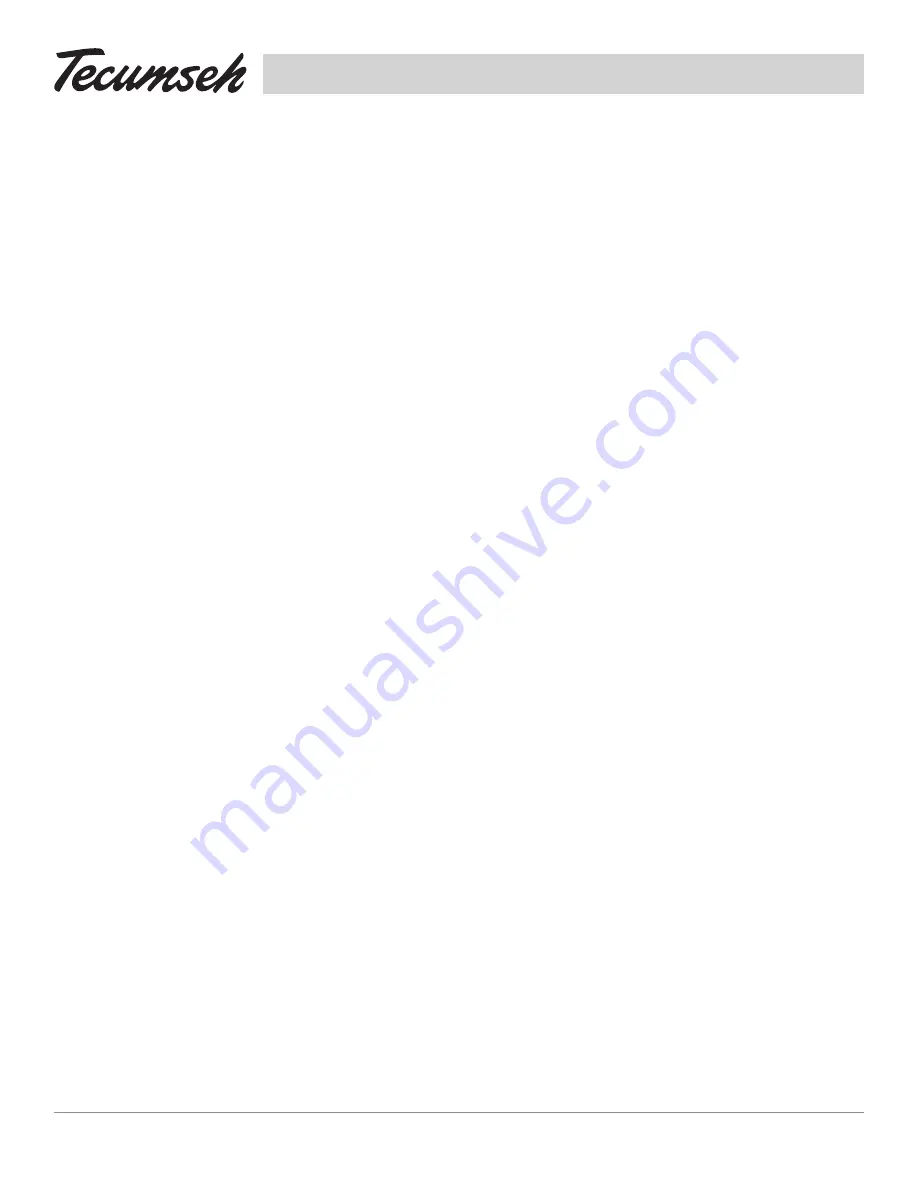
6
©2019 Tecumseh Compressor Company LLC. All rights reserved.
TPC Part #71511 | Rev A 05/13/2019
www.tecumseh.com
SYSTEM FLUSHING, PURGING, AND PRESSURE TESTING FOR LEAKS
Failure to properly flush, purge, or pressure test a system for leaks can result in serious injury or death from
explosion, fire, or contact with acid-saturated refrigerant or oil mists. A pressure leak test is mandatory and is to be
performed for the complete refrigeration system, including the condensing unit, prior to system charging.
To thoroughly leak check the system, the system should be pressurized to a maximum of 150 psig with dry
nitrogen to the high and low side of the system. With the pressure equalized at 150 psig, a leak check should be
performed on EVERY joint in the system, including the condensing unit, to ensure that no major leaks are present.
The initial charge may then be released.
Follow these precautions when flushing, purging or pressure testing a system for leaks:
• Use flushing products according to the manufacturer’s instructions
• To purge a system, use only dry nitrogen.
• When pressure testing for leaks, use only regulated dry nitrogen or dry nitrogen plus de minimis amounts of
serial label refrigerant.
• When purging or pressure testing any refrigeration or air conditioning system for leaks, never use air, oxygen or
acetylene.
1. Oxygen can explode on contact with oil.
2. Acetylene can decompose and explode when exposed to pressures greater than approximately 15 psig.
3. Combining an oxidizing gas, such as oxygen or air, with an HCFC or HFC refrigerant under pressure
can result in a fire or explosion.
Use a pressure regulating valve and pressure gauges.
• Commercial Cylinders of nitrogen contain pressures in excess of 2000 psig at 70°F. At pressures much lower
than 2000 psig, compressors can explode and cause serious injury or death. To avoid over pressurizing the
system, always use a pressure-regulating valve on the nitrogen cylinder discharge. The pressure regulator must
be able to reduce the pressure down to 1 to 2 psig and maintain this pressure.
PRESSURE TESTING FOR LEAKS
The leak check procedure should then be repeated using a much more accurate means to determine that the
system is 100% free of leaks. Use of electronic leak detection equipment is highly recommended due to its
potential accuracy when used correctly in accordance with the manufacturers instructions. If trace amounts of
refrigerant are used, use only the refrigerant indicated on the serial label of the condensing unit.
If de minimis amounts of refrigerant are used during the leak check procedure, this must be properly recovered
and disposed of in an appropriate manner to protect the environment. As an added precaution, the leak check charge
should be left in the system for no less than 12 hours without loss of pressure.
Every joint in the system including, but not limited to, factory welds, flare nuts and pressure controls
must be leak checked.
A leak free system is required for the installation to function correctly.
Summary of Contents for Argus
Page 1: ...Remote Condensing Unit Installation Instructions ...
Page 35: ...NOTES ...