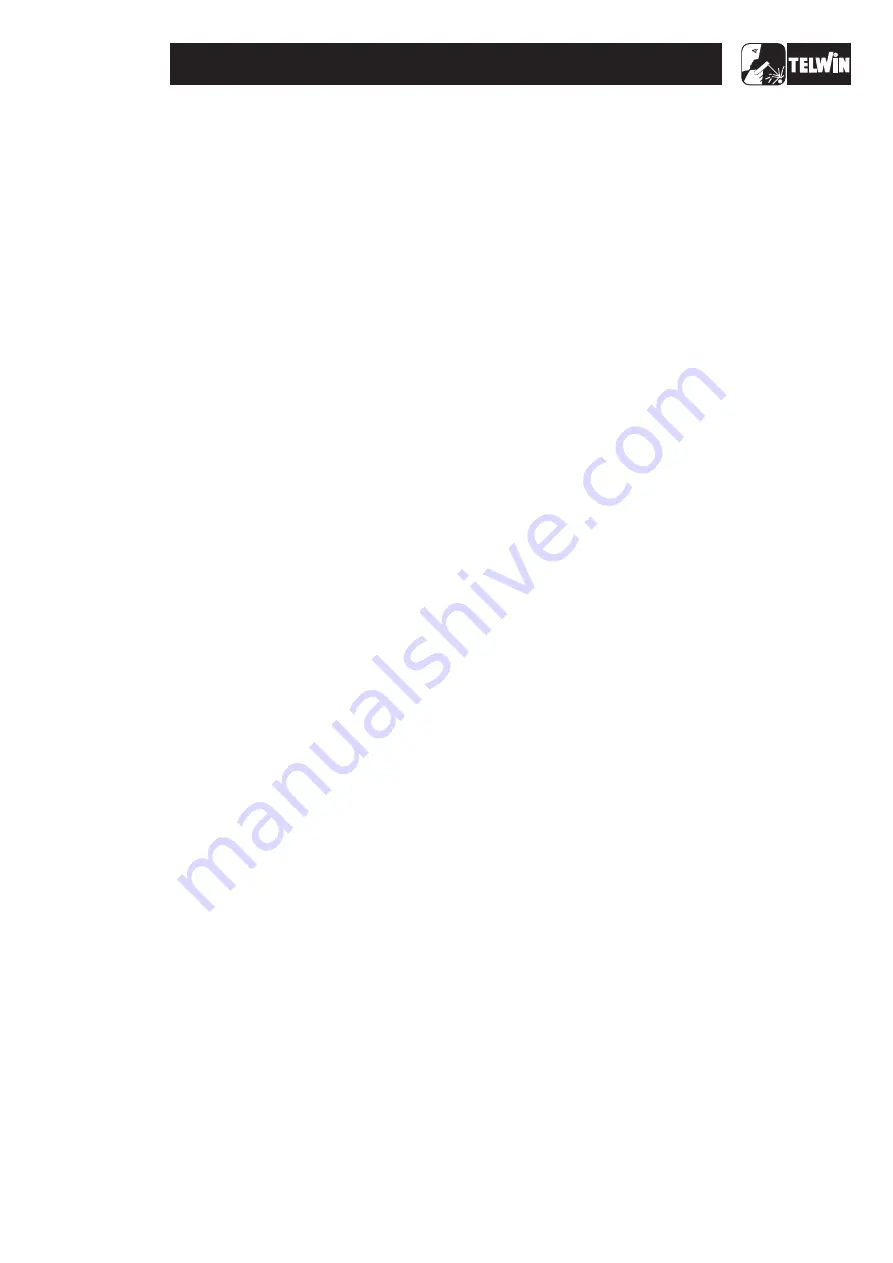
It is therefore important to take special care when cleaning the
following parts
Check whether dirt has been deposited on the front and back air
vents or has damaged the correct rotation of the blades, if there is
still damage after cleaning replace the fan.
Make sure there is no mechanical deformation, dent, or damaged
and/or disconnected connector.
Make sure the power supply cable has not been damaged or
disconnected internally and that the fan works with the machine
switched on. Inspect the components and cables for signs of
burning or breaks that may endanger operation of the power
source. Check the following elements:
Use the multimeter to check whether the contacts are stuck
together or open. Probable cause:
-
mechanical or electric shock (e.g. bridge rectifier or IGBT in
short circuit, handling under load).
Probable cause:
-
see main power supply switch.
If the relay contacts are
stuck together or dirty, do not attempt to separate them and
clean them, just replace the relay.
Probable cause:
-
mechanical shock;
-
machine connected to power supply voltage much higher than
the rated value;
-
broken rheophore on one or more capacitor: the remainder will
be overstressed and become damaged by overheating;
-
ageing after a considerable number of working hours;
-
overheating caused by thermostatic capsule failure.
