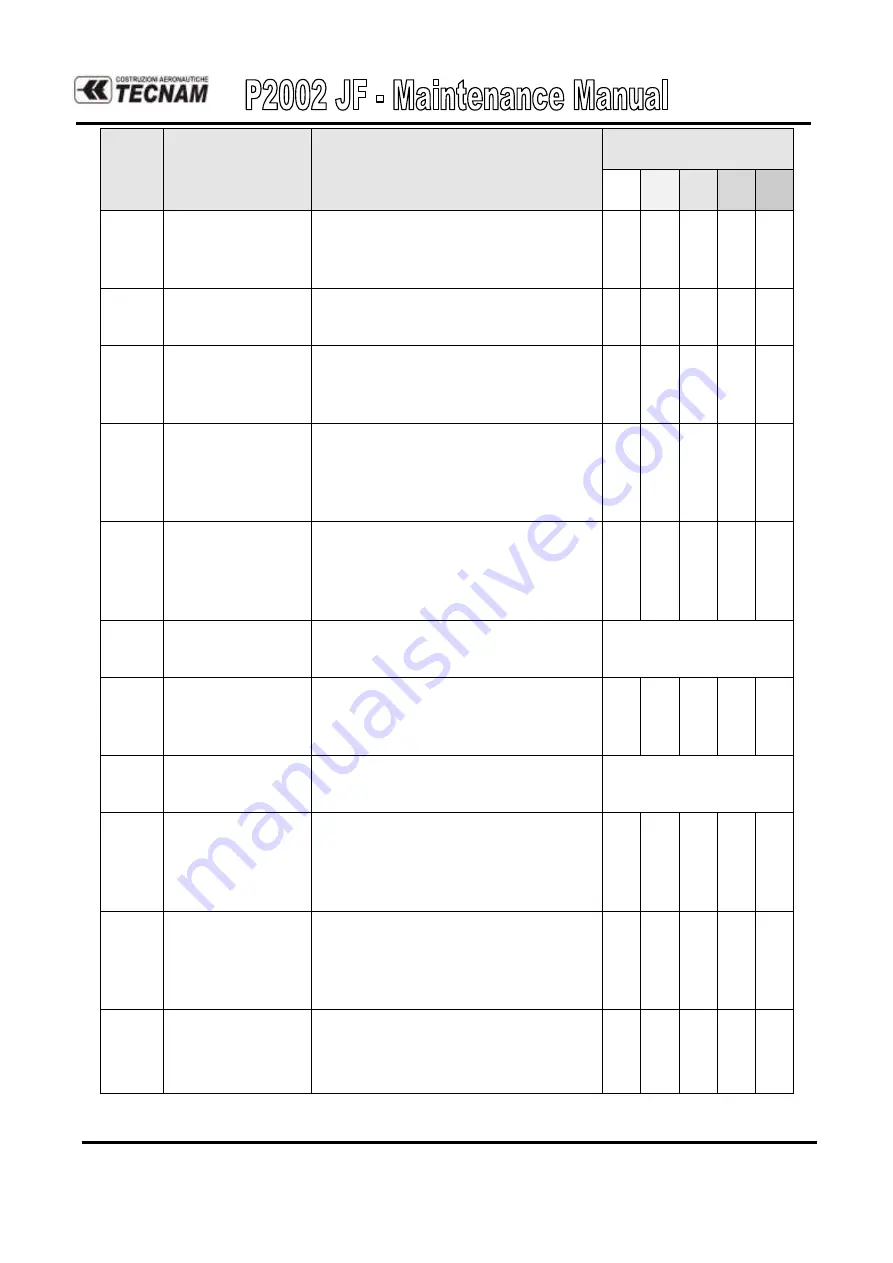
2
nd
Edition - Rev 0
Page 11
05-20
INSPECTION PROGRAM
ATA
Item
Maintenance task
FREQUENCY
A B C D E
33
Lights
Check instruments lights, cockpit
cabin and switches lights and related
dimmers devices operate correctly.
X
33
Lights
Check emergency light(courtesy light
for operation (if installed).
X
34
Navigation
Inspect Navigation equipment for
general condition, operation and se-
curity of installation.
X
34
Navigation
Inspect electronic installations for
condition and security: check anten-
nas and mounts for damage and secu-
rity.
X
34
Navigation
Pitot and static system: check static
ports for condition and operation. Ex-
amine Pitot-static system water trap,
drain if required.
X
34
Navigation
Check calibration of airspeed indica-
tor and altimeter. Perform leak test.
24 months
34
Navigation
Inspect magnetic compass for condi-
tion, operation and security of instal-
lation.
X
34
Navigation
Perform Magnetic compass compen-
sation procedure
24 months
52
Doors
Inspect the canopy for damage and
operation. Check latches and hinges
for condition and security of installa-
tion.
X
53
Fuselage
Remove all cabin inspection caps. In-
spect flight compartment for absence
of loose equipment that might foul
the controls.
X
53
Fuselage
Inspect externally skins, bulkheads,
frames and rivets for damage and
sealing. Inspect drainage holes for
free of obstructions.
X
Summary of Contents for P2002 JF
Page 2: ...2nd Edition Rev 0 INTENTIONALLY LEFT BLANK ...
Page 5: ...Page 3 2nd Edition Rev 0 RECORD OF REVISIONS INTENTIONALLY LEFT BLANK ...
Page 6: ...Page 4 2nd Edition Rev 0 RECORD OF REVISIONS INTENTIONALLY LEFT BLANK ...
Page 7: ...2nd Edition Rev 0 Chapter 01 Introduction ...
Page 8: ...2nd Edition Rev 0 INTENTIONALLY LEFT BLANK ...
Page 10: ...Page 2 2nd Edition Rev 0 01 LOEP INTENTIONALLY LEFT BLANK ...
