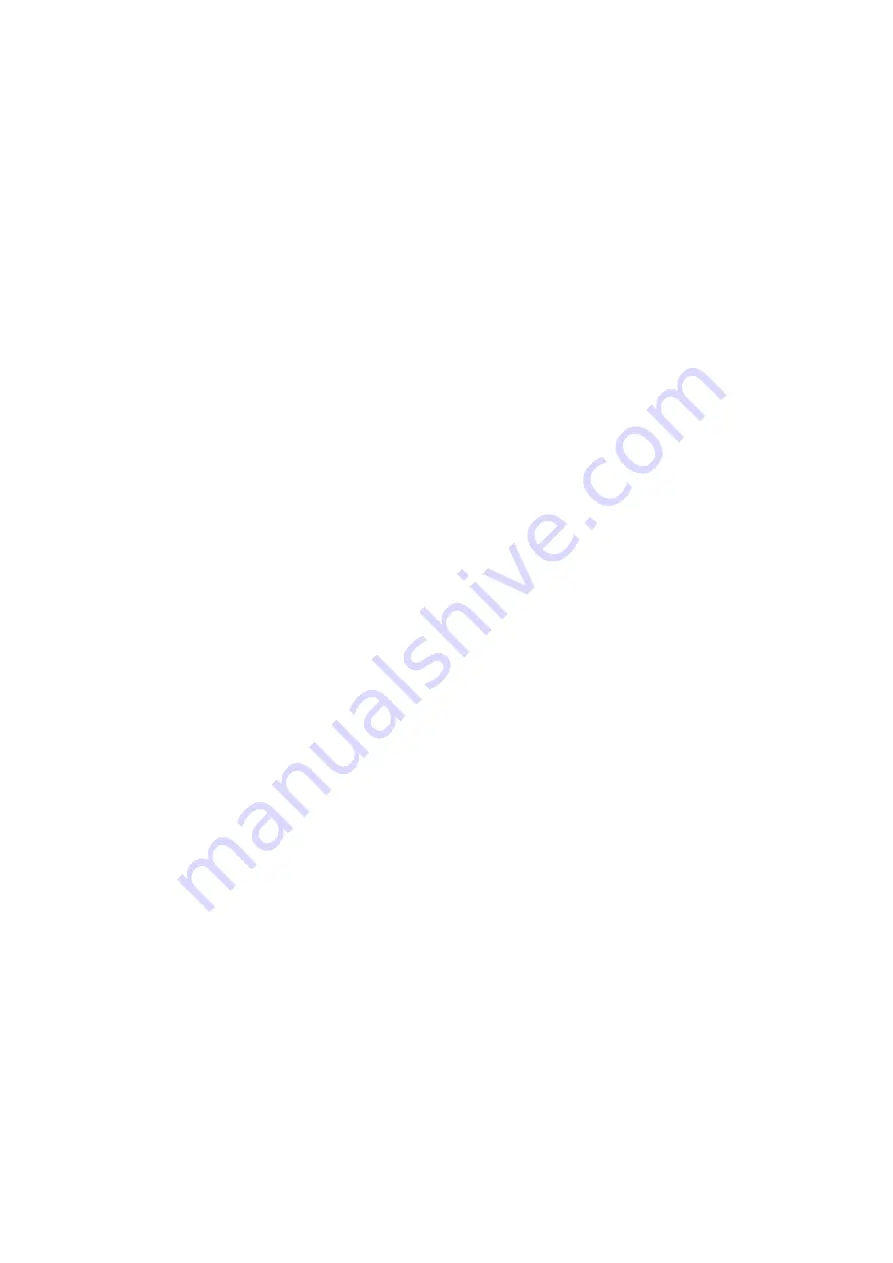
SECTION 7.
SOLENOID VALVE AND CONTROLS REPAIR
AND ADJUSTMENT.
6.1 Checking coils for correct operation.
The coil leads have an LED to indicate operation, it is no guarantee of a connection between the cap, and the coil
though.
Without the tractor engine running it is usually possible to hear the click of cartridge valves moving when the
switches are operated.
Remove the coil from the cartridge valve by unscrewing the retaining nut being careful not to lose the ’O’ ring be-
hind the nut. With the switch on the control desk operated, the magnetic effect of the coil should be detectable on
a screwdriver placed inside the coil.
If the magnetic effect cannot be detected try a different coil attached to the same lead or alternatively check for a
switched current on the lead with a multimeter. If there is no switched electrical current at the coil connector it may
be a fault in the wiring, switch or connector on the cab control desk which can only be traced with the aid of a
multimeter /test lamp.
6.2 Removal of the proportional cartridge.
Remove the coil from the proportional cartridge valve by unscrewing the retaining nut being careful not to lose the
’O’ ring behind the nut.
Removal of the cartridge is best effected with the use of tool HYD5336 which allows the cartridge to be removed
by a 1” AF deep socket. Where the tool HYD5336 is not available then adjacent components may have to be
removed to obtain access with a 9/16” AF open ended spanner.
Reattach the proportional coil to the cartridge and operate through the bed chain speed control range. A variable
opening of the cartridge should be noted.
6.3 Diagnosing bale chamber electronic circuit for faults.
Diagnostics can only be achieved with the use of a multimeter capable of measuring a variable voltage in the
range 0-12v.
6.3a Bluetooth controls.
Measure the varying voltage at the connector to the coil, a variation of 6v in a range from 4v to 10v should be
measured. If the above satisfactory readings cannot be obtained then one of the two following faults has occurred:
1.
Bale chamber max and min values need adjustment usually indicated by a variable voltage outside the giv-
en range.
2.
Control desk potentiometer or circuit board has failed - refer the control desk to Teagle Machinery Ltd for
repair.
3.
Note: Control desks are available on an exchange basis to prevent any unnecessary down time.
6.4 Replacing junction box circuit boards.
Remove the valve block cover and the junction box lid. The majority of the electronic components are on a PCB
removable card (EC2007). The PCB card can be removed for repair by carefully pulling on the PCB card and
disconnecting all the multi-switches. Replace with the fixed – PCB card and re-connect the mulit-switches. Re-
place the other components and plug the power lead in. You should hear a click sound when the power is con-
nected. Follow the instructions in section 1 to connect the control desk and the junction box.
6.5 Removal of manifold to clean pilot orifice.
Firstly disconnect the 1 or 2 electrical connectors from the coils.
With a 5mm Allen Key remove the 2 socket head
cap screws retaining the manifold assembly onto the valve body.
The pilot orifice can now be inspected for contamination and cleaned.
Refit the O rings in the correct position. These are a special hard compound, and only original equipment should
be used. Assemble the manifold back onto the valve. The 2 socket head cap screws should be refitted with a
thread locking liquid applied to the thread and tightened to a torque of 20.3 Nm (15 lbft).
25
Summary of Contents for Tomahawk C12
Page 1: ......
Page 11: ...10 Section 4 2 Identifying hydraulic slices components Notes ...
Page 20: ...19 Section 4 4 Hydraulic Hoses Fittings ...
Page 28: ......