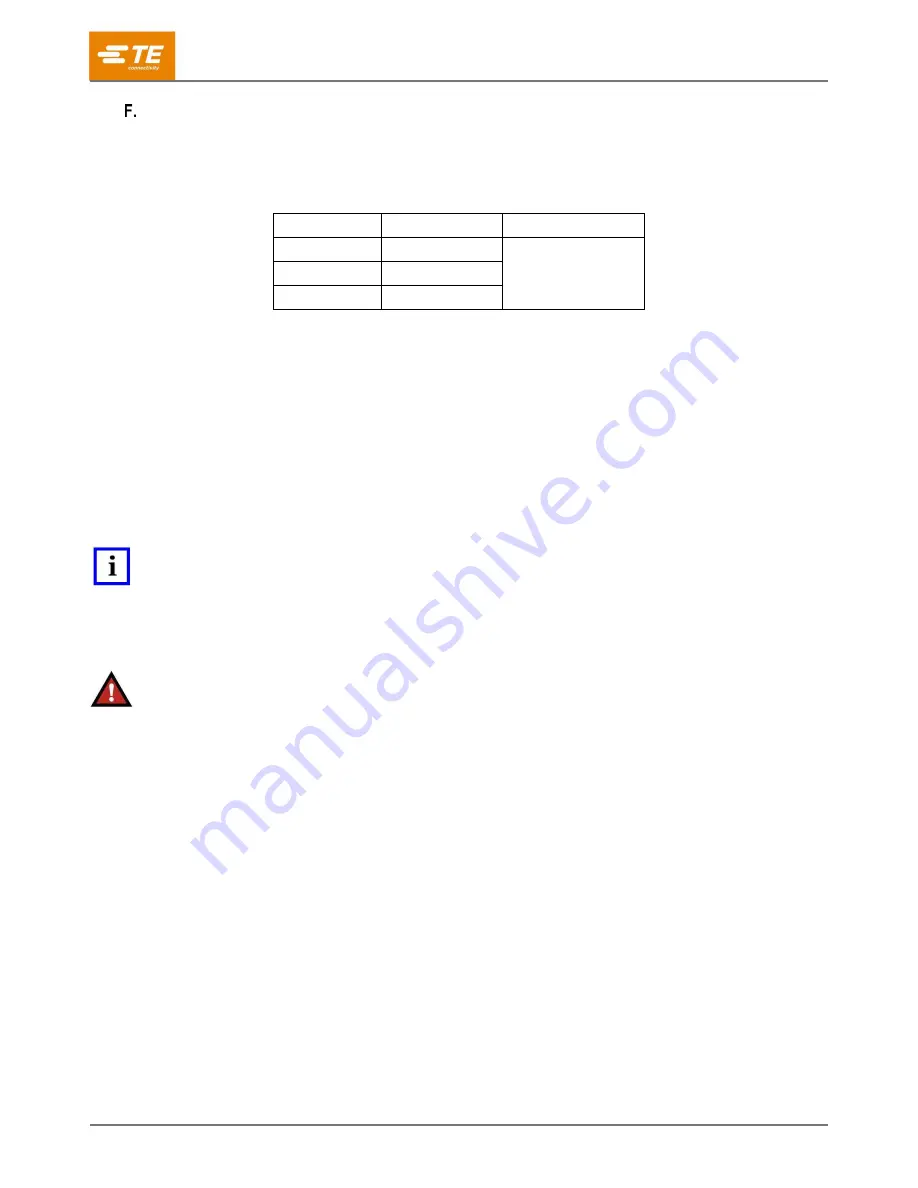
409-1950
Rev G
10
of 22
Latch pin kit
The latch pin kit consists of a latch pin, pivot pin, and coupling assembly. Assembly instructions are
provided in the instruction sheet packaged with the kit.
Table 10: Latch pin kit part numbers
Latch pin kit Crimping head Instruction sheet
67909
69051
408-2096
67909-2
69065
67909-3
69066
3.
RECEIVING INSPECTION
1. Carefully inspect the pump upon arrival for evidence of damage that may have occurred in transit. If
damage is evident, file a claim against the carrier and notify TE Connectivity.
2. Check all components to make sure that they are secure.
3. Check all wiring for loose connections, cuts, or other possible causes of electrical short circuits.
4. Inspect all air lines for evidence of loose connections and cuts that may cause leakage.
4.
SETUP
NOTE
Keep the pump in an upright position at all times.
4.1.
Installing the Casters
Install the casters into the sockets in the bottom corners of the pump. The casters are not required unless the
pump is used in portable applications.
DANGER
Use the casters whenever possible while moving the pump. Two people are needed to lift the pump.