Page 12: ...Page 2 2nd Edition Rev 0 01 TOC INTENTIONALLY LEFT BLANK ...
Page 16: ...Page 3 2nd Edition Rev 0 01 20 MANUAL BREAKDOWN AND ORGANIZATION INTENTIONALLY LEFT BLANK ...
Page 20: ...Page 2 2nd Edition Rev 0 01 40 OCCURRENCE REPORTING INSTRUCTIONS ...
Page 21: ...Page 3 2nd Edition Rev 0 01 40 OCCURRENCE REPORTING INSTRUCTIONS INTENTIONALLY LEFT BLANK ...
Page 22: ...Page 4 2nd Edition Rev 0 01 40 OCCURRENCE REPORTING INSTRUCTIONS INTENTIONALLY LEFT BLANK ...
Page 23: ...2nd Edition Rev 0 Chapter 02 Conversion charts ...
Page 24: ...2nd Edition Rev 0 INTENTIONALLY LEFT BLANK ...
Page 26: ...Page 2 2nd Edition Rev 0 02 LOEP INTENTIONALLY LEFT BLANK ...
Page 28: ...Page 2 2nd Edition Rev 0 02 TOC INTENTIONALLY LEFT BLANK ...
Page 34: ...Page 4 2nd Edition Rev 0 02 20 CONVERSION TABLES INTENTIONALLY LEFT BLANK ...
Page 35: ...2nd Edition Rev 0 Chapter 03 Airplane general description ...
Page 36: ...2nd Edition Rev 0 INTENTIONALLY LEFT BLANK ...
Page 38: ...Page 2 2nd Edition Rev 0 03 LOEP INTENTIONALLY LEFT BLANK ...
Page 40: ...Page 2 2nd Edition Rev 0 03 TOC INTENTIONALLY LEFT BLANK ...
Page 58: ...Page 18 2nd Edition Rev 0 03 00 AIRPLANE GENERAL DESCRIPTION INTENTIONALLY LEFT BLANK ...
Page 60: ...2nd Edition Rev 0 INTENTIONALLY LEFT BLANK ...
Page 62: ...Page 2 2nd Edition Rev 0 04 LOEP INTENTIONALLY LEFT BLANK ...
Page 66: ...Page 3 2nd Edition Rev 0 04 00 AIRWORTHINESS LIMITATIONS INTENTIONALLY LEFT BLANK ...
Page 67: ...2nd Edition Rev 0 Chapter 05 Time Limits and Maintenance schedule ...
Page 68: ...2nd Edition Rev 0 INTENTIONALLY LEFT BLANK ...
Page 72: ...2nd Edition Rev 0 05 00 LOEP Page 4 INTENTIONALLY LEFT BLANK ...
Page 74: ...2nd Edition Rev 0 05 00 TOC Page 2 INTENTIONALLY LEFT BLANK ...
Page 76: ...2nd Edition Rev 0 05 00 GENERAL Page 2 INTENTIONALLY LEFT BLANK ...
Page 78: ...2nd Edition Rev 0 05 10 COMPONENT TIME LIMITS Page 2 INTENTIONALLY LEFT BLANK ...
Page 81: ...2nd Edition Rev 0 Page 3 05 20 INSPECTION PROGRAM INTENTIONALLY LEFT BLANK ...
Page 95: ...2nd Edition Rev 0 Page 17 05 20 INSPECTION PROGRAM INTENTIONALLY LEFT BLANK ...
Page 96: ...2nd Edition Rev 0 Page 18 05 20 INSPECTION PROGRAM INTENTIONALLY LEFT BLANK ...
Page 101: ...2nd Edition Rev 0 Page 5 05 30 LUBRICATION Figure 1 Inspection points ...
Page 102: ...2nd Edition Rev 0 Page 6 05 30 LUBRICATION Figure 2 Inspection points details ...
Page 105: ...2nd Edition Rev 0 Page 9 05 30 LUBRICATION Figure 7 Stabilator supports ...
Page 117: ...2nd Edition Rev 0 Page 21 05 30 LUBRICATION Figure 29 Nose gear wing bearings 42 ...
Page 125: ...2nd Edition Rev 0 Page 6 05 50 SPECIAL SCHEDULED MAINTENANCE INTENTIONALLY LEFT BLANK ...
Page 134: ...2nd Edition Rev 0 Page 9 05 60 UNSCHEDULED MAINTENACE INTENTIONALLY LEFT BLANK ...
Page 135: ...2nd Edition Rev 0 Chapter 06 Dimensions and inspection caps ...
Page 136: ...2nd Edition Rev 0 INTENTIONALLY LEFT BLANK ...
Page 138: ...Page 2 2nd Edition Rev 0 O6 LOEP INTENTIONALLY LEFT BLANK ...
Page 143: ...Page 4 2nd Edition Rev 0 O6 00 DIMENSIONS AND AREAS INTENTIONALLY LEFT BLANK ...
Page 145: ...Page 2 2nd Edition Rev 0 O6 10 INSPECTION CAPS Figure 2 Inspection caps ...
Page 147: ...Page 4 2nd Edition Rev 0 O6 10 INSPECTION CAPS INTENTIONALLY LEFT BLANK ...
Page 148: ...Page 5 2nd Edition Rev 0 O6 10 INSPECTION CAPS INTENTIONALLY LEFT BLANK ...
Page 149: ...2nd Edition Rev 0 Chapter 07 Jacking ...
Page 150: ...2nd Edition Rev 0 INTENTIONALLY LEFT BLANK ...
Page 152: ...Page 2 2nd Edition Rev 0 O7 LOEP INTENTIONALLY LEFT BLANK ...
Page 154: ...Page 2 2nd Edition Rev 0 O7 TOC INTENTIONALLY LEFT BLANK ...
