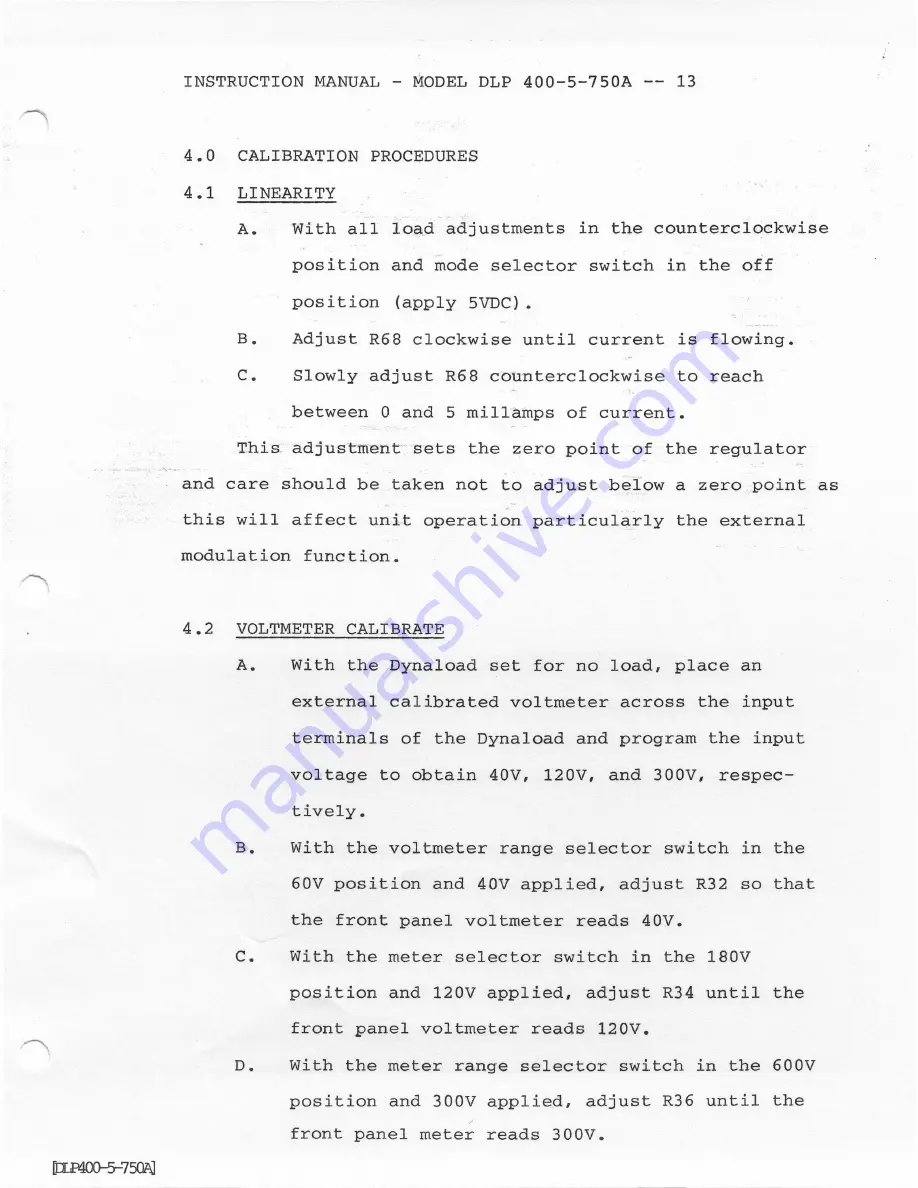
INSTRUCTION
MANUAL
-
MODEL
DLP
400-5-750A
13
4.0
CALIBRATION PROCEDURES
4.1
LINEARITY
A.
With
all
load
adjustments
in
the counterclockwise
position
and
mode selector switch
in
the
off
position
(apply
5VDC)
.
B.
Adjust
R68
clockwise
until
current
is
flowing.
C.
Slowly
adjust
R68
counterclockwise
to
reach
between
0
and
5
millamps
of
current.
This
adjustment
sets
the
zero
point
of the
regulator
and
care
should
be
taken
not
to
adjust
below
a
zero
point
as
this
will
affect
unit
operation
particularly the external
modulation
function.
4.2 VOLTMETER
CALIBRATE
A.
With
the
Dynaload
set
for no
load,
place
an
external
calibrated
voltmeter
across
the
input
terminals
of
the
Dynaload
and program
the
input
voltage to
obtain
40V,
120V,
and
300V,
respec
tively
.
B.
With the
voltmeter
range
selector
switch in
the
60V
position and
40V
applied,
adjust
R32
so
that
the
front
panel
voltmeter
reads
40V.
C.
With
the
meter selector
switch in
the
180V
position
and
120V
applied,
adjust
R34
until
the
front
panel
voltmeter
reads
120V.
D.
With
the
meter
range
selector
switch in
the 600V
position and
300V
applied, adjust
R36
until
the
front
panel
meter
reads
300V.
[ELF400-5-75QA]