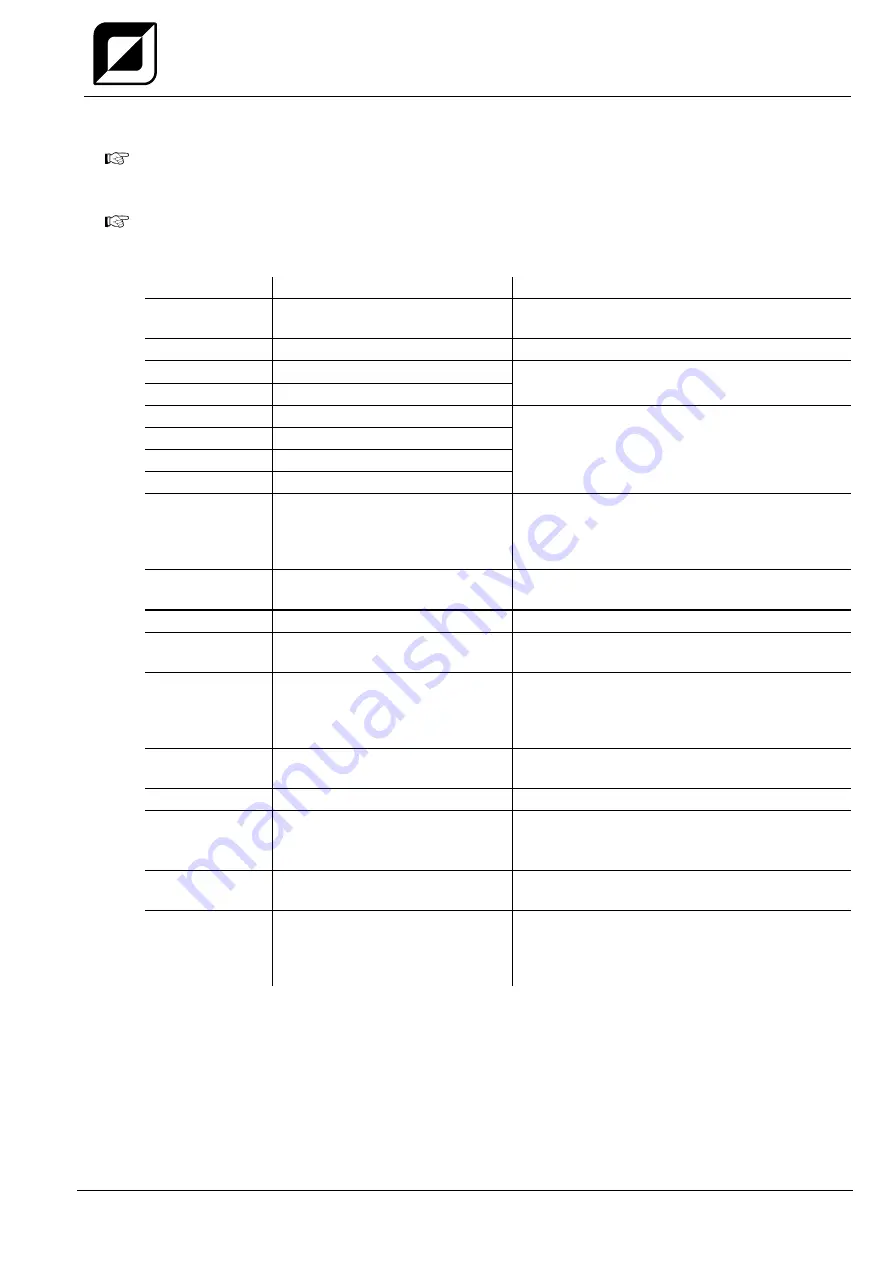
Rectifying faults
Machine faults (error messages)
299-020100-TWD01
18.03.2016
47
7.2
Machine faults (error messages)
A welding machine error is indicated by the collective fault signal lamp (A1) lighting up and an
error code (see table) being displayed in the machine control display. In the event of a machine
error, the power unit shuts down.
The display of possible error numbers depends on the machine version (interfaces/functions).
• If multiple errors occur, these are displayed in succession.
• Document machine errors and inform service staff as necessary.
Error message
Possible cause
Remedy
E 0
Start signal set in the event of
errors
Do not press the torch trigger or the foot-
operated remote control
E 4
Temperature error
Allow the machine to cool down
E 5
Mains overvoltage
Switch off the machine and check the mains
voltage
E 6
Mains undervoltage
E 7
Electronics error
Switch the machine on and off again.
If the error persists, notify service department
E 9
Secondary overvoltage
E12
Voltage reduction error (VRD)
E13
Electronics error
E14
Adjustment error in current
recording
Switch off the machine, place the electrode
holder in an insulated position and switch the
machine back on. If the error persists, notify
service department
E15
Error in on of the electronics
supply voltages
Switch the machine off and on again.
If the error persists, notify service department
E23
Temperature error
Allow the machine to cool down
E32
Electronics error
Switch the machine on and off again.
If the error persists, notify service department
E33
Adjustment error in voltage
recording
Switch off the machine, place the electrode
holder in an insulated position and switch the
machine back on. If the error persists, notify
service department
E34
Electronics error
Switch the machine on and off again.
If the error persists, notify service department
E37
Temperature error
Allow the machine to cool down
E40
Motor fault
Check wire feed unit,
switch the machine off and on again, inform the
service department if the fault persists.
E55
Failure of a mains phase
Switch off the machine and check the mains
voltage
E58
Short circuit in welding circuit
Switch off machine and check welding current
leads for correct installation, e.g., put down
electrode holder in an electrically insulated
manner, disconnect degausser current lead.