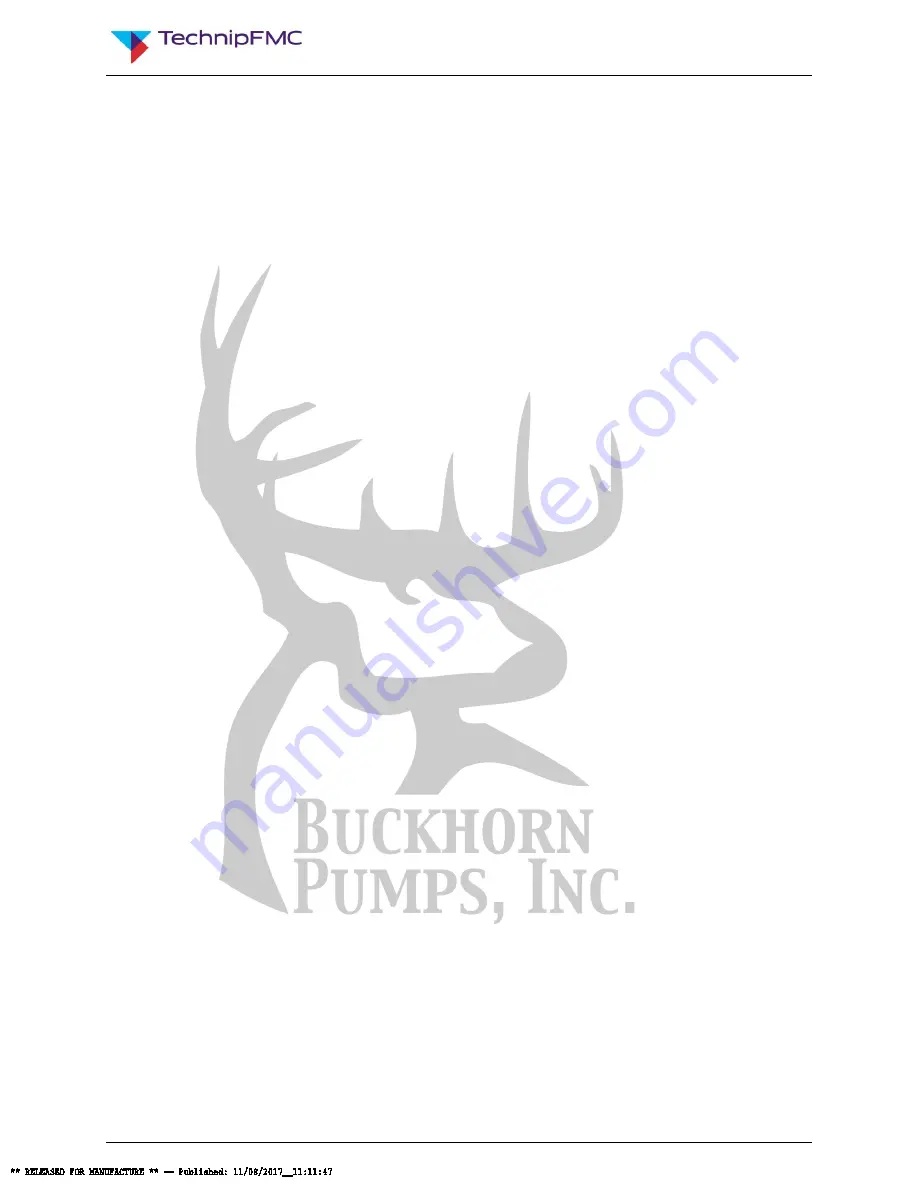
Doc No: OMM50001243
Rev: C Page 10 of 68
This document and all the information contained herein are the confidential and exclusive property of TechnipFMC,
and may not be reproduced, disclosed, or made public in any manner prior to express written authorization by TechnipFMC.
well as the suction and discharge manifolds. After the run, blow compressed air
through the fluid end to remove all traces of fluid. If possible, remove plugs from the
bottom of the fluid cylinder and push open the suction valve seats to ensure that all fluid
is drained from the pumping chamber between the suction and discharge valves.
As an alternative to the previous procedure, a compatible antifreeze solution can be
circulated through the fluid end. RV antifreeze, propylene glycol, is recommended for
this purpose. Remember that any fluid that poses an environmental hazard or is toxic
must be handled and disposed of properly.
4.0
Installation Guidelines
A proper installation is essential to optimal performance, long service life, and reduced
maintenance requirements. Take time to thoroughly plan all aspects of your installation.
4.1
General Location
It is important to position the pump on as flat and level a surface as possible to assist
the splash oil lubrication system. Park mobile equipment, such as drilling machines, on
as level a surface as possible. Whenever possible the pump should be mounted in a
clean, dry location with sufficient lighting and adequate space for easy inspection and
maintenance. Locate the pump as close to the suction source as possible to allow for
the shortest and most direct routing of the inlet piping.
4.2
Mounting Pump to Foundation and Power Source
The M06 pumps described in this document must be mounted in a horizontal position
only. Secure the pump to the mounting surface using the four (4) holes provided in the
pump base. Check motor or engine rotation direction to ensure that the top of the pump
crank shaft rotates toward the pump fluid end when in operation.
For units that are V-belt driven, check the alignment of the sheaves after the unit is
installed on its permanent mounting. Tighten belts to the proper tension as
recommended by the belt manufacturer. Verify that the sheaves are in line and parallel
to each other with a straight edge.