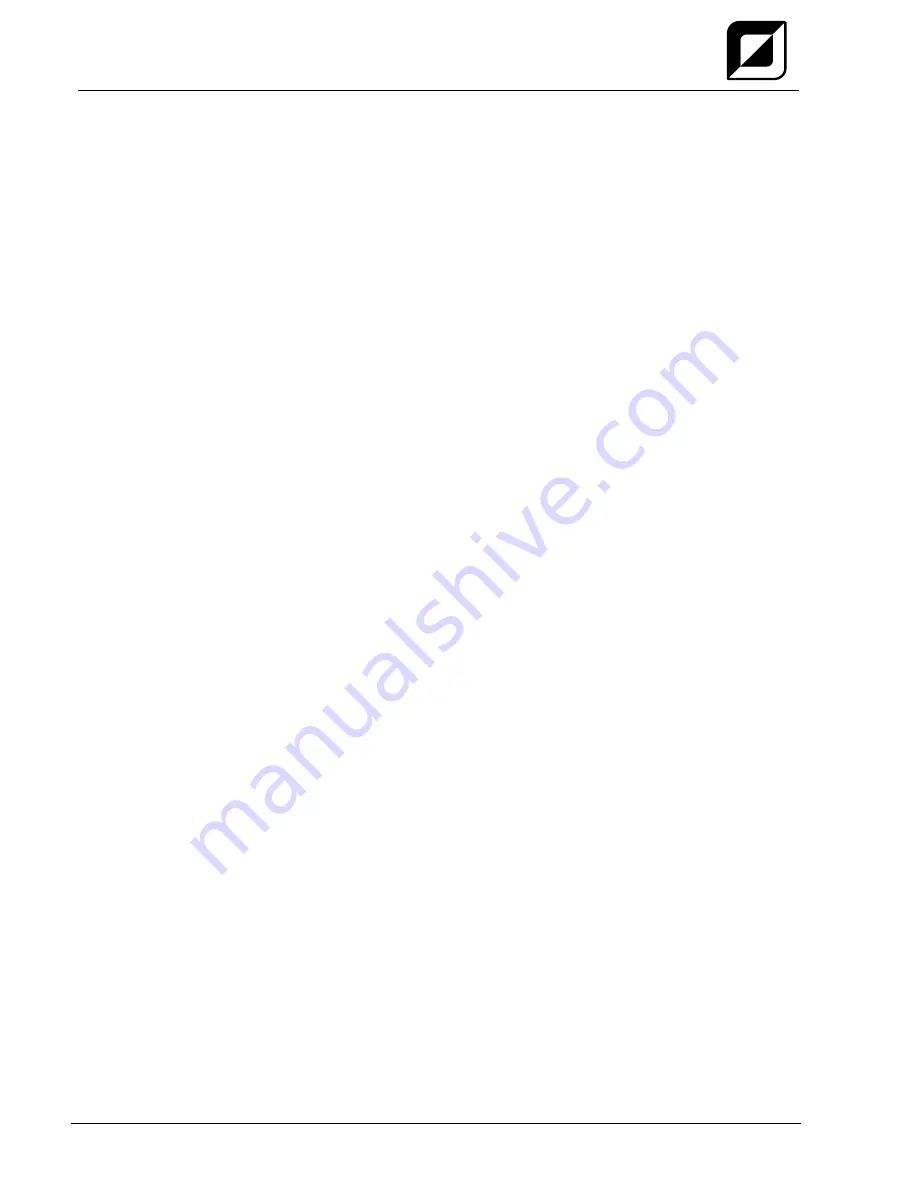
Contents
Notes on the use of these operating instructions
4
299-030200-TWD01
25.09.2015
6.3
Disposing of equipment ................................................................................................................ 39
6.3.1
Manufacturer's declaration to the end user .................................................................. 39
6.4
Meeting the requirements of RoHS .............................................................................................. 39
7
Rectifying faults .................................................................................................................................... 40
7.1
Checklist for rectifying faults ........................................................................................................ 40
8
Technical data ....................................................................................................................................... 41
8.1
MIG 250 S, 300 S ......................................................................................................................... 41
9
Accessories .......................................................................................................................................... 42
9.1
Internet ......................................................................................................................................... 42
10
Replaceable parts ................................................................................................................................. 43
10.1
Wire feed rollers ........................................................................................................................... 43
10.1.1
Wire feed rollers for steel wire ...................................................................................... 43
10.1.2
Wire feed rollers for aluminium wire ............................................................................. 43