Probable cause:
-
discontinuation in snubber network,
-
fault in driver circuit
-
poorly functioning thermal contact between IGBT and
dissipator (e.g. loosened attachment screws: check),
-
excessive overheating related to faulty operation
Probable cause:
-
excessive overheating related to faulty operation.
Probable cause:
- mechanical shock.
Probable cause:
-
discontinuation in snubber network;
-
poorly functioning thermal contact between IGBT and
dissipator (e.g. loosened attachment screws: check);
-
faulty output connection.
Probable cause:
see the main power supply switch;
If the relay contacts are
stuck together or dirty, do not attempt to separate or clean them,
just replace the relay.
Check it for colour changes.
Probable cause:
overheating due to loosening of the screws connecting the shunt
to the PCB.
Probable cause:
see the main power supply switch;
If the relay contacts are
stuck together or dirty, do not attempt to separate or clean them,
just replace the relay.
Make sure the fuse is correctly inserted into the fuse holder and
that it has not blown (blackened in colour). Use the multimeter to
check whether the fuses have blown. Probable cause:
excessive current absorption from the main supply.
Inspect the windings for colour changes.
Probable causes:
- aging after a substantial number of working hours;
- excessive overheating related to faulty operation.
Inspect the windings for colour changes. Probable causes:
- aging after a substantial number of working hours;
- excessive overheating related to faulty operation.
Check it for colour changes. Probable cause:
- overheating due to loosening of the screws connecting the
shunt to the PCB.
Check the solenoid valve to see if it opens. Probable causes:
- the solenoid valve does not open because of a mechanical
block; do not attempt to open the valve but used compressed air to
carry out thorough cleaning or replace the solenoid valve.
Maintenance status, referring to the instructions given in the
instruction manual. Condition of parts not subject to wear on the
connecting cable between torch and power source (insulation).
It is important to check that all the connections are in good
condition and the connectors are inserted and/or attached
correctly. To do this, take the cables between finger and thumb (as
close as possible to the fastons or connectors) and pull outwards
gently: the cables should not come away from the fastons or
connectors. N.B. If the power cables are not tight enough this
could cause dangerous overheating.
Fan fig. 2A
Main power supply switch fig. 2A
Relays K1, K2 primary board fig. 5
Electrolytic capacitors C2,C4,C6,C7 primary board fig. 5
IGBT's Q1, Q2, Q3, Q4 primary board fig. 5
Primary diodes D1, D4, D6, D8 primary board fig. 5
Mode selector switches SW2 and SW3 panel board (fig. 2A)
Secondary diodes D1...D10 secondary board fig. 2A
Relay K2 secondary board (fig. 6)
Shunt R2 secondary board (fig. 6)
Relay K1 torch button board (fig. 4)
Fuse F1 torch button board (fig. 4)
Power transformer and filter inductance (fig. 2A)
HF transformer (fig. 2A)
Shunt (fig. 2A)
Solenoid valve (fig. 3)
TIG Torch
(
)
(
)
(
)
(
)
(
)
.
(
)
(
)
Primary board (fig. 5:)
Secondary board (fig. 6):
Power transformer and inductance assembly (fig. 2A)
Parts fastened to the base (fig. 4)
5.0 Electrical measurements with the machine switched off
-
-
-
-
-
-
-
-
-
fig. 5
fig. 5
fig. 6
fig. 6
fig. 5
fig. 5
fig. 6
rheofores of IGBT's Q1, Q2, Q3, Q4;
rheofores of recirculating diodes D4, D8;
rheofores of snubber network diodes D1, D6;
rheofores of opto-couplers ISO1 and ISO2;
rheofores of connectors J4 and J6;
rheofores of secondary power diodes D1…D10;
bump contacts on top of and under the printed circuit of the
SCR Q5 module;
thermostat ST1 on secondary diode dissipator;
rheofores of opto-couplers ISO1, ISO2, ISO3, ISO4;
Do this if it is necessary to remove the primary board, otherwise it
is possible to clean the part superficially from the side of the
secondary board.
If the primary and secondary boards are removed (with the
diaphragm), carefully clean all the parts fastened to the base, or
clean the base partially from the sides of the machine.
A) With the multimeter set on diode testing check the following
components (joint voltages not less than 0.2V):
-
rectifier bridges D3, D5 (
);
-
IGBT's Q1, Q2, Q3, Q4, (no short circuits between collector-
gate and collector-emitter (
));
-
secondary diodes D1…D10 between anode and cathode
(
). SCR Q5 module (no short circuits between anode
and cathode
).
B)
With the multimeter in ohm mode check the following
components:
-
resistor R1: 47 ohm (pre-charge
).
-
resistors R2, R6: 10 ohm (primary snubber
).
-
resistors R1, R2, R3, R4: 10 ohm (secondary snubber
).
-
thermostat continuity test on inductance: disconnect fastons
3.0 Visual inspection of the machine
4.0 Checking the power and signal wiring
N.B.
-
N.B.
-
-
N.B.
-
- 15 -
TECHNOLOGY TIG 172 AC/DC