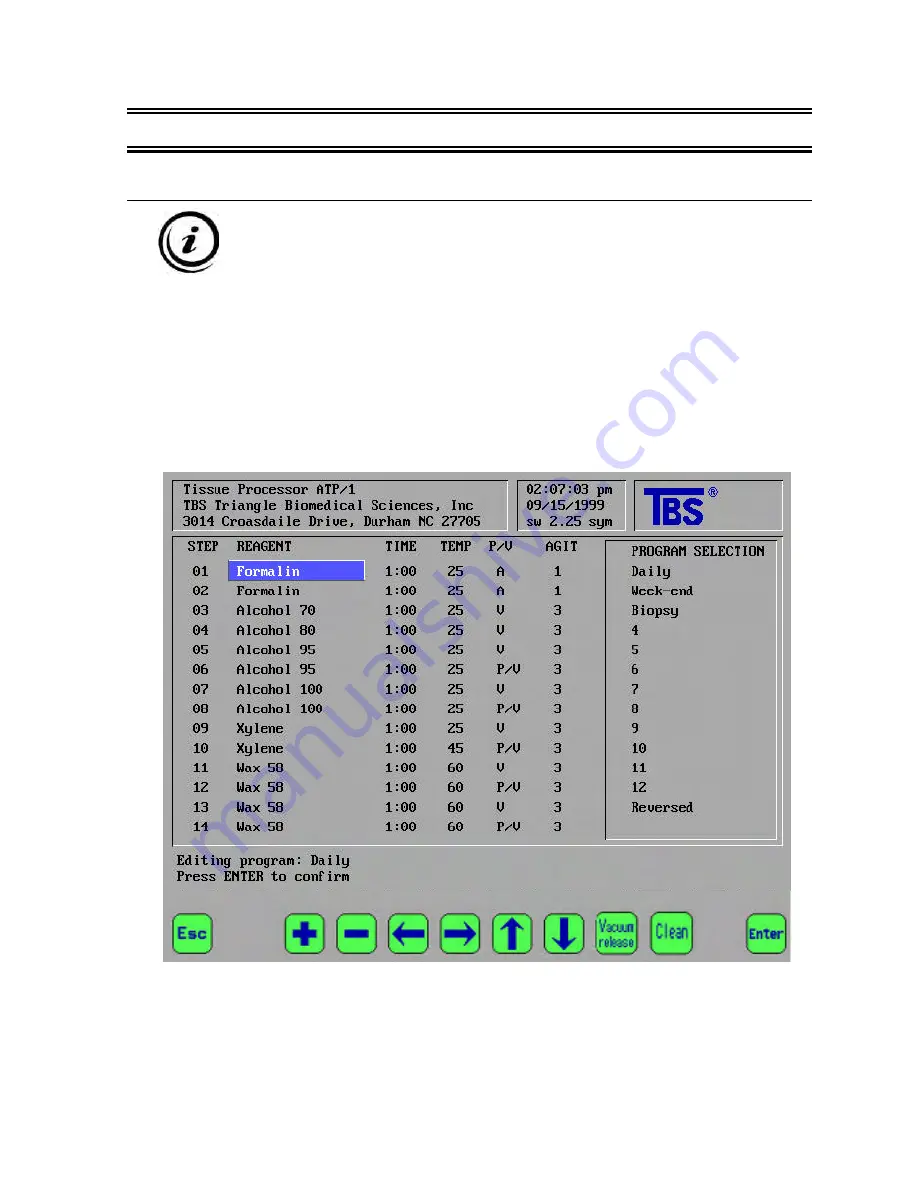
27
CHAPTER
8
–
PROGRAMMING
PROCESSES
8 . 1
–
P
R O G R A M M I N G
P
R O C E S S E S
To define new or edit existing programs, the Program Label must exist,
and any reagents to be included in the program must already be
defined.
1. Select
EDIT PROGRAMS
from the
MAIN
menu.
2. From the menu on the right side of the screen, use the arrows to select which
program you would like to edit. Once highlighted, press
ENTER
The
Edit Programs Screen
will appear.
Use
↑
and
↓
arrows to select the process to edit/change.
Use
ENTER
to start editing the selected process.
Use the
ARROW
keys to move through the process data: Reagent name,
Processing Time, Temperature, Pressure/Vacuum and Agitation.