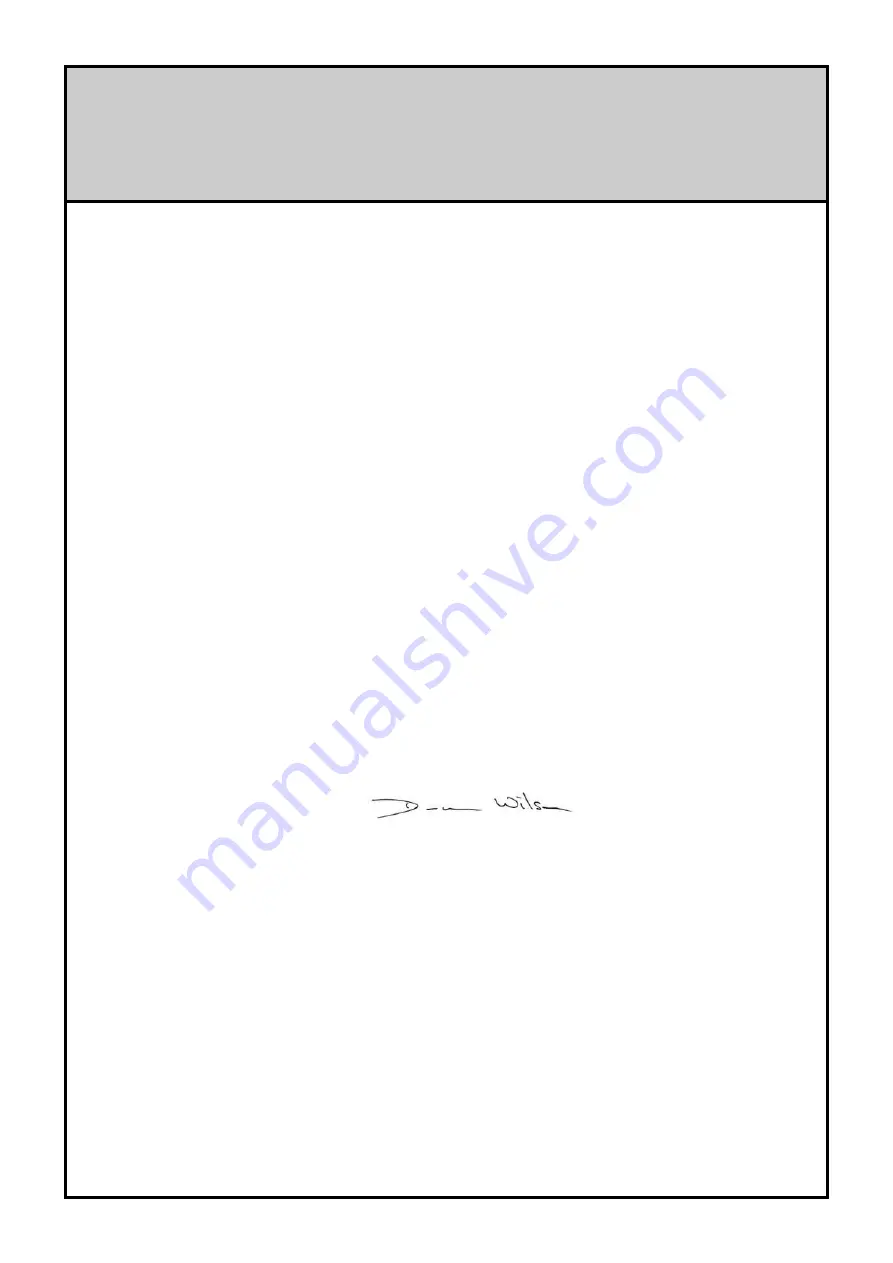
EC Declaration of Conformity
conforming to EEC Directive 2006/42/EC
Teagle Machinery Ltd.
Blackwater
Truro
Cornwall
TR4 8HQ
United Kingdom
declares in sole responsibility that the
Tomahawk 404M & 505M Hammer Mill
Tomahawk 4040 & 5050 Silage Feeder
to which this certificate applies
conforms to the essential Health and Safety requirements of
EEC Directive 2006/42/EC & 2004/108/EC.
To effect correct application of the essential
Health and Safety requirements stated in
the EEC Directives, the following harmonised standards were consulted:
BS EN ISO 12100-1
BS EN ISO 12100-2
BS EN ISO 13857:2008
Signed:
Duncan Wilson
(Engineering Director)
Dated: 8
th
August, 2017
Person authorised to compile Technical File
Duncan Wilson,
Teagle Machinery
Blackwater, Truro
Cornwall, TR4 8HQ
United Kingdom
Machine Serial No. . . . . . . . . .