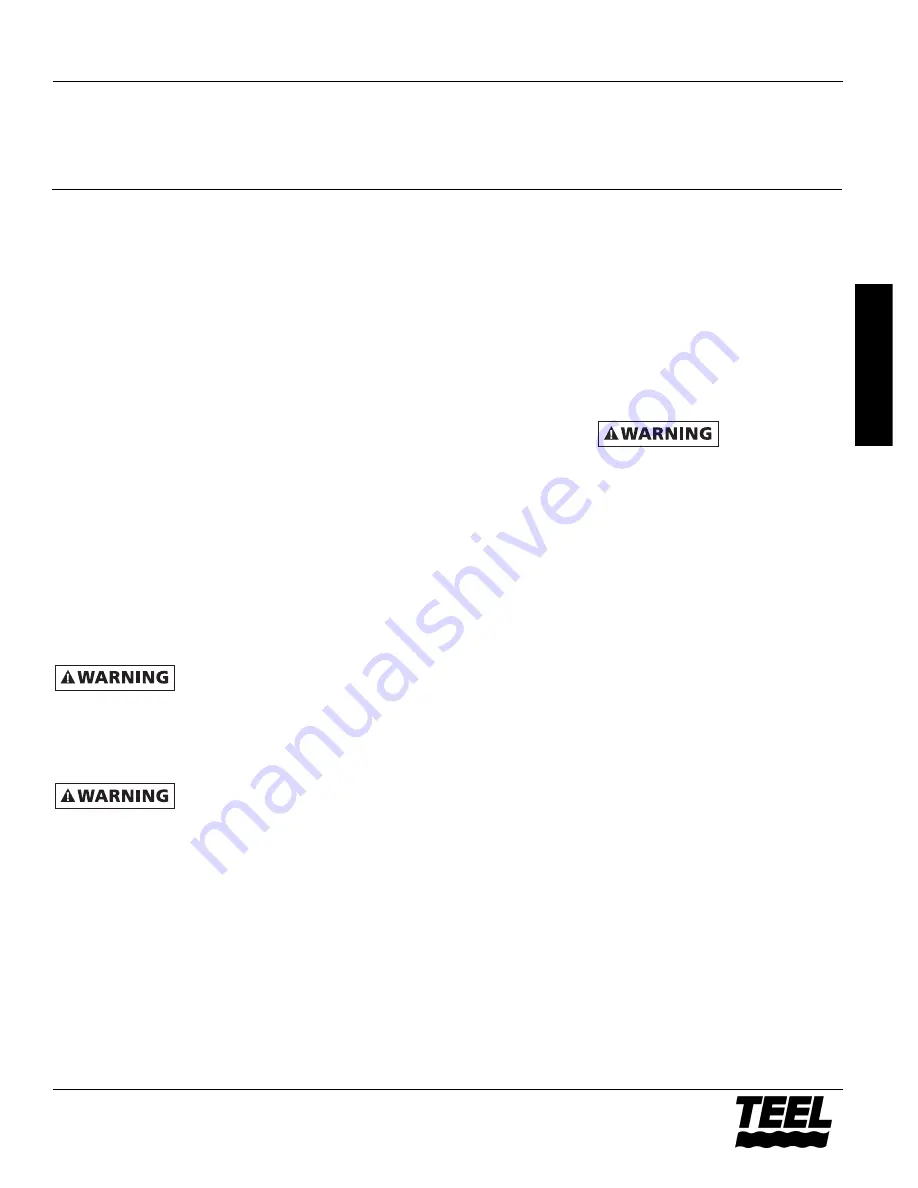
Installation (Continued)
In an
effluent
system, use a
2”
(51
mm) minimum check valve in pump
discharge to prevent backflow of
liquid into pump basin. The check
valve should be a free flow valve that
will easily pass solids. Be sure check
valve installation complies with local
codes.
NOTE:
Check valve must not be smaller
than pump discharge pipe.
NOTE:
For best performance of check
valve when handling solids, do not
install it with discharge more than 45°
above the horizontal. Do not install
check valve in a vertical position as
solids may settle in valve and prevent
opening on startup.
