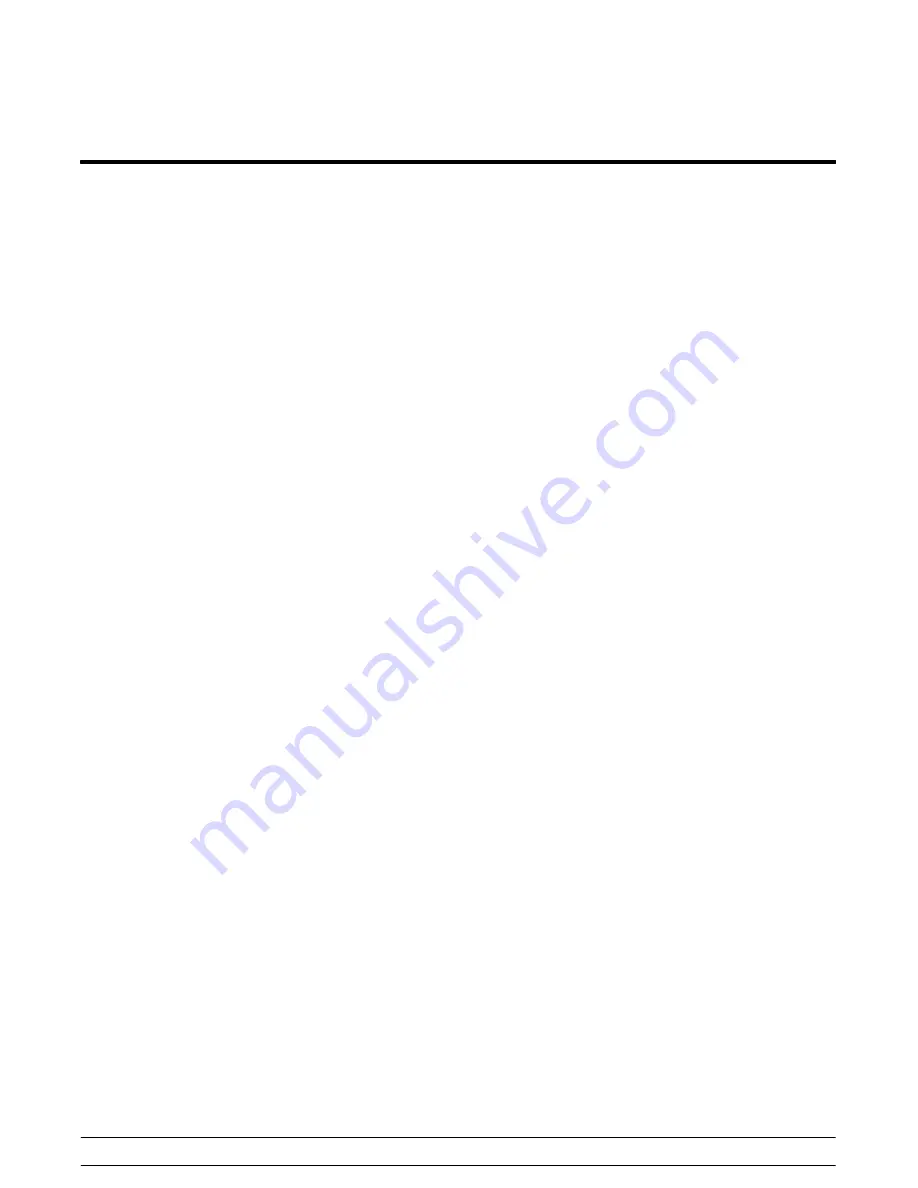
27
Models 150, 152, 162, 168
Troubleshooting Guide
Control Troubleshooting
Temperature Control Service Tips
Fill the bulb well with antifreeze before installing the
temperature control sensing bulb.
Use pliers to install the sensing bulb carefully into the
bulb-well. Feed one inch (2.5 cm) of the bulb into the
well at a time. This will help prevent the sensing bulb
from becoming kinked and more difficult to install.
