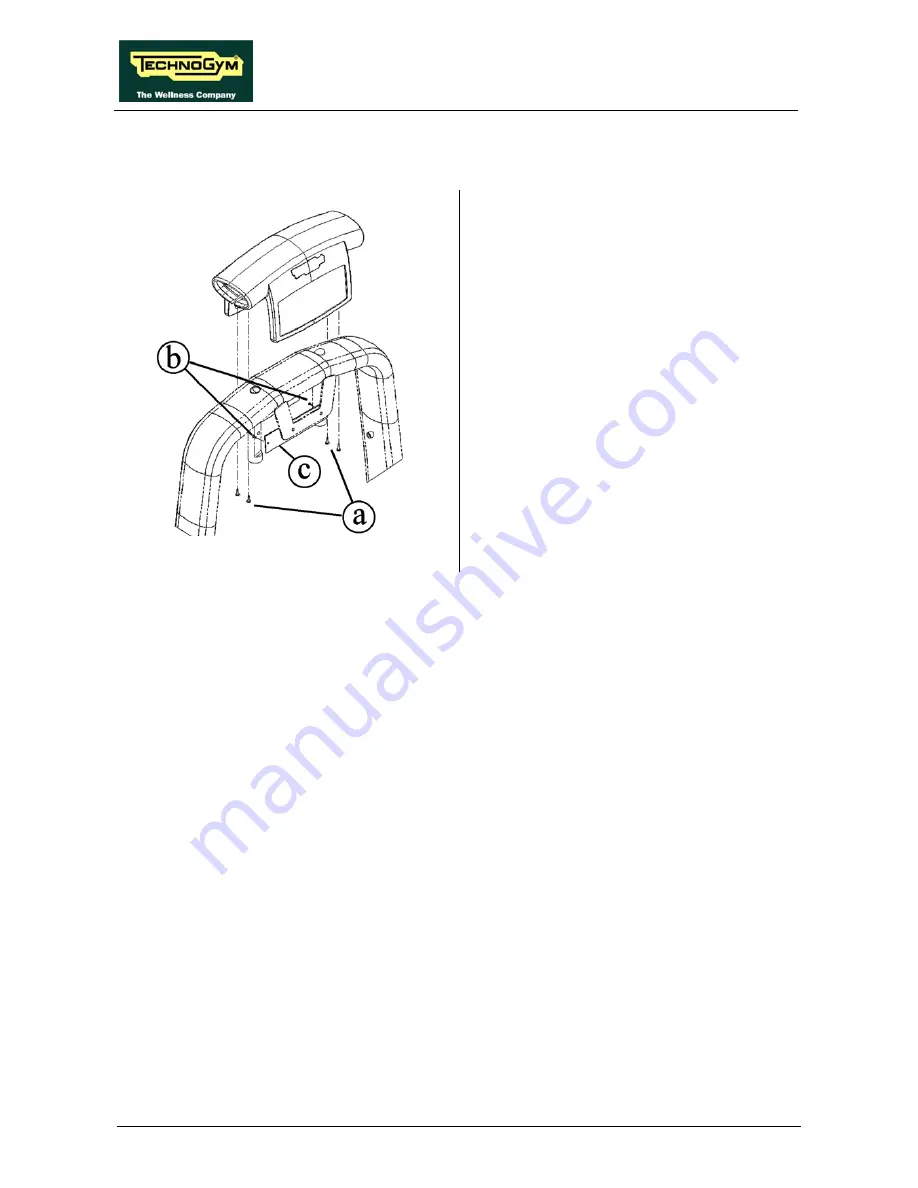
Personal Selection TÜV: Service & Maintenance Manual - rev. 1.0
Page 6.2
6.2. TOP
Photo 6.2-1
1. Back off the 4 screws
a
, using a medium
Phillips screwdriver.
2. Back of the self threading screws
b
on both
internal side of the top and remove the plates
c
.
3. Remove the Top from the machine.
4. Reassemble all the components, carrying out
the procedure in reverse order.