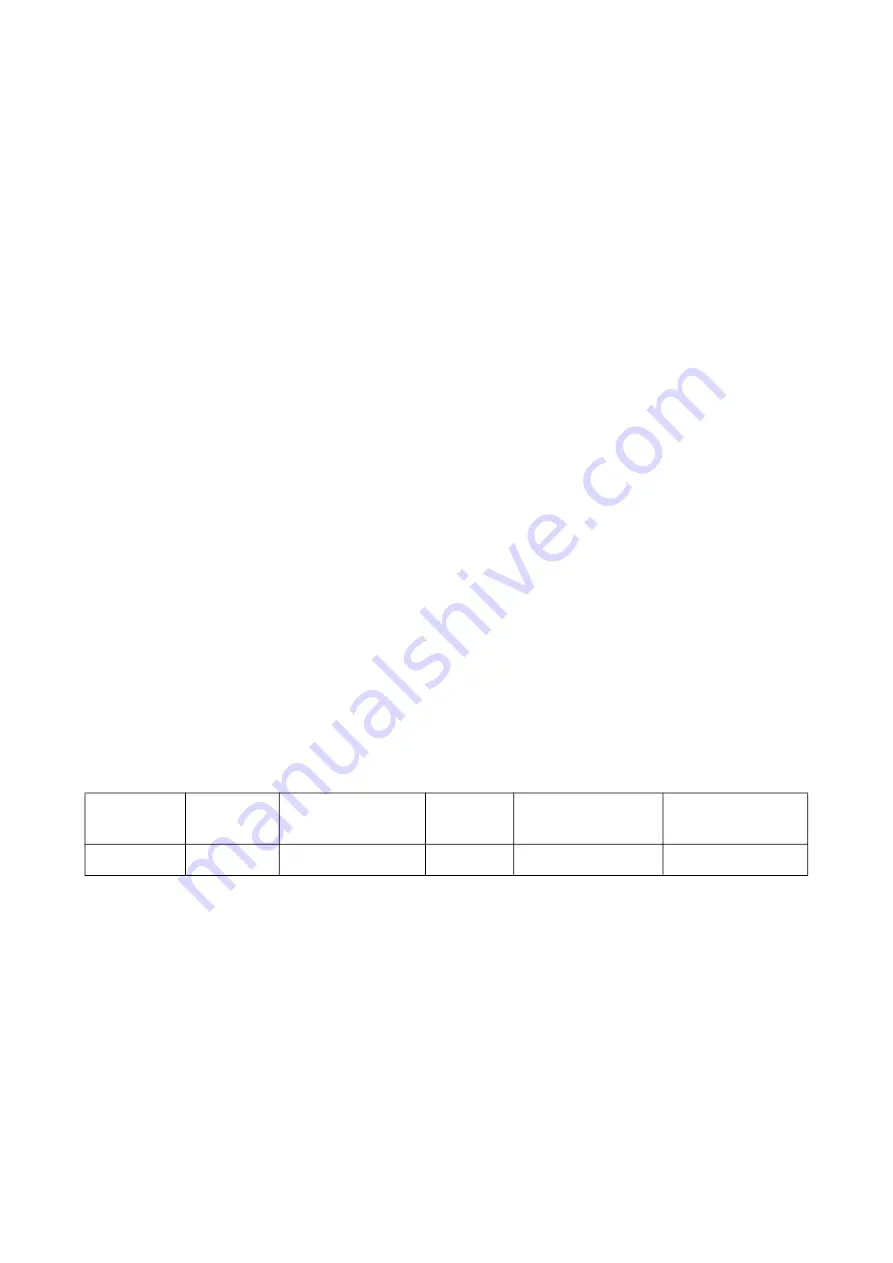
24
Troubleshooting – programming
The manufacturer can assist you in troubleshooting if you have the correct documentation and suf
-
ficient data to hand. The following are indispensable for this:
• a hydraulic scheme via fax or email (WMF, JPG),
• the complete program via TAPPS file or at least the function data (*.dat file) by email,
• operating system version and controller serial number,
• all existing log files or at least the (temperature) values of the inputs at the time the system mal
-
functioned,
• telephone contact for describing the problem – in most cases a written fault description is not
enough.
Troubleshooting in the CAN network
To isolate the error we recommend shutting down part of the network and monitoring when the error
disappears.
General tests:
• Node numbers – no node number must be assigned twice
• Power supply to BUS subscribers (if necessary use the CAN-NT power supply unit)
• Setting of the Baud rate (even when using the CAN BUS converter CAN-BC2)
Wiring test:
All nodes must be switched off for this test.
• Resistance across CAN-H and CAN-L
• If this is in excess of 70 Ω, it indicates incorrect termination.
• If the resistance is below 60 Ω, look for too many terminations or short circuits between
cables/leads.
• Check for short circuits across GND or screen and the signal cables.
• Check for earth loops – for this the screen is undone at each node and the current tested. If
there is a current flow, an earth loop has been created by an unwanted earth connection.
Information on the ECO-design Directive 2009/125/EC
1
Definitions according to Official Journal of the European Union C 207 dated 03/07/2014
2
The classification applied is based on optimum utilisation and correct application of the products.
The actual applicable class may differ from the classification applied.
3
Contribution of the temperature controller to seasonal central heating efficiency in percent, round
-
ed to one decimal place
4
No output active = standby / all outputs and display active
5
The class is defined on the basis of the programming of the heating circuit controller, in accordance
with the Ecodesign Directive.
Subject to technical modifications
© 2020
Product
Class
1,2
Energy efficien
-
cy
3
Standby
max. [W]
Power consump
-
tion typ. [W]
4
Max. power con
-
sumption [W]
4
RSM610
5
max. 8
max. 5
1,0
0,80 / 1,55
1,0 / 1,9