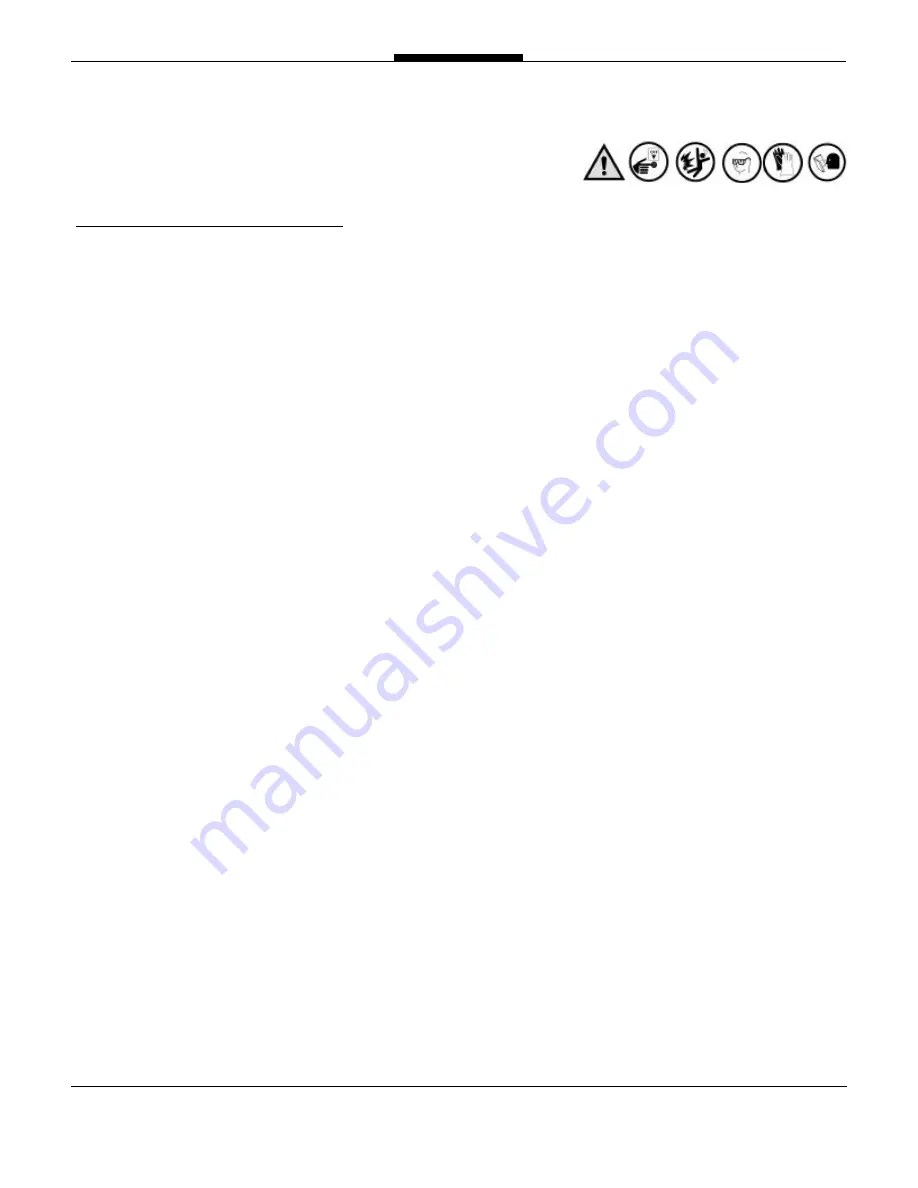
Page 17
Split Compartment Test (Continued)
Single Compartment Test Procedure:
The test of single-compartment tanks is easier to accomplish if there is a quick-connect hose coupling be-
tween the compartment valve and the pump that supplies product to the meter. If the system does not have
quick-connect couplings between the compartment and the meter, an additional source of sufficient prod-
uct at the test site is required.
Without a quick-connect coupling:
1). Begin the tests with the compartment containing an amount of fuel equal to or less than one-half the
nominal capacity of the prover being used. Operate the meter at the normal full flow rate until the
supply tank is empty. There are several methods for determining that the tank is empty. There may
be significant change in the sound of the pump. Someone may visually watch for the tank to run dry.
The meter may stop entirely or may begin to move in jumps (pause, resume running, the pause, then
run again).
2). Continue the test until the meter indication stop entirely for at east 10 seconds. If the meter stops for
at least 10 seconds, proceed to step 3. If the meter indication fails to stop entirely for at least 10
seconds, continue to operate the system for 3 minutes.
3). Close the compartment valve and the delivery nozzle or valve if top filling. Stop the pump and load
sufficient product from the alternate source into the supply compartment for the meter being tested.
Allow the product to stand in the compartment for a brief time to allow entrained vapor or air to
escape.
4). Open the compartment valve and restart the pump without pump resetting the meter to zero. Care
fully open the nozzle of valve at the end of the delivery hose. Pockets of vapor or air may cause
product to splash out of the prover. The test results may not be valid if product is splashed out of the
prover. Appropriate attire and protection is required, but caution is still necessary.
5). Continue delivery of product at the normal full flow rate until the liquid level in the prover reached
the nominal capacity of the prover.
6). Close the delivery nozzle or valve, stop the meter, and allow any foam to settle, then read prover
sight gauge.
7). Compare the meter indication with the actual delivered volume in the prover.
8). Calculate the meter error, apply Product Depletion test tolerance, and determine whether or not the
meter error is acceptable. Reference the NIST Handbook 44 for further information.
Summary of Contents for 700-30
Page 9: ...Page 9...
Page 10: ...Page 10...
Page 22: ...Page 22 700 30 700 35 Meter Assembly...
Page 24: ...Page 24 730 Air Eliminator Assembly...
Page 28: ...Page 28 750 30 Hydraulic Preset Valve Assembly Front Pull Side Swing...
Page 54: ...Page 54 Notes...