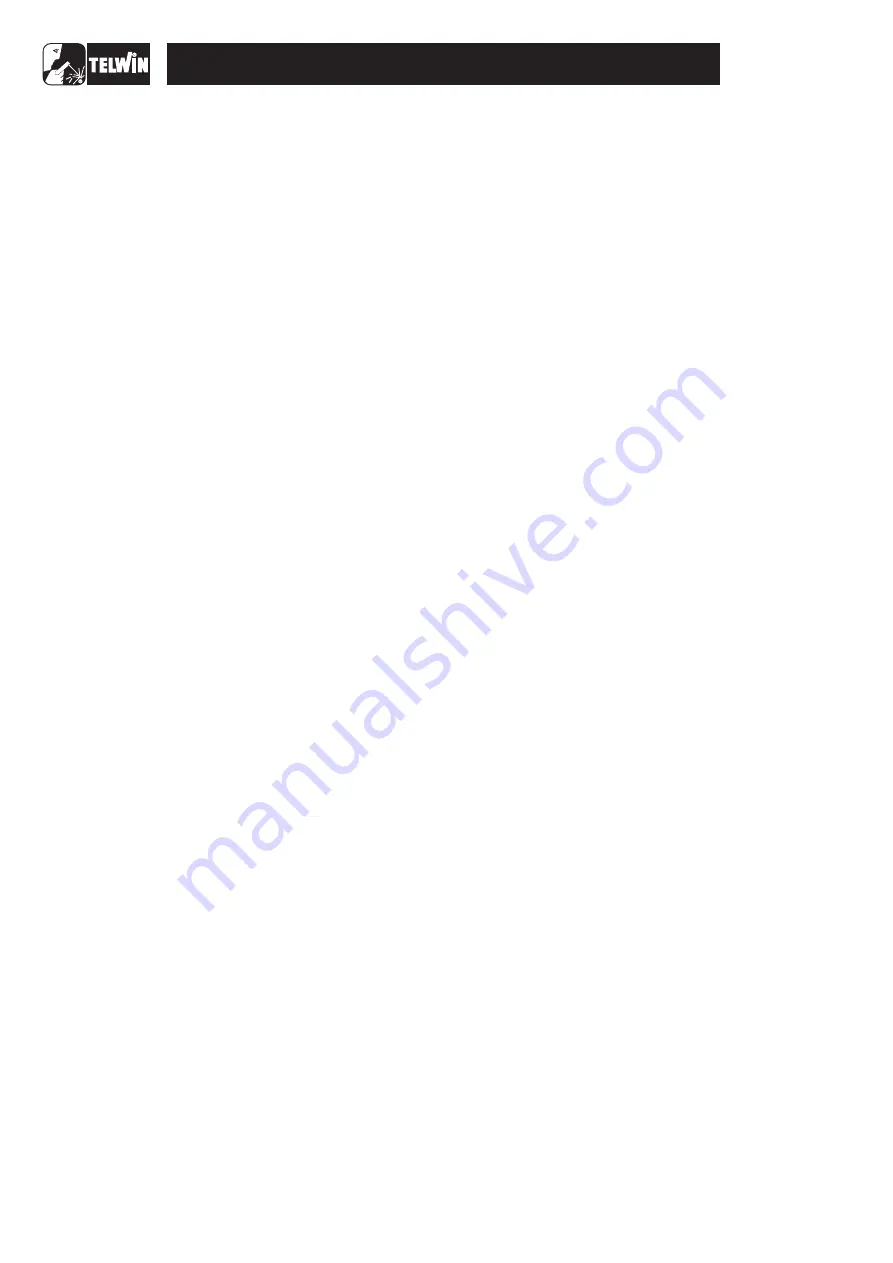
instructions.
-
Prepare the components for replacement. For the IGBT's,
bend the rheofores at 90 (never bend and/or place the parts
under tension near the case).
-
Position the components on the dissipator with the fastening
screws, but do not tighten the screws completely
-
Join the dissipator/component assembly to the printed board,
inserting all the rheofores in the bump contacts and the
threaded spacers on the 4 attachment holes.
-
Attach the dissipators with the nuts and lock them once and for
all in the following order:
- the nuts fastening the dissipators to the printed circuit with a
torque wrench setting of 2 Nm ±20%;
- the screws fastening the rectifiers to the dissipators with a
torque wrench setting of 2 Nm ±20%;
- the screws fastening the IGBT's to the dissipators with a
torque wrench setting of 1 Nm ±20%.
- Solder the terminals taking care not to let the solder run along
them.
- On the component side cut away the protruding part of the
rheofores and check they are not shorted (especially the gate
and emitter).
The 4 IGBT's should belong to the same selection kit
supplied by Telwin.
