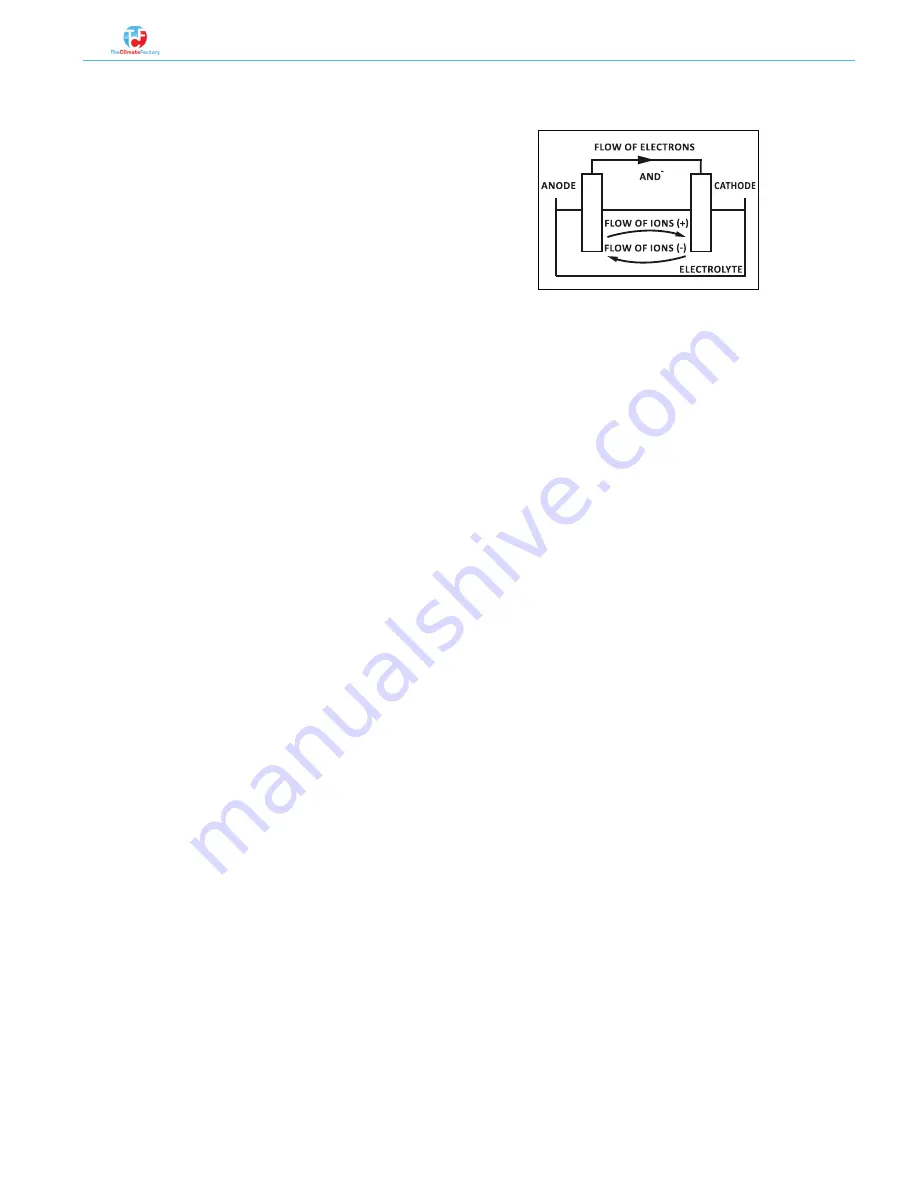
ANL - ANLH 020-202
6
BASIC PRINCIPLES ON MICROCHANNEL COIL
CORROSION
The main material in AERMEC heat exchangers is alu-
minium. Aluminium is a very reactive material, whose
surface is easily oxidized. As long as this hard layer of
aluminium oxide remains intact, the aluminium at the base
will remain corrosion resistant. For other materials, for
example steel, the oxide layer detaches from the surface
and peels off, thereby allowing the underlying metal to be
constantly attacked.
Extreme environments may, however, damage the layer of
oxide that could not be regenerated as quickly as neces-
sary to provide suffi cient protection to the product. These
hostile environments are distinguished by very high or
very low levels of pH. Normally, the protective oxide of
aluminium is generally stable in the pH range of 4.5 and
8.5. For this reason, sea water with neutral pH does not
intrinsically corrode aluminium. Galvanic corrosion is the
reason why precautions are required in marine environ-
ments for heat exchangers with aluminium cooling louvers
and copper piping.
Galvanic corrosion occurs when different metals come
into contact through an electrolyte. Because of an elec-
trochemical reaction, electrons detach from one of the
metals (reduce), whereas the other metal increases the
electrons (oxidized).
The role of each metal is determined by the respective
galvanic potential, typically summarised by the galvanic
series. The metal with the lower galvanic potential will be
reduced (consumed), whereas the metal with higher po-
tential will be oxidized, thereby becoming more resistant.
In the case of aluminium and copper (for example in the
presence of salt water), the aluminium will be sacrifi ced
in favour of the copper. It is customary for AERMEC to
custom design the chemistry and the selection of materials
to make sure that the fi rst component to corrode is a fi n
structure. The pipe that carries the refrigerant, which has
a round or microchannel section, is the component of the
most protected exchanger since perforation would cause
the refrigerant to leak.
Pitting corrosion is nothing else than the localised version
of galvanic corrosion. The different material is often an
inclusion in the same base metal alloy. Often, the sur-
face treatment, for example thermal zinc spraying (with
low galvanic potential), are those used most in order to
create general corrosion, which acts laterally across the
surface of the part, which is a preferable corrosion to di-
rect downward corrosion through a cavity, so as to avoid
perforation.
Anthill or ant-nest corrosion is a poorly known phenome-
non which takes its name from the morphology that is
similar to that of a nest of ants. It can be best described
as micro-pitting because the cavities on the surface are
generally so small that they are invisible to the naked eye.
This type of corrosion occurs more commonly in copper
pipes. The ant-hill corrosion
is caused by the chemical reaction which requires three
components: oxygen, water and an organic acid.
1. GENERAL INSTRUCTIONS FOR THE INSTALLER