Page 158: ...Page 203 2nd Edition Rev 0 07 00 JACKING MAINTENANCE PRACTICES INTENTIONALLY LEFT BLANK ...
Page 159: ...2nd Edition Rev 0 Chapter 08 Leveling and Weighing ...
Page 160: ...2nd Edition Rev 0 INTENTIONALLY LEFT BLANK ...
Page 162: ...Page 2 2nd Edition Rev 0 O8 LOEP INTENTIONALLY LEFT BLANK ...
Page 164: ...Page 2 2nd Edition Rev 0 O8 TOC INTENTIONALLY LEFT BLANK ...
Page 171: ...Page 203 2nd Edition Rev 0 O8 20 WEIGHING and BALANCE INTENTIONALLY LEFT BLANK ...
Page 172: ...Page 204 2nd Edition Rev 0 O8 20 WEIGHING and BALANCE INTENTIONALLY LEFT BLANK ...
Page 173: ...2nd Edition Rev 0 Chapter 09 Towing and Taxiing ...
Page 174: ...2nd Edition Rev 0 INTENTIONALLY LEFT BLANK ...
Page 176: ...Page 2 2nd Edition Rev 0 O9 LOEP INTENTIONALLY LEFT BLANK ...
Page 178: ...Page 2 2nd Edition Rev 0 09 TOC INTENTIONALLY LEFT BLANK ...
Page 180: ...Page 201 2nd Edition Rev 0 09 10 TOWING MAINTENANCE PRACTICES INTENTIONALLY LEFT BLANK ...
Page 182: ...Page 201 2nd Edition Rev 0 09 20 TAXIING MAINTENANCE PRACTICES INTENTIONALLY LEFT BLANK ...
Page 183: ...2nd Edition Rev 0 Chapter 10 Parking Mooring Storage and Return to Service ...
Page 184: ...2nd Edition Rev 0 INTENTIONALLY LEFT BLANK ...
Page 186: ...Page 2 2nd Edition Rev 0 10 LOEP INTENTIONALLY LEFT BLANK ...
Page 188: ...Page 2 2nd Edition Rev 0 10 TOC INTENTIONALLY LEFT BLANK ...
Page 191: ...Page 201 2nd Edition Rev 0 10 20 MOORING Figure 1 Mooring scheme ...
Page 194: ...Page 202 2nd Edition Rev 0 10 20 STORAGE AND RETURN TO SERVICE INTENTIONALLY LEFT BLANK ...
Page 195: ...2nd Edition Rev 0 Chapter 11 Markings and Placards ...
Page 196: ...2nd Edition Rev 0 INTENTIONALLY LEFT BLANK ...
Page 198: ...Page 2 2nd Edition Rev 0 11 LOEP INTENTIONALLY LEFT BLANK ...
Page 200: ...Page 2 2nd Edition Rev 0 11 TOC INTENTIONALLY LEFT BLANK ...
Page 215: ...2nd Edition Rev 0 Chapter 12 Servicing ...
Page 216: ...2nd Edition Rev 0 INTENTIONALLY LEFT BLANK ...
Page 218: ...Page 2 2nd Edition Rev 0 12 TOC INTENTIONALLY LEFT BLANK ...
Page 227: ...Page 202 2nd Edition Rev 0 12 20 OIL SYSTEM SERVICING PRACTICES Figure 3 Oil tank location ...
Page 239: ...Page 201 2nd Edition Rev 0 12 60 BATTERY SERVICING PRACTICES Figure 11 Anti vibration PAD ...
Page 244: ...Page 203 2nd Edition Rev 0 12 80 BRAKE SYSTEM SERVICING PRACTICES INTENTIONALLY LEFT BLANK ...
Page 245: ...Page 204 2nd Edition Rev 0 12 80 BRAKE SYSTEM SERVICING PRACTICES INTENTIONALLY LEFT BLANK ...
Page 246: ...Page 205 2nd Edition Rev 0 12 80 BRAKE SYSTEM SERVICING PRACTICES INTENTIONALLY LEFT BLANK ...
Page 247: ...2nd Edition Rev 0 Chapter 20 Standard practices Airframe ...
Page 248: ...2nd Edition Rev 0 INTENTIONALLY LEFT BLANK ...
Page 250: ...Page 2 2nd Edition Rev 0 20 LOEP INTENTIONALLY LEFT BLANK ...
Page 271: ...Page 210 2nd Edition Rev 0 02 40 SAFETYING MAINTENANCE PRACTICES ...
Page 275: ...Page 214 2nd Edition Rev 0 02 40 SAFETYING MAINTENANCE PRACTICES INTENTIONALLY LEFT BLANK ...
Page 276: ...Page 215 2nd Edition Rev 0 02 40 SAFETYING MAINTENANCE PRACTICES INTENTIONALLY LEFT BLANK ...
Page 277: ...2nd Edition Rev 0 Chapter 21 Heating and ventilation ...
Page 278: ...2nd Edition Rev 0 INTENTIONALLY LEFT BLANK ...
Page 280: ...Page 2 2nd Edition Rev 0 21 LOEP INTENTIONALLY LEFT BLANK ...
Page 295: ...Page 206 2nd Edition Rev 0 21 10 CABIN HEATING MAINTENANCE PRACTICE INTENTIONALLY LEFT BLANK ...
Page 300: ...Page 201 2nd Edition Rev 0 21 20 VENTILATION MAINTENANCE PRATICE INTENTIONALLY LEFT BLANK ...
Page 301: ...2nd Edition Rev 0 Chapter 23 Communications ...
Page 302: ...2nd Edition Rev 0 INTENTIONALLY LEFT BLANK ...
Page 304: ...Page 2 2nd Edition Rev 0 23 LOEP INTENTIONALLY LEFT BLANK ...
Page 313: ...Page 8 2nd Edition Rev 0 23 10 COMM 1 AND 2 DESCRIPTION AND OPERATION Figure 8 Antennas ...