If the fault is in the secondary board, it should be specified that to
remove it, it is necessary to separate the base from the machine
structure as follows:
- with the machine disconnected from the main power supply
and after removing the control and primary boards, separate
the base from the machine structure by undoing the 4 screws;
- disconnect all wiring connected to the secondary board;
- undo the 4 screws fastening the dissipator to the machine
structure;
- extract the secondary board from the machine structure;
for assembly proceed in the reverse order.
The 10 secondary DIODES are attached to the dissipator and to
reach them it is necessary to remove the boards above and below.
Whenever one diode is replaced, they should all be replaced.
- undo the 3 screws fastening the SCR module to the top board;
- disconnect the 4 fastons connected to the SCR module;
- undo the 2 screws fastening the aluminium connections to the
bottom board;
- remove the top board;
- undo the 4 nuts fastening the bottom board to the dissipator;
- undo the 10 screws attaching the diodes to the dissipater;
- remove the 10 diodes by unsoldering the rheofores and also
remove the solder from the bump contacts on the PCB;
- clean any irregularities or dirt from the dissipators. If the diodes
have burst the dissipator may be irreparably damaged: in such
a case it should be replaced;
- apply thermoconductive paste following the general
instructions;
for diodes D6, D7, D8, D9 and D10
remember to insert nomex insulation between the dissipator
and the diode.
- place the dissipator with the new components on the bump
contacts of the PCB and fasten it down with the screws (torque
wrench setting 1 Nm 20%);
- solder the terminals taking care not to let the solder run along
them;
- on the soldering side cut the protruding part of the rheofores
and make sure they have not shorted (between cathode and
anode).
make sure that resistors R1, R2, R3, R4 and capacitors C1,
C2, C3, C4 on the snubber are soldered correctly to the bottom
board.
The SCR module is attached to the dissipator and to reach it, it is
necessary to remove the top board:
- undo the 3 screws fastening the SCR module to the top board;
- disconnect the 4 fastons connected to the SCR module;
- remove the top board;
- remove the SCR module by undoing the 2 screws at the side;
- clean any irregularities or dirt from the dissipators. If the SCR
module has blown the dissipator may be irreparably damaged:
in such a case it should be replaced;
-
apply thermoconductive paste following the general
instructions;
-
place the new SCR module on the dissipator and fasten it with
the screws (torque wrench setting 5 Nm 20%);
make sure that resistors R1, R6, diodes D22, D5 and
capacitors C1, C5 on the snubber are soldered correctly to the top
board.
Tests should be carried out on the assembled machine before
closing it with the top cover. During tests with the machine in
operation never commute the selectors or activate the ohmic load
contactor.
Before proceeding to test the machine, we should
remind you that during these tests the power source is powered
and therefore the operator is exposed to the danger of electric
shock.
The tests given below are used to verify power source operation
under load.
A) Do not connect the gas mixture source.
B) Connect the machine to the static load generator (code
802110) using cables fitted with the appropriate dinse
connectors (802110)
C) Set up the dual trace oscilloscope with the voltage probe
CH1x100 connected between the collector (probe) and the
emitter of Q4 (earth) on the primary board (
).
D) Pass the current probe of the Hall effect transducer along the
cable connecting the power transformer at faston CN10 with
the reference arrow pointing into CN10.
E) Lastly, connect the Hall Probe and the current probe to the
oscilloscope.
F) Set up a multimeter in DC volt mode and connect the prods to
the OUT+ and OUT- dinse connections.
G) On the front panel set switch SW2 to MMA (as low as it will go)
and switch SW3 to DC-LIFT (in the centre).
H) Keep fastons J1 and J3 disconnected from the HF board (fig.
3).
the high frequency voltage will permanently damage
any instrument connected to the generator. Before proceeding
make very sure that the fastons listed above are disconnected and
completely isolated from one another.
I)
Connect the power supply cable to the 230Vac power supply.
during testing prevent contact with the metal part of
the torch because of the presence of high voltages that are
hazardous to the operator.
Switch on the machine, gradually increase the power supply
voltage from 0V to 230Vac and make sure that:
-
the pre-charge relays on the primary board close;
-
the fan starts operating correctly;
-
the green power supply LED D6 lights up;
-
the waveform displayed on the oscilloscope resembles
and the frequency is equal to +60KHz ±5%; if the frequency
°
NOTE.
N.B.
Take special note of the procedure for replacing the
secondary diodes (fig. 6):
Warning!
N.B.
Please take careful note of the procedure for replacing the
SCR module (fig. 6):
N.B.
WARNING!
fig. 5
WARNING!
WARNING!
A)
Loadless test:
Fig. F
7.3 Removing the secondary board (fig. 6)
TESTING THE MACHINE
1.1 Preparation for testing
1.2 Scheduled tests
- 18 -
TECHNOLOGY TIG 172 AC/DC