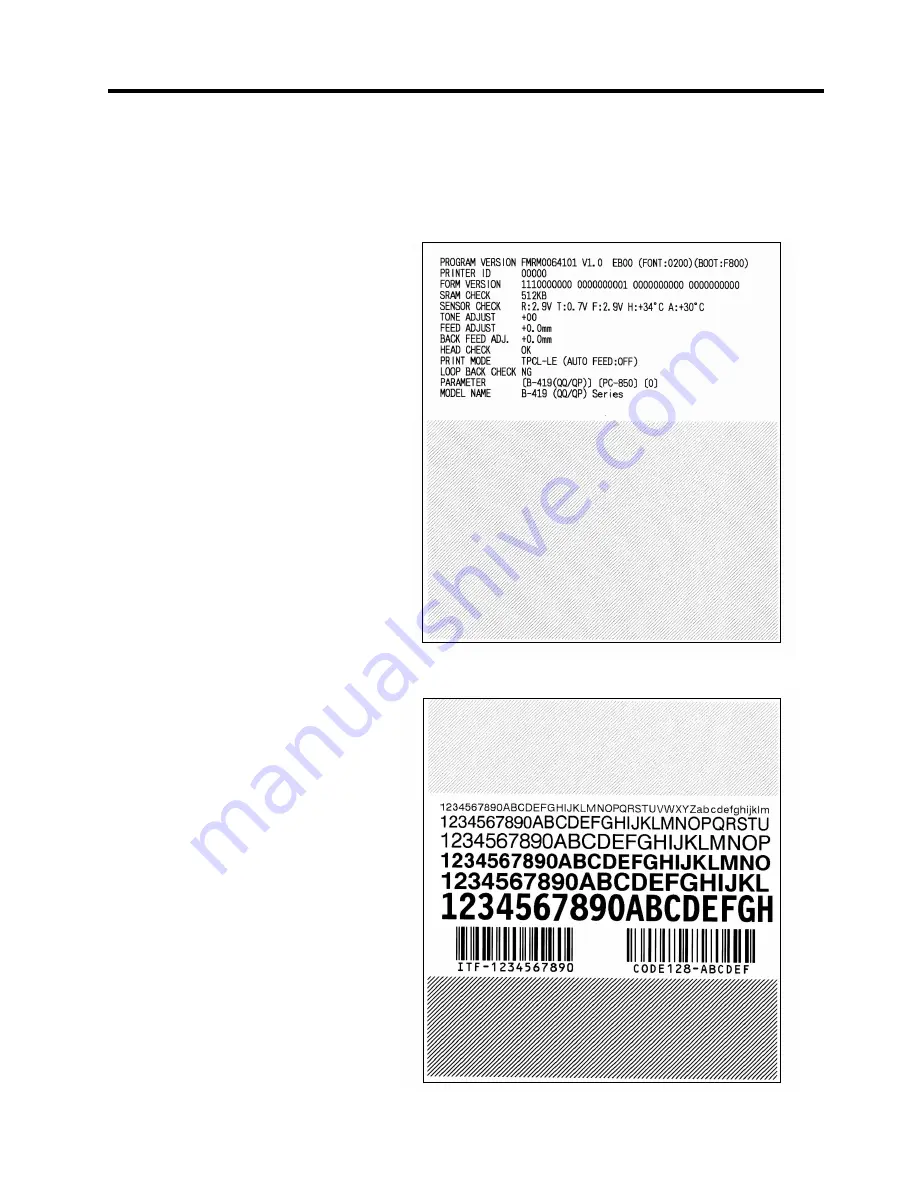
2. PRINTER SETUP
EO1-33030
2.9 Test Print
2- 10
2.9 Test Print
The following test procedure allows you to perform a print test to verify
that the printer is operating correctly.
1.
Load the media on the printer.
2.
Slide the Stand-by Switch to ON while holding the
[FEED]
button.
The printer will start a status print.
3.
After completing the status print, the test pattern is printed each time
the
[FEED]
button is pressed.
(1)
(2)
(3)
(4)
(5)
(6)
(7)
(8)
(9)
(10)
(11)
(12)
(13)
(14)
Summary of Contents for TEC B-419-GS10
Page 1: ...TEC Label Printer B 419 GS10 QQ Owner s Manual ...
Page 52: ......
Page 53: ......
Page 54: ...E PRINTED IN JAPAN EO1 33030 ...