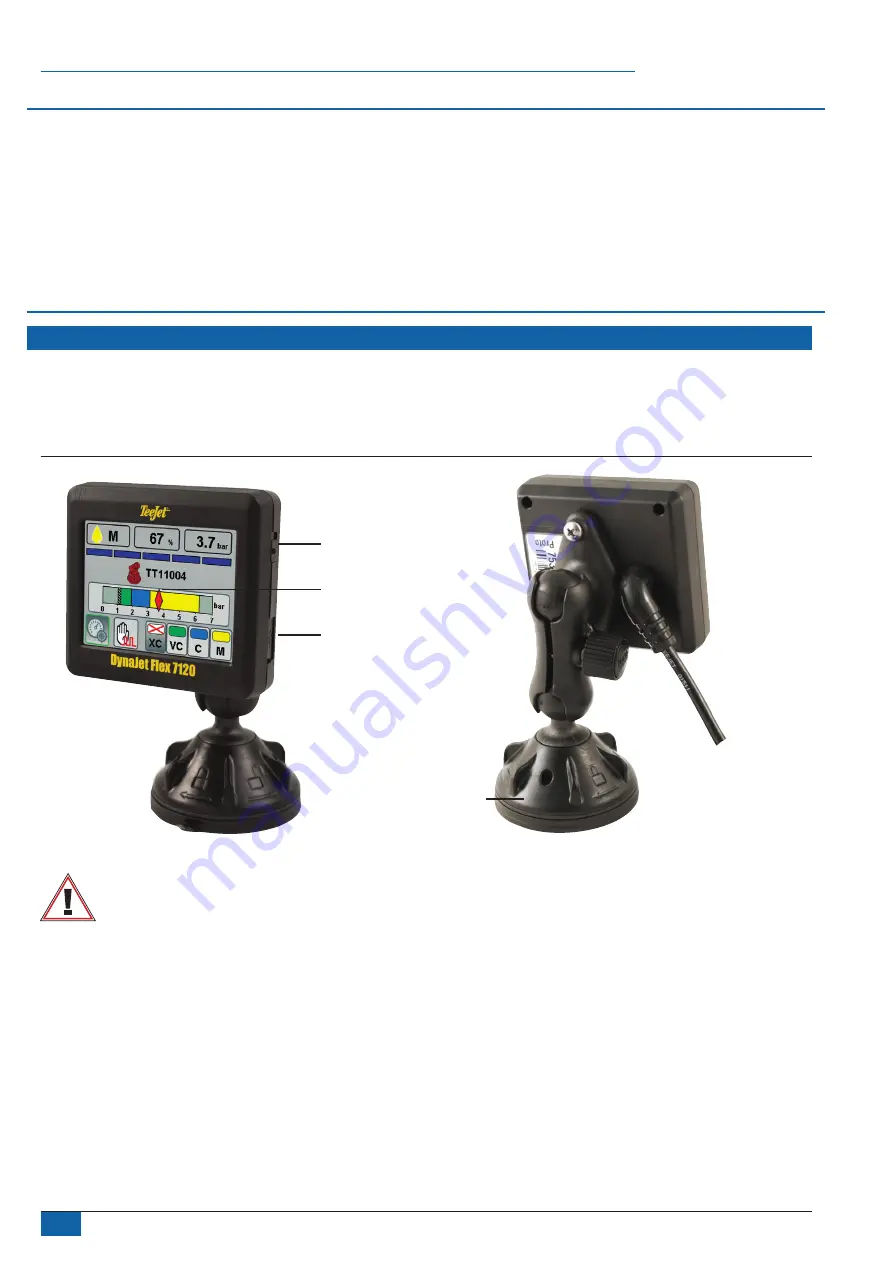
1
www.teejet.com
DynaJet
®
Flex
DYNAJET® FLEX OVERVIEW
The DynaJet Flex controller works in conjunction with an existing rate controller that regulates flow via a control valve or pump regulation to
achieve a target application rate while maintaining target droplet size(s) when a speed change occurs. This system only works with automatic
rate controllers that use flow based monitoring systems and not pressure based monitoring systems. Automatic rate controllers equipped for
both flow and pressure based control should have the pressure-based system disabled to work in conjunction with DynaJet Flex.
The independent automatic rate controller loop performs the same as it would if the DynaJet controller were not present. The DynaJet Flex
controller changes flow output to each individual nozzle based upon input provided from the operator about the optimum droplet size
(pressure) for the application.
INSTALLATION
CONSOLE
The DynaJet Flex console is designed to provide years of service under typical agricultural and turf operating conditions. A tight fitting
enclosure means that typical dusty environments will not cause operational problems. While occasional splashing of water will not damage
the unit, the DynaJet Flex console is not designed for direct exposure to rain. Take care not to operate the DynaJet Flex console in wet
conditions.
Figure 1: DynaJet Flex 7120 console front and back
to DynaJet interface
harness connection
Power switch
USB port
Standard RAM bracket
Bright touch screen
Safety information
TeeJet Technologies is not responsible for damage or physical harm caused by failure to adhere to the following safety
requirements.
As the operator of the vehicle, you are responsible for its safe operation.
The DynaJet Flex is not designed to replace the vehicle’s operator.
Be sure that the area around the vehicle is clear of people and obstacles before and during engagement.
The DynaJet Flex is designed to support and improve efficiency while working in the field. The driver has full responsibility for the quality and
work related results.
Summary of Contents for DynaJet Flex 7120
Page 23: ......