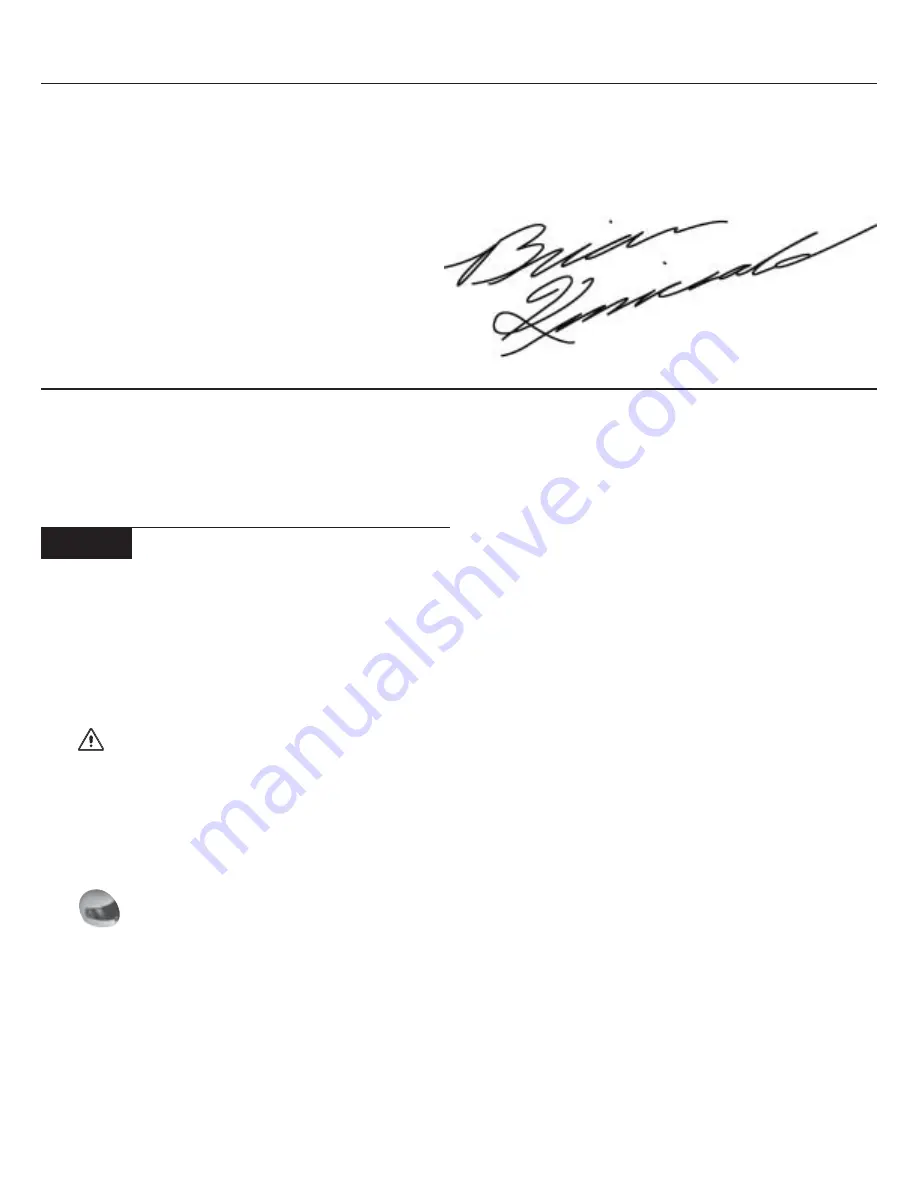
i
Welcome Team Losi Triple-X Owner!
Thank you for choosing the Team Losi
Triple-X Kinwald Edition. I have been fortunate to work and race for Team
Losi through the years. I owe a great deal of my success to their cutting edge designs and attention to detail.
This Kinwald Edition kit includes a large selection of more important specialty parts I used to win the recent ROAR
Modified 2 Wheel Drive National Championship. Before you start building your new
Triple-X, I suggest you read
through the instructions first. Be sure to check out the performance tips as you build and the tuning tips at the back of this
manual as well. I hope you enjoy your
Triple-X as much as I do mine.
Good luck, and thank you for choosing Team Losi.
1. INTRODUCTION
TRIPLE-X KINWALD EDITION COMPLETED KIT DIMENSIONS
Length: 14.875"
Front Width: 9.82"
Rear Width: 9.84"
Height: 5.125"
Wheelbase: 10.6"
All dimensions at ride height.
Weight will vary depending on accessories.
NOTES & SYMBOLS USED
Figure 1
This is a common figure number found at the beginning
of each new illustration throughout the manual.
!
Step 1. - Each step throughout the entire manual has a
check box to the left of it. As you complete each step, mark the
box with a check. If you need to take a break and return to build-
ing at a later time you will be able to locate the exact step where
you left off.
*NOTE: This is a common note. It is used to call attention to
specific details of a certain step in the assembly.
IMPORTANT NOTE:
Even if you are familiar with
Team Losi kits, be sure and pay attention to these notes. They
point out very important details during the assembly process. Do
not ignore these notes!
!
This wrench designates a performance tip. These tips
are not necessary, but can improve the performance of your
Triple-X car.
In illustrations where it is important to note which
direction parts are facing, a helmet like this one will be included
in the illustration. The helmet will always face the front of the car.
Any reference to the right or left side will relate to the direction of
the helmet.
KIT/MANUAL ORGANIZATION
The kit is composed of different bags marked A through G. Each
bag contains all of the parts necessary to complete a particular
section of the kit. Some of these bags have subassembly bags within
them. It is essential that you open only one bag at a time and
follow the correct assembly sequence, otherwise you may face dif-
ficulties in finding the correct part. It is helpful to read through
the instructions for an entire bag prior to beginning assembly.
Key numbers (in parenthesis) have been assigned to each part and
remain the same throughout the manual. In some illustrations,
parts which have already been installed are not shown so that the
current steps can be illustrated more clearly.
For your convenience, an actual-size hardware identifica-
tion guide is included with each step. To check a part, hold it
against the silhouette until the correct part is identified. In some
cases extra hardware has been supplied for parts that may be
easy to lose.
The molded parts in the kit are manufactured to demanding
tolerances. When screws are tightened to the point of being snug,
the parts are held firmly in place. For this reason it is very impor-
tant that screws not be overtightened in any of the plastic parts.
To ensure that parts are not lost during construction, it is
recommended that you work over a towel or mat to prevent parts
from rolling away.
IMPORTANT SAFETY NOTES
1. Select an area for assembly that is away from the reach of
small children.
Some parts in this kit are small and can be swallowed
by children, causing choking and possible internal injury.
2. The shock fluid and greases supplied should be kept out
of childrens' reach.
They are not intended for human consumption!
3.
Exercise care when using any hand tools, sharp instruments,
or power tools during construction.
4.
Carefully read all manufacturers' warnings and cautions for
any glues, chemicals, or paints that may be used for assembly and
operating purposes.