Drill a 3/16" (5 mm) hole in discharge
pipe about 1 to 2" (25-50 mm) above
pump discharge connection (but below
check valve) to prevent airlocking the
pump.
ELECTRICAL
Risk of electrical
shock and fire. Be
sure that power supply information
(Voltage/Hertz/Phase) on pump motor
nameplate matches incoming power
supply exactly. Install pump according to
all electrical codes that apply.
Hazardous voltage.
Can shock, burn, or
cause death. When installing, operating,
or servicing this pump, follow safety
instructions below.
DO NOT
splice the power cord,
submerge electrical cord plug, or use
extension cords.
DO NOT
handle or service pump while
it is connected to power supply.
DO NOT
operate pump unless it is
properly grounded. Wire pump
directly into grounded terminal block
in automatic float or pump controller
box. Power cord on 1-phase units is a
3-wire conductor with a 3-prong
grounding-type plug. Do not modify
cord or plug. When using with plug-in
receptacle, plug pump into a 3-wire,
grounded, grounding-type receptacle
only. Connect pump according to all
applicable codes.
Model 4RK62A has a piggy-back cord
and plug on the switch. Do not modify
cords or plugs. Plug the pump into the
switch plug and plug the switch plug
into a 3-wire, grounded, grounding-
type receptacle.
For automatic operation, plug or wire
pump into an automatic float switch or
pump controller. For continuous
operation, plug directly into an
electrical outlet or wire directly into
switch box. Connect pump to its own
individual branch circuit with nothing
else on the circuit.
For fuse/circuit breaker requirements
see “Specifications” on Page 1.
OVERLOADS – SINGLE PHASE
In single-phase units, an automatic
overload protector in the motor will
protect motor from burning out due
to overheating/overloading. When
motor cools down, protector
automatically resets and starts motor.
If overload trips frequently, check for
cause. It could be a stuck impeller,
wrong/low voltage, or electrical failure
in motor. If an electrical failure in the
motor is suspected, have it serviced by
a competent repairman.
NOTE:
Do not allow pump to run in a
dry sump. It will void the warranty and
may damage the pump.
CONTROL PANEL OVERLOAD
ADJUSTMENT – 3 PHASE
NOTE:
Control panel not provided
with pump. See control panel in-
stallation and operating instructions
before adjusting overload setting.
For pumps with a nameplate service
factor of 1.0, set overload protective
device to nameplate full load current.
For pumps with a nameplate service
factor of 1.15 or higher, set overload
protective device to 1.09 times the
nameplate full load current.
Size overload protective device so that
trip current is 115% of final setting as
selected above.
WIRING CONNECTIONS
Fire hazard.
Incorrect voltage
can cause a fire or seriously damage the
motor and voids the warranty. The
supply voltage must be within ±10% of
the motor nameplate voltage.
NOTE:
Model Numbers 4RK46A,
4RK48A and 4RK63A are factory wired
for 230 volts. If necessary, the motor
can be wired for 460 volts by
connecting the wires as indicated in
Table III, on Page 5. Do not alter the
wiring in single voltage motors. If in
doubt, consult a qualified electrician.
Install, ground, wire, and maintain
your pump in compliance with the
National Electrical Code (NEC) in the
U.S., or the Canadian Electrical Code
(CEC), as applicable, and with all local
codes and ordinances that apply.
Consult your local building inspector
for code information.
Model 4RK62A is equipped with an
automatic float switch which is factory
set with a 4” tether length. This tether
can be adjusted to accommodate a
variety of pumping ranges (See Table
II). The installer must ensure that the
switch does not become obstructed
and that the range is set so the liquid
level remains a minimum of 2” above
pump suction at the lowest level, and
below the basin inlet pipe at the
highest level.
Models 4RK45A, 4RK46A, 4RK47A,
4RK48A, 4RK49A, 4RK62A and 4RK63A
3
Teel Operating Instructions and Parts Manual
E
N
G
L
I
S
H
®