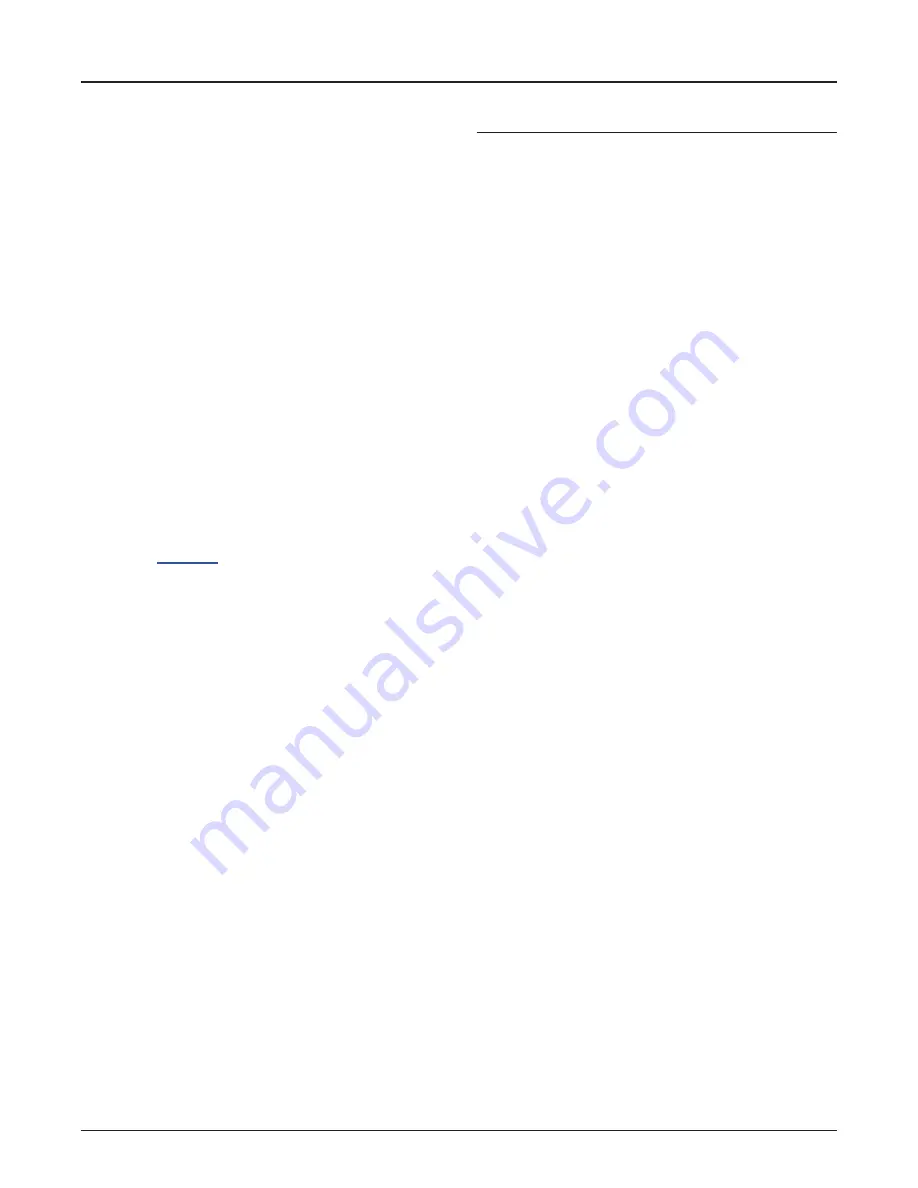
2 • MN02004
Issue/Rev. 0.3 (8/02)
Section 1 – General Information
It is suggested that a detailed record be maintained
for each meter. Nameplate data, progressive totalizer
readings, meter factor, parts used, and other similar in
-
formation provide background material for scheduling a
preventive maintenance program. An increase in meter
factor drift against throughput can be used as the basis
for making an inspection.
The time of the first inspection must be based on the
operating conditions imposed by the installation. Flow
rate, lubrication properties of the fluid, and the possibility
of abrasive contaminants are points to consider. Then,
at the time of inspection, the condition of the meter
should indicate whether the inspection interval could
be lengthened or shortened.
All parts, as they are removed, should be thoroughly
inspected and, if necessary, cleaned in solvent.
Before any disassembly is performed on the meter, be
sure the trouble is in the meter.
1. Check that the meter is being operated within the
proper flow rate. Refer to the nameplate on the side
of the meter.
2. Check pick-up coil and preamplifier for proper
operation. An oscilloscope will be necessary to
determine wave form of the pick-up coil. Refer to
for pick-up coil specifications and
Page 3 of this document for preamplifier information.
3. Check for electronic totalizer malfunction.
4. Check that the system flow temperature has
stabilized, that there are no abnormal pressure
fluctuations, and that there is proper system back
pressure.
5. Check valve operation in the system.
6. Check for air in the system.
After all other accessories have been checked and found
to be operating normally, the turbine meter should be
checked.
Before beginning any service procedure, stop product
flow, drain the line in the direction of flow (if possible),
and relieve the pressure from the system. Remove the
Sentry Series Turbine Meter from the line and take it to
a clean area for disassembly.
Return Procedures
No material can be returned from either a distributor
or customer without receiving a properly executed
Return Material Authorization (RMA). Once the RMA is
received, the material may be returned in accordance
with the instructions contained in the RMA.
Authorization for the return of either new or used ma
-
terial can only be granted by the Customer Service
Department of TechnipFMC.
If the material to be returned is new and unused, the
customer should supply the invoice number and/or the
shipping order number of the original purchase.
For any units that have been installed and could con
-
tain a residue of product, it is the responsibility of the
customer to properly flush and, if necessary, neutralize
the inside of the equipment in question. If not properly
accomplished, the customer must assume all respon
-
sibility for any injuries, property damages, or violations
of state or local statutes.
All items to be returned must be freight prepaid to the
TechnipFMC 1602 Wagner Avenue, Erie, Pennsylvania
16514 and shipped in accordance with all rules and
regulations of the Department of Transportation and
Environmental Protection Agency.