Page 325: ...Page 208 2nd Edition Rev 0 23 10 COMM 1 and 2 MANTEINANCE PRACTICE INTENTIONALLY LEFT BLANK ...
Page 326: ...Page 209 2nd Edition Rev 0 23 10 COMM 1 and 2 MANTEINANCE PRACTICE INTENTIONALLY LEFT BLANK ...
Page 327: ...2nd Edition Rev 0 Chapter 24 Electrical system ...
Page 328: ...2nd Edition Rev 0 INTENTIONALLY LEFT BLANK ...
Page 330: ...Page 2 2nd Edition Rev 0 24 LOEP INTENTIONALLY LEFT BLANK ...
Page 333: ...Page 2 2nd Edition Rev 0 24 10 GENERAL IINTENTIONALLY LEFT BLANK ...
Page 361: ...2nd Edition Rev 0 Chapter 25 Equipment and furnishing ...
Page 362: ...2nd Edition Rev 0 INTENTIONALLY LEFT BLANK ...
Page 364: ...Page 2 2nd Edition Rev 0 25 LOEP INTENTIONALLY LEFT BLANK ...
Page 386: ...Page 201 2nd Edition Rev 0 25 30 ELT MAINTENANCE PRACTICES Figure 10 ELT ...
Page 388: ...Page 1 2nd Edition Rev 0 25 30 FIRT AID KIT INTENTIONALLY LEFT BLANK ...
Page 389: ...2nd Edition Rev 0 Chapter 26 Fire protection ...
Page 390: ...2nd Edition Rev 0 INTENTIONALLY LEFT BLANK ...
Page 392: ...Page 2 2nd Edition Rev 0 26 LOEP INTENTIONALLY LEFT BLANK ...
Page 399: ...2nd Edition Rev 0 Chapter 27 Flight controls ...
Page 400: ...2nd Edition Rev 0 INTENTIONALLY LEFT BLANK ...
Page 421: ...Page 210 2nd Edition Rev 0 27 20 AILERONS MAINTENANCE PRACTICES INTENTIONALLY LEFT BLANK ...
Page 424: ...Page 3 2nd Edition Rev 0 27 30 FLAPS DESCRIPTION AND OPERATION INTENTIONALLY LEFT BLANK ...
Page 449: ...Page 205 2nd Edition Rev 0 27 50 RUDDER MAINTENANCE PRACTICES INTENTIONALLY LEFT BLANK ...
Page 450: ...Page 206 2nd Edition Rev 0 27 50 RUDDER MAINTENANCE PRACTICES INTENTIONALLY LEFT BLANK ...
Page 451: ...2nd Edition Rev 0 Chapter 28 Fuel system ...
Page 452: ...2nd Edition Rev 0 INTENTIONALLY LEFT BLANK ...
Page 454: ...Page 2 2nd Edition Rev 0 28 LOEP INTENTIONALLY LEFT BLANK ...
Page 456: ...Page 2 2nd Edition Rev 0 28 TOC INTENTIONALLY LEFT BLANK ...
Page 477: ...Page 214 2nd Edition Rev 0 28 10 FUEL SYSTEM MAINTENANCE PRACTICE A C B Figure 13 Fuel system ...
Page 479: ...Page 216 2nd Edition Rev 0 28 10 FUEL SYSTEM MAINTENANCE PRACTICE INTENTIONALLY LEFT BLANK ...
Page 480: ...Page 200 2nd Edition Rev 0 28 10 FUEL SYSTEM MAINTENANCE PRACTICE INTENTIONALLY LEFT BLANK ...
Page 481: ...2nd Edition Rev 0 Chapter 30 Ice protection ...
Page 482: ...2nd Edition Rev 0 INTENTIONALLY LEFT BLANK ...
Page 484: ...Page 2 2nd Edition Rev 0 02 LOEP INTENTIONALLY LEFT BLANK ...
Page 485: ...Page 1 2nd Edition Rev 0 02 TOC CHAPTER 30 TABLE OF CONTENTS 30 00 ICE PROTECTION GENERAL 100 ...
Page 487: ...2nd Edition Rev 0 Chapter 31 Indicating system ...
Page 488: ...2nd Edition Rev 0 INTENTIONALLY LEFT BLANK ...
Page 491: ...Page 3 2nd Edition Rev 0 31 TOC INTENSIONALLY LEFT BLANK ...
Page 506: ...2nd Edition Rev 0 Chapter 32 Landing gear ...
Page 507: ...2nd Edition Rev 0 INTENTIONALLY LEFT BLANK ...
Page 512: ...Page 3 2nd Edition Rev 0 32 TOC INTENTIONALLY LEFT BLANK ...
Page 516: ...Page 101 2nd Edition Rev 0 32 10 MLG and BRAKES TROUBLESHOOTING INTENTIONALLY LEFT BLANK ...
Page 566: ...2nd Edition Rev 0 Chapter 33 Lights ...
Page 567: ...2nd Edition Rev 0 INTENTIONALLY LEFT BLANK ...
Page 569: ...Page 2 2nd Edition Rev 0 33 LOEP INTENTIONALLY LEFT BLANK ...
Page 588: ...2nd Edition Rev 0 Chapter 34 Navigation ...
Page 589: ...2nd Edition Rev 0 INTENTIONALLY LEFT BLANK ...
Page 641: ...2nd Edition Rev 0 Chapter 51 Standard Practices Structures ...
Page 642: ...2nd Edition Rev 0 INTENTIONALLY LEFT BLANK ...
Page 673: ...Page 3 2nd Edition Rev 0 51 40 ALIGNMENT CHECK GENERAL INTENTIONALLY LEFT BLANK ...
Page 674: ...2nd Edition Rev 0 Chapter 52 Canopy ...