Be sure the sensing bulb is installed completely into
the bottom of the bulb-well.
Viscosity Service Tips
The amount of mix in the freezing cylinder will affect
the finished product viscosity and temperature.
Example #1
The cylinder is overloaded with mix. The beater motor
wattage is increased and the set point on the control
is reached too soon. When the freezer cycles off, the
product is warm and appears wet.
Example #2
Not enough mix is in the freezing cylinder. With less
amperage load on the beater motor, the product must
become much thicker than normal to reach the control
set-point and to cycle off the freezer. Extremely long
running times and a loss of ejection indicate that the
cylinder is “starved” of mix.
The Watt control will compensate for voltage
fluctuation within the controls operating electrical
specification (
"
10%). In order to maintain a
consistent product viscosity, the amperage at cycle-off
will vary slightly when the voltage supply to the freezer
changes.
(Old Style Only)
On the front of the Watt control, next to the viscosity
adjustment potentiometer, there are two additional
potentiometers. CAUTION: DO NOT ATTEMPT TO
ADJUST THESE POTENTIOMETERS, as this will
alter the operating ranges and differential in the
control.
The Watt viscosity control will cycle the compressor off
when drawing product if the viscosity setting is
achieved. The Watt control relay will re-close (socket
connection #2 and #3) to bring the compressor back on
when the beater motor amperage drops approximately
.25 amps below the viscosity set-point.
Check the wire connections to the Watt control before
replacing a suspected faulty control. If a poor
connection interrupts L1 or L2 power to the control, the
Watt control relay will always remain closed and a
freeze-up condition will occur.
TQC Service Tips
The amount of mix in the freezing cylinder will affect
the finished product viscosity and temperature.
Example #1
The cylinder is overloaded with too much mix. The
beater motor amperage is increased and the set-point
on the TQC is reached too soon. The freezer cycles off
at a warmer temperature and the product appearance
is too soft.
Example #2
Not enough mix is in the freezing cylinder. With less
load on the beater motor, the product must get thicker
than normal to reach the TQC setpoint and cycle the
freezer off. Extremely long running times and a loss of
ejection indicate that the cylinder is “starved” of mix.
The TQC cycle-off amperage setting should never
exceed the FLA rating of the beater motor.
The TQC will cycle the compressor off when drawing
product, if the viscosity setting is achieved. The TQC
relay will re-close (socket connection #2 and #3) to
activate the compressor when the beater motor
amperage drops 1/2 amp below the TQC viscosity
setting.
On the front of the TQC, next to the viscosity
adjustment potentiometer, there is another small
adjustment potentiometer. CAUTION: DO NOT
ATTEMPT TO ADJUST THE SMALL
POTENTIOMETER as this will alter the operating
ranges of the control.
Check the TQC wire connections before replacing a
control that is suspected to be faulty.
Example: If a poor connection interrupts L1 or L2
power to the control, the TQC relay will always remain
closed and a freeze-up condition will occur.
Summary of Contents for Taylormate 150
Page 2: ......
Page 18: ...14 Controls and Systems Models 150 152 162 168 130521 Refrigeration Schematic Figure 5 ...
Page 35: ...31 Models 150 152 162 168 Parts Notes ...
Page 36: ...32 Parts Models 150 152 162 168 160210 Model 150 Exploded View Figure 9 ...
Page 40: ...36 Parts Models 150 152 162 168 160210 Model 152 Exploded View Figure 12 ...
Page 42: ...38 Parts Models 150 152 162 168 Model 162 Exploded View Figure 13 ...
Page 46: ...42 Parts Models 150 152 162 168 Model 168 Exploded View Figure 16 ...
Page 72: ...Model 150 152 050416 12 11 15 Taylor Company 2015 Carrier Commercial Refrigeration Inc c ...
Page 73: ...Model 150 152 050416 27 11 15 Taylor Company 2015 Carrier Commercial Refrigeration Inc c ...
Page 74: ...Model 150 152 050416 40 11 15 Taylor Company 2015 Carrier Commercial Refrigeration Inc c ...