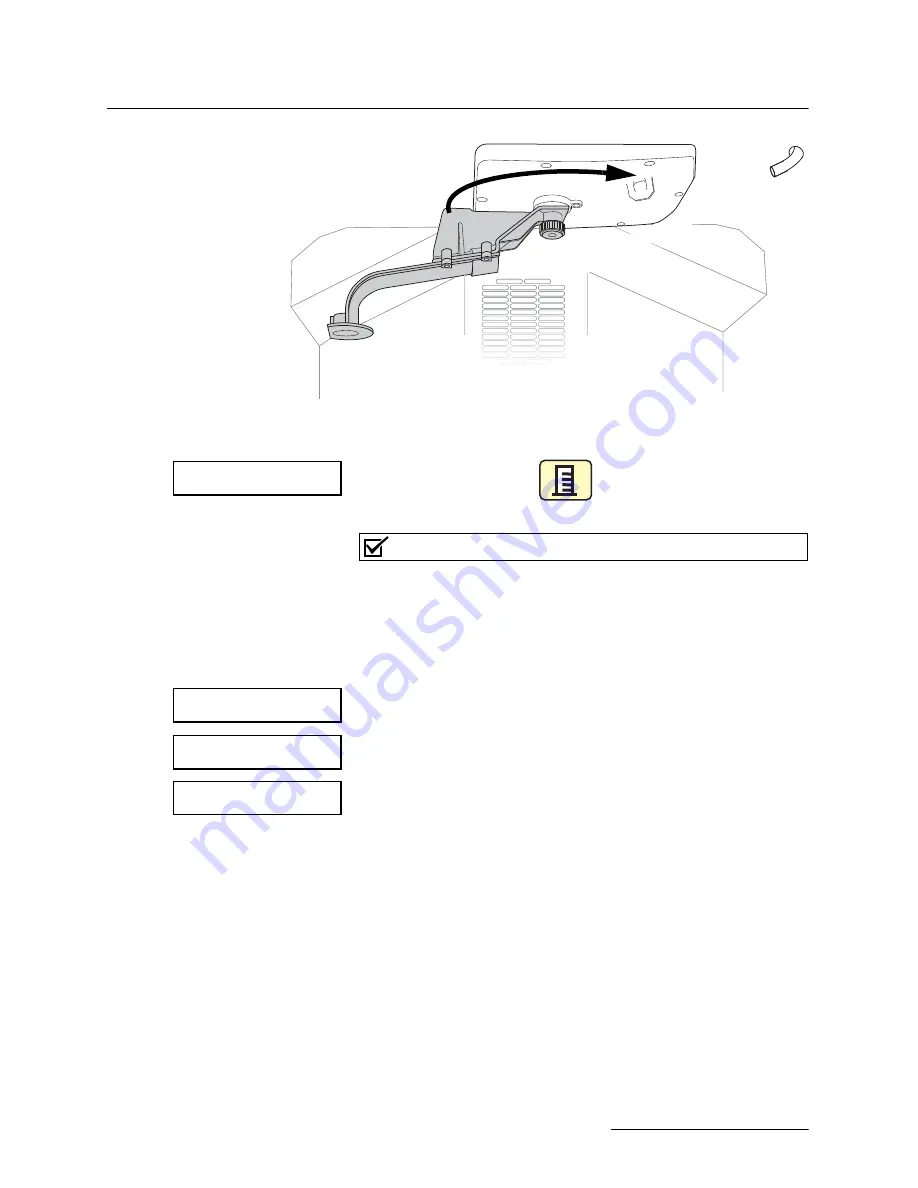
4700 Refrigerated Sampler Service Guide
Section 5 Electrical Troubleshooting and Diagnostics
5-5
Figure 5-2 Distributor arm positioning, discharge tube removed
5. Press the Calibrate
button. This saves the current
distributor arm position as “home.”
Note
The arm must be at the stop when the Calibrate button is
pressed. The calibrate function always saves the arm’s current
position as "home."
6. Enter the bottle number to which the sampler should move
the arm. Press Enter and the distributor will run.
7. The sampler reports the new distributor arm position. Ver-
ify that the arm is aligned over the correct bottle.
8. The sampler then asks for the next bottle position. Enter a
bottle number and press Enter, or press the Stop button to
exit the test.
9. From the standby screen, reenter the code
82253
(TABLE)
to exit Calibrate mode. It is important to exit Calibrate
mode prior to operation to avoid errors during the running
of a program.
If the sampler displays
DISTRIBUTOR JAMMED
,
DISTRIBUTOR
ERROR
,
SLOT CODE ERROR
,
DISK ERROR
, or
BELT TOO
LOOSE
, verify that the arm movement is not obstructed. Clear
any obstructions such as bottles not fully seated in the rack or an
incorrectly installed discharge tube, then perform the
TEST DIS-
TRIBUTOR
diagnostic again from step 1. If you don’t find obstruc-
tions to the distributor arm movement, contact your authorized
Isco service facility or the Teledyne Isco factory.
GO TO BOTTLE ___
(1-max)
MOVING TO BOTTLE ___
NOW AT BOTTLE ___
GO TO BOTTLE ___
(1-max)
Summary of Contents for 4700
Page 2: ......