Page 675: ...2nd Edition Rev 0 INTENTIONALLY LEFT BLANK ...
Page 677: ...Page 2 2nd Edition Rev 0 52 LOEP INTENTIONALLY LEFT BLANK ...
Page 680: ...Page 2 2nd Edition Rev 0 52 00 CANOPY GENERAL Figure 3 Windshield and canopy ...
Page 687: ...Page 3 2nd Edition Rev 0 52 10 DOOR SAFETY LOCK GENERAL Figure 11 Upper safety lock internal ...
Page 691: ...Page 2 2nd Edition Rev 0 52 20 CANOPY REMOVAL INSTALLATION GENERAL INTENTIONALLY LEFT BLANK ...
Page 702: ...2nd Edition Rev 0 Chapter 53 Fuselage ...
Page 703: ...2nd Edition Rev 0 INTENTIONALLY LEFT BLANK ...
Page 705: ...Page 2 2nd Edition Rev 0 53 LOEP INTENTIONALLY LEFT BLANK ...
Page 714: ...Page 204 2nd Edition Rev 0 53 10 FUSELAGE MAINTENANCE PRACTICES INTENTIONALLY LEFT BLANK ...
Page 715: ...Page 205 2nd Edition Rev 0 53 10 FUSELAGE MAINTENANCE PRACTICES INTENTIONALLY LEFT BLANK ...
Page 716: ...2nd Edition Rev 0 Chapter 55 Stabilator and Rudder ...
Page 717: ...2nd Edition Rev 0 INTENTIONALLY LEFT BLANK ...
Page 719: ...Page 2 2nd Edition Rev 0 55 LOEP INTENTIONALLY LEFT BLANK ...
Page 724: ...Page 4 2nd Edition Rev 0 55 10 STABILATOR DESCRIPTION AND OPERATION INTENTIONALLY LEFT BLANK ...
Page 725: ...Page 5 2nd Edition Rev 0 55 10 STABILATOR DESCRIPTION AND OPERATION INTENTIONALLY LEFT BLANK ...
Page 738: ...Page 204 2nd Edition Rev 0 55 20 RUDDER MAINTENANCE PRACTICES INTENTIONALLY LEFT BLANK ...
Page 739: ...2nd Edition Rev 0 Chapter 56 Windows ...
Page 740: ...2nd Edition Rev 0 INTENTIONALLY LEFT BLANK ...
Page 742: ...Page 2 2nd Edition Rev 0 56 LOEP INTENTIONALLY LEFT BLANK ...
Page 747: ...Page 4 2nd Edition Rev 0 56 10 WINDOWS DESCRIPTION AND OPERATION INTENTIONALLY LEFT BLANK ...
Page 751: ...Page 203 2nd Edition Rev 0 56 10 WINDOWS MAINTENANCE AND PRACTICES Figure 2 Windshield ...
Page 753: ...Page 201 2nd Edition Rev 0 56 10 WINDOWS MAINTENANCE AND PRACTICES Figure 3 Side window ...
Page 755: ...Page 201 2nd Edition Rev 0 56 10 WINDOWS MAINTENANCE AND PRACTICES Figure 3 Canopy window ...
Page 756: ...Page 202 2nd Edition Rev 0 56 10 WINDOWS MAINTENANCE AND PRACTICES INTENTIONALLY LEFT BLANK ...
Page 757: ...Page 203 2nd Edition Rev 0 56 10 WINDOWS MAINTENANCE AND PRACTICES INTENTIONALLY LEFT BLANK ...
Page 758: ...Chapter 57 Wings ...
Page 759: ...INTENTIONALLY LEFT BLANK ...
Page 761: ...Page 2 2nd Edition Rev 0 57 LOEP INTENTIONALLY LEFT BLANK ...
Page 765: ...Page 4 2nd Edition Rev 0 57 10 WINGS DESCRIPTION AND OPERATIONS Figure 2 Wing stations ...
Page 766: ...Page 5 2nd Edition Rev 0 57 10 WINGS DESCRIPTION AND OPERATIONS INTENTIONALLY LEFT BLANK ...
Page 777: ...Page 210 2nd Edition Rev 0 57 10 WINGS MAINTENANCE PRACTICE Figure 8 RH Aileron ...
Page 780: ...Page 213 2nd Edition Rev 0 57 10 WINGS MAINTENANCE PRACTICE INTENTIONALLY LEFT BLANK ...
Page 781: ...Page 214 2nd Edition Rev 0 57 10 WINGS MAINTENANCE PRACTICE INTENTIONALLY LEFT BLANK ...
Page 782: ...2nd Edition Rev 0 Chapter 61 Propeller ...
Page 783: ...2nd Edition Rev 0 INTENTIONALLY LEFT BLANK ...
Page 785: ...Page 2 2nd Edition Rev 0 61 LOEP INTENTIONALLY LEFT BLANK ...
Page 787: ...Page 2 2nd Edition Rev 0 61 TOC INTENTIONALLY LEFT BLANK ...
Page 789: ...Page 2 2nd Edition Rev 0 61 10 PROPELLER DESCRIPTION AND OPERATION INTENTIONALLY LEFT BLANK ...
Page 796: ...Page 205 2nd Edition Rev 0 61 10 PROPELLER MAINTENACE PRACTICES INTENTIONALLY LEFT BLANK ...
Page 797: ...Page 206 2nd Edition Rev 0 61 10 PROPELLER MAINTENACE PRACTICES INTENTIONALLY LEFT BLANK ...
Page 798: ...Chapter 71 Power plant ...
Page 799: ...INTENTIONALLY LEFT BLANK ...
Page 801: ...Page 2 2nd Edition Rev 0 71 LOEP INTENTIONALLY LEFT BLANK ...
Page 816: ...Page 204 2nd Edition Rev 0 71 20 ENGINE MOUNT MAINTENANCE PROCESSES INTENTIONALLY LEFT BLANK ...
Page 828: ...Chapter 75 Liquid cooling system ...
Page 829: ...INTENTIONALLY LEFT BLANK ...
Page 831: ...Page 2 2nd Edition Rev 0 75 LOEP INTENTIONALLY LEFT BLANK ...
Page 846: ...2nd Edition Rev 0 Chapter 78 Exhaust ...
Page 847: ...2nd Edition Rev 0 INTENTIONALLY LEFT BLANK ...
Page 849: ...Page 2 2nd Edition Rev 0 78 LOEP INTENTIONALLY LEFT BLANK ...
Page 862: ...Page 209 2nd Edition Rev 0 78 10 EXHAUST MAINTENACE PRACTICES INTENTIONALLY LEFT BLANK ...
Page 863: ...Page 210 2nd Edition Rev 0 78 10 EXHAUST MAINTENACE PRACTICES INTENTIONALLY LEFT BLANK ...
Page 864: ...Chapter 79 Oil system ...
Page 865: ...INTENTIONALLY LEFT BLANK ...
Page 867: ...Page 2 2nd Edition Rev 0 79 LOEP INTENTIONALLY LEFT BLANK ...
Page 875: ...Page 7 2nd Edition Rev 0 79 10 OIL SYSTEM DESCRIPTION AND OPERATION Figure 7 Oil tank ...
Page 876: ...Page 8 2nd Edition Rev 0 79 10 OIL SYSTEM DESCRIPTION AND OPERATION INTENTIONALLY LEFT BLANK ...
Page 888: ...Chapter 80 Starting ...
Page 889: ...INTENTIONALLY LEFT BLANK ...
Page 891: ...Page 2 2nd Edition Rev 0 80 LOEP INTENTIONALLY LEFT BLANK ...
Page 894: ...Page 2 2nd Edition Rev 0 80 10 STARTING DESCRIPTION AND OPERATION INTENTIONALLY LEFT BLANK ...
Page 898: ...Page 202 2nd Edition Rev 0 80 10 STARTING DESCRIPTION AND OPERATION Figure 2 Starter relay ...
Page 899: ...Page 203 2nd Edition Rev 0 80 10 STARTING DESCRIPTION AND OPERATION INTENTIONALLY LEFT BLANK ...
Page 900: ...2nd Edition Rev 0 AMM SUPPLEMENTS LIST Page 1 Tecnam P2002JF AMM Supplements List ...
Page 905: ...Page 3 SUPPLEMENT S4 RECORD OF REVISIONS 2nd Edition Rev0 INTENTIONALLY LEFT BLANK ...
Page 909: ...Page 2 SUPPLEMENT S4 TABLE OF CONTENTS 2nd Edition Rev0 INTENTIONALLY LEFT BLANK ...
Page 911: ...Page 2 SUPPLEMENT S4 INTRODUCTION 2nd Edition Rev0 INTENTIONALLY LEFT BLANK ...
Page 912: ...Page 1 SUPPLEMENT S4 SERVICING 2nd Edition Rev 0 Chapter 12 Servicing ...
Page 913: ...Page 2 SUPPLEMENT S4 SERVICING 2nd Edition Rev 0 INTENTIONALLY LEFT BLANK ...
Page 920: ...Page 1 SUPPLEMENT S4 STABILATOR AND RUDDER 2nd Edition Rev 0 Chapter 55 Stabilator and Rudder ...
Page 921: ...Page 2 SUPPLEMENT S4 STABILATOR AND RUDDER 2nd Edition Rev 0 INTENTIONALLY LEFT BLANK ...
Page 942: ...Page 1 SUPPLEMENT S4 ENGINE 2nd Edition Rev 0 Chapter 72 Engine ...
Page 943: ...Page 2 SUPPLEMENT S4 ENGINE 2nd Edition Rev 0 INTENTIONALLY LEFT BLANK ...
Page 955: ...INTENTIONALLY LEFT BLANK ...
Page 957: ...2nd Edition Rev 0 SUPPLEMENT S1 LOEP Page 2 INTENTIONALLY LEFT BLANK ...
Page 961: ...2nd Edition Rev 0 SUPPLEMENT S1 TABLE OF CONTENTS Page 6 INTENTIONALLY LEFT BLANK ...
Page 963: ...2nd Edition Rev 0 SUPPLEMENT S1 INTRODUCTION Page 8 INTENTIONALLY LEFT BLANK ...
Page 968: ...2nd Edition Rev 0 SUPPLEMENT S1 Chapter 5 Inspection Program Page 3 INTENTIONALLY LEFT BLANK ...
Page 969: ...2nd Edition Rev 0 SUPPLEMENT S1 Chapter 5 Inspection Program Page 4 INTENTIONALLY LEFT BLANK ...
Page 977: ...2nd Edition Rev 0 SUPPLEMENT S1 Chapter 61 Propeller Page 2 HUB DESIGNATION example ...
Page 978: ...2nd Edition Rev 0 SUPPLEMENT S1 Chapter 61 Propeller Page 3 BLADE DESIGNATION example ...
Page 987: ...2nd Edition Rev 0 SUPPLEMENT S1 Chapter 61 Propeller Page 207 INTENTIONALLY LEFT BLANK ...
Page 988: ...2nd Edition Rev 0 SUPPLEMENT S1 Chapter 61 Propeller Page 208 INTENTIONALLY LEFT BLANK ...
Page 990: ...INTENTIONALLY LEFT BLANK ...
Page 992: ...SUPPLEMENT S2 LOEP Page 2 2nd Edition Rev 0 INTENTIONALLY LEFT BLANK ...
Page 995: ...SUPPLEMENT S2 RECORD OF REVISIONS Page 3 2nd Edition Rev 0 INTENTIONALLY LEFT BLANK ...
Page 996: ...SUPPLEMENT S2 RECORD OF REVISIONS Page 4 2nd Edition Rev 0 INTENTIONALLY LEFT BLANK ...
Page 998: ...SUPPLEMENT S2 TABLE OF CONTENTS Page 2 2nd Edition Rev 0 INTENTIONALLY LEFT BLANK ...
Page 1000: ...SUPPLEMENT S2 INTRODUCTION Page 2 2nd Edition Rev 0 INTENTIONALLY LEFT BLANK ...
Page 1008: ...SUPPLEMENT S2 Chapter 5 Inspection Program Page 10 2nd Edition Rev 0 INTENTIONALLY LEFT BLANK ...
Page 1010: ...SUPPLEMENT S2 Chapter 6 Inspection Page 12 2nd Edition Rev 0 INTENTIONALLY LEFT BLANK ...
Page 1014: ...SUPPLEMENT S2 Chapter 23 Electric System Page 16 2nd Edition Rev 0 INTENTIONALLY LEFT BLANK ...
Page 1018: ...SUPPLEMENT S2 Chapter 27 Flight Control Page 20 2nd Edition Rev 0 INTENTIONALLY LEFT BLANK ...
Page 1020: ...SUPPLEMENT S2 Chapter 27 Flight Control Page 22 2nd Edition Rev 0 INTENTIONALLY LEFT BLANK ...
Page 1022: ...SUPPLEMENT S2 Chapter 53 Fuselage Page 24 2nd Edition Rev 0 INTENTIONALLY LEFT BLANK ...
Page 1026: ...INTENTIONALLY LEFT BLANK ...
Page 1033: ...2nd Edition Rev 0 SUPPLEMENT SG 3 RECORD OF REVISIONS Page 3 INTENTIONALLY LEFT BLANK ...
Page 1034: ...2nd Edition Rev 0 SUPPLEMENT SG 3 RECORD OF REVISIONS Page 4 INTENTIONALLY LEFT BLANK ...
Page 1036: ...2nd Edition Rev 0 SUPPLEMENT SG 3 TABLE OF CONTENTS Page 2 INTENTIONALLY LEFT BLANK ...
Page 1038: ...2nd Edition Rev 0 SUPPLEMENT SG 3 INTRODUCTION Page 2 INTENTIONALLY LEFT BLANK ...
Page 1097: ...2nd Edition Rev 0 SUPPLEMENT SG 3 CHAPTER 31 INDICATIONG SYSTEM Page 1 Chapter 34 Navigation ...
Page 1100: ...2nd Edition Rev 0 SUPPLEMENT SG 3 CHAPTER 34 DESCRIPTION AND OPERATION Page 4 530W ...
Page 1105: ...SUPPLEMENT SG 3 CHAPTER 92 WIRING DIAGRAMS Page 1 Chapter 92 Wiring diagrams ...
Page 1106: ...SUPPLEMENT SG 3 CHAPTER 92 WIRING DIAGRAMS Page 2 INTENTIONALLY LEFT BLANK ...
Page 1109: ...SUPPLEMENT SG 3 CHAPTER 92 WIRING DIAGRAMS Page 5 INTENTIONALLY LEFT BLANK ...
Page 1110: ...SUPPLEMENT SG 3 CHAPTER 92 WIRING DIAGRAMS Page 6 ...
Page 1111: ...SUPPLEMENT SG 3 CHAPTER 92 WIRING DIAGRAMS Page 7 ...
Page 1112: ...SUPPLEMENT SG 3 CHAPTER 92 WIRING DIAGRAMS Page 8 ...
Page 1113: ...SUPPLEMENT SG 3 CHAPTER 92 WIRING DIAGRAMS Page 9 ...
Page 1114: ...SUPPLEMENT SG 3 CHAPTER 92 WIRING DIAGRAMS Page 10 ...
Page 1115: ...SUPPLEMENT SG 3 CHAPTER 92 WIRING DIAGRAMS Page 11 ...
Page 1116: ...SUPPLEMENT SG 3 CHAPTER 92 WIRING DIAGRAMS Page 12 ...
Page 1117: ...SUPPLEMENT SG 3 CHAPTER 92 WIRING DIAGRAMS Page 13 ...
Page 1118: ...SUPPLEMENT SG 3 CHAPTER 92 WIRING DIAGRAMS Page 14 ...
Page 1119: ...SUPPLEMENT SG 3 CHAPTER 92 WIRING DIAGRAMS Page 15 ...
Page 1120: ...SUPPLEMENT SG 3 CHAPTER 92 WIRING DIAGRAMS Page 16 ...
Page 1121: ...SUPPLEMENT SG 3 CHAPTER 92 WIRING DIAGRAMS Page 17 ...
Page 1122: ...SUPPLEMENT SG 3 CHAPTER 92 WIRING DIAGRAMS Page 18 ...
Page 1123: ...SUPPLEMENT SG 3 CHAPTER 92 WIRING DIAGRAMS Page 19 ...
Page 1124: ...SUPPLEMENT SG 3 CHAPTER 92 WIRING DIAGRAMS Page 20 ...
Page 1125: ...SUPPLEMENT SG 3 CHAPTER 92 WIRING DIAGRAMS Page 21 ...
Page 1126: ...SUPPLEMENT SG 3 CHAPTER 92 WIRING DIAGRAMS Page 22 ...
Page 1127: ...SUPPLEMENT SG 3 CHAPTER 92 WIRING DIAGRAMS Page 23 ...
Page 1128: ...SUPPLEMENT SG 3 CHAPTER 92 WIRING DIAGRAMS Page 24 ...
Page 1129: ...SUPPLEMENT SG 3 CHAPTER 92 WIRING DIAGRAMS Page 25 ...
Page 1130: ...SUPPLEMENT SG 3 CHAPTER 92 WIRING DIAGRAMS Page 26 ...
Page 1131: ...SUPPLEMENT SG 3 CHAPTER 92 WIRING DIAGRAMS Page 27 ...
Page 1132: ...SUPPLEMENT SG 3 CHAPTER 92 WIRING DIAGRAMS Page 28 ...
Page 1133: ...SUPPLEMENT SG 3 CHAPTER 92 WIRING DIAGRAMS Page 29 ...
Page 1134: ...SUPPLEMENT SG 3 CHAPTER 92 WIRING DIAGRAMS Page 30 ...
Page 1135: ...SUPPLEMENT SG 3 CHAPTER 92 WIRING DIAGRAMS Page 31 ...
Page 1136: ...SUPPLEMENT SG 3 CHAPTER 92 WIRING DIAGRAMS Page 32 ...
Page 1137: ...SUPPLEMENT SG 3 CHAPTER 92 WIRING DIAGRAMS Page 33 ...
Page 1138: ...SUPPLEMENT SG 3 CHAPTER 92 WIRING DIAGRAMS Page 34 ...
Page 1139: ...SUPPLEMENT SG 3 CHAPTER 92 WIRING DIAGRAMS Page 35 INTENTIONALLY LEFT BLANK ...
Page 1143: ...Page 3 SUPPLEMENT S2 RECORD OF REVISIONS 1st Edition Rev0 INTENTIONALLY LEFT BLANK ...
Page 1147: ...Page 2 SUPPLEMENT S2 TABLE OF CONTENTS 1st Edition Rev0 INTENTIONALLY LEFT BLANK ...
Page 1149: ...Page 2 SUPPLEMENT S2 INTRODUCTION 1st Edition Rev0 INTENTIONALLY LEFT BLANK ...
Page 1150: ...Page 1 SUPPLEMENT S2 SERVICING 1st Edition Rev Chapter 12 Servicing ...
Page 1151: ...Page 2 SUPPLEMENT S2 SERVICING 1st Edition Rev INTENTIONALLY LEFT BLANK ...
Page 1158: ...Page 1 SUPPLEMENT S2 STABILATOR AND RUDDER 1st Edition Rev Chapter 55 Stabilator and Rudder ...
Page 1159: ...Page 2 SUPPLEMENT S2 STABILATOR AND RUDDER 1st Edition Rev INTENTIONALLY LEFT BLANK ...
Page 1166: ...Page 1 SUPPLEMENT S2 WINGS 1st Edition Rev0 Chapter 57 Wings ...
Page 1167: ...Page 2 SUPPLEMENT S2 WINGS 1st Edition Rev0 INTENTIONALLY LEFT BLANK ...
Page 1180: ...Page 1 SUPPLEMENT S2 ENGINE 1st Edition Rev Chapter 72 Engine ...
Page 1181: ...Page 2 SUPPLEMENT S2 ENGINE 1st Edition Rev INTENTIONALLY LEFT BLANK ...
Page 1193: ...INTENTIONALLY LEFT BLANK ...
Page 1201: ...2nd Edition Rev 0 SUPPLEMENT SG 1 LOEP Page 8 INTENTIONALLY LEFT BLANK ...
Page 1204: ...2nd Edition Rev 0 SUPPLEMENT SG 1 RECORD OF REVISIONS Page 3 INTENTIONALLY LEFT BLANK ...
Page 1205: ...2nd Edition Rev 0 SUPPLEMENT SG 1 RECORD OF REVISIONS Page 4 INTENTIONALLY LEFT BLANK ...
Page 1208: ...2nd Edition Rev 0 SUPPLEMENT SG 1 TABLE OF CONTENTS Page 3 INTENTIONALLY LEFT BLANK ...
Page 1209: ...2nd Edition Rev 0 SUPPLEMENT SG 1 TABLE OF CONTENTS Page 4 INTENTIONALLY LEFT BLANK ...
Page 1211: ...2nd Edition Rev 0 SUPPLEMENT SG 1 INTRODUCTION Page 2 INTENTIONALLY LEFT BLANK ...
Page 1229: ...2nd Edition Rev 0 SUPPLEMENT SG 1 CHAPTER 34 NAVIGATION Page 1 Chapter 31 Indicating system ...
Page 1230: ...2nd Edition Rev 0 SUPPLEMENT SG 1 CHAPTER 34 NAVIGATION Page 2 INTENTIONALLY LEFT BLANK ...
Page 1237: ...2nd Edition Rev 0 SUPPLEMENT SG 1 CHAPTER 34 NAVIGATION Page 6 INTENTIONALLY LEFT BLANK ...
Page 1239: ...2nd Edition Rev 0 SUPPLEMENT SG 1 CHAPTER 34 NAVIGATION Page 8 Garmin G500 LRUs location ...
Page 1241: ...2nd Edition Rev 0 SUPPLEMENT SG 1 CHAPTER 34 NAVIGATION Page 10 Pitot static line scheme ...
Page 1272: ...2nd Edition Rev 0 SUPPLEMENT SG 1 CHAPTER 34 NAVIGATION Page 41 INTENTIONALLY LEFT BLANK ...
Page 1273: ...2nd Edition Rev 0 SUPPLEMENT SG 1 CHAPTER 34 NAVIGATION Page 1 Chapter 34 Navigation ...
Page 1274: ...2nd Edition Rev 0 SUPPLEMENT SG 1 CHAPTER 34 NAVIGATION Page 2 INTENTIONALLY LEFT BLANK ...
Page 1276: ...2nd Edition Rev 0 SUPPLEMENT SG 1 CHAPTER 34 DESCRIPTION AND OPERATION Page 4 530W ...
Page 1278: ...2nd Edition Rev 0 SUPPLEMENT SG 1 CHAPTER 34 TROUBLESHOOTING Page 100 TROUBLESHOOTING ...