Page 6: ...Isco 4700 Refrigerated Sampler Service Guide Safety iv ...
Page 12: ...4700 Refrigerated Sampler Service Guide Table of Contents x ...
Page 30: ...4700 Refrigerated Sampler Service Guide Section 1 Introduction and General Guidelines 1 18 ...
Page 60: ...4700 Refrigerated Sampler Service Guide Section 2 Sample Delivery System 2 30 ...
Page 108: ...4700 Refrigerated Sampler Service Guide Section 4 CPU and Power Supply 4 26 ...
Page 124: ...4700 Refrigerated Sampler Service Guide Appendix A Electrical Diagrams A 2 ...
Page 126: ...4700 Refrigerated Sampler Electrical Wiring A 4 Figure A 3 4700 wiring diagram 230V ...
Page 128: ...4700 Refrigerated Sampler Electrical Wiring A 6 Figure A 5 4700 CPU schematic diagram ...
Page 131: ...4700 Refrigerated Sampler Appendix B Replacement Parts List B 3 ...
Page 132: ...4700 Refrigerated Sampler Appendix B Replacement Parts List B 4 ...
Page 133: ...4700 Refrigerated Sampler Appendix B Replacement Parts List B 5 ...
Page 134: ...4700 Refrigerated Sampler Appendix B Replacement Parts List B 6 ...
Page 135: ...4700 Refrigerated Sampler Appendix B Replacement Parts List B 7 ...
Page 136: ...4700 Refrigerated Sampler Appendix B Replacement Parts List B 8 ...
Page 137: ...4700 Refrigerated Sampler Appendix B Replacement Parts List B 9 ...
Page 138: ...4700 Refrigerated Sampler Appendix B Replacement Parts List B 10 ...
Page 139: ...4700 Refrigerated Sampler Appendix B Replacement Parts List B 11 ...
Page 140: ...4700 Refrigerated Sampler Appendix B Replacement Parts List B 12 ...
Page 141: ...4700 Refrigerated Sampler Appendix B Replacement Parts List B 13 ...
Page 142: ...4700 Refrigerated Sampler Appendix B Replacement Parts List B 14 ...
Page 143: ...4700 Refrigerated Sampler Appendix B Replacement Parts List B 15 ...
Page 144: ...4700 Refrigerated Sampler Appendix B Replacement Parts List B 16 ...
Page 145: ...4700 Refrigerated Sampler Appendix B Replacement Parts List B 17 ...
Page 146: ...4700 Refrigerated Sampler Appendix B Replacement Parts List B 18 ...
Page 147: ...4700 Refrigerated Sampler Appendix B Replacement Parts List B 19 ...
Page 148: ...4700 Refrigerated Sampler Appendix B Replacement Parts List B 20 ...
Page 149: ...4700 Refrigerated Sampler Appendix B Replacement Parts List B 21 ...
Page 150: ...4700 Refrigerated Sampler Appendix B Replacement Parts List B 22 ...
Page 151: ...4700 Refrigerated Sampler Appendix B Replacement Parts List B 23 ...
Page 152: ...4700 Refrigerated Sampler Appendix B Replacement Parts List B 24 ...
Page 153: ...4700 Refrigerated Sampler Appendix B Replacement Parts List B 25 ...
Page 154: ...4700 Refrigerated Sampler Appendix B Replacement Parts List B 26 ...
Page 155: ...4700 Refrigerated Sampler Appendix B Replacement Parts List B 27 ...
Page 156: ...4700 Refrigerated Sampler Appendix B Replacement Parts List B 28 ...
Page 157: ...4700 Refrigerated Sampler Appendix B Replacement Parts List B 29 ...
Page 158: ...4700 Refrigerated Sampler Appendix B Replacement Parts List B 30 ...
Page 159: ...4700 Refrigerated Sampler Appendix B Replacement Parts List B 31 ...
Page 161: ...4700 Refrigerated Sampler Appendix B Replacement Parts List B 33 ...
Page 162: ...4700 Refrigerated Sampler Appendix B Replacement Parts List B 34 ...
Page 163: ...4700 Refrigerated Sampler Appendix B Replacement Parts List B 35 ...
Page 164: ...4700 Refrigerated Sampler Appendix B Replacement Parts List B 36 ...
Page 165: ...4700 Refrigerated Sampler Appendix B Replacement Parts List B 37 ...
Page 166: ...4700 Refrigerated Sampler Appendix B Replacement Parts List B 38 ...
Page 167: ...4700 Refrigerated Sampler Appendix B Replacement Parts List B 39 ...
Page 168: ...4700 Refrigerated Sampler Appendix B Replacement Parts List B 40 ...
Page 169: ...4700 Refrigerated Sampler Appendix B Replacement Parts List B 41 ...
Page 170: ...4700 Refrigerated Sampler Appendix B Replacement Parts List B 42 ...
Page 171: ...4700 Refrigerated Sampler Appendix B Replacement Parts List B 43 ...
Page 172: ...4700 Refrigerated Sampler Appendix B Replacement Parts List